Heat Exchanger Monitoring and End of Cycle Prediction
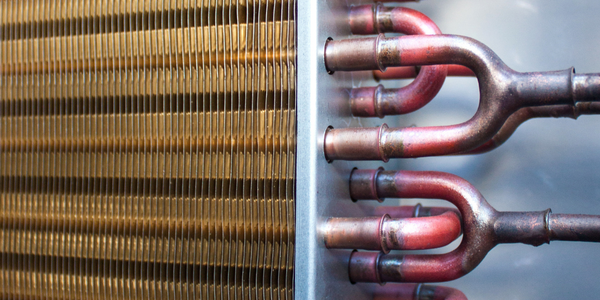
- Analytics & Modeling - Predictive Analytics
- Maintenance
- Predictive Maintenance
Predicting end-of-cycle (EOC) for a heat exchanger due to fouling is a constant challenge faced by refineries. Proactively predicting when a heat exchanger needs to be cleaned enables risk-based maintenance planning and optimization of processing rates, operating costs, and maintenance costs. Before using Seeq, the engineer had to manually combine data entries in a spreadsheet and spend hours/days formatting and filtering the content or removing non-relevant data when necessary (for example when equipment was out-of-service).
Utilizing the Seeq Formula Tool to monitor heat exchanger performance in the place of time-consuming spreadsheets will eliminate weeks of work for engineers, freeing them up to perform other valuable company tasks. The same formulas can be applied to many other exchangers, so users can focus on other continuous improvement projects instead of continually monitoring many spreadsheets. Millions of dollars could be saved per year as a result of improved turnaround planning and other improvement opportunities.
Related Case Studies.
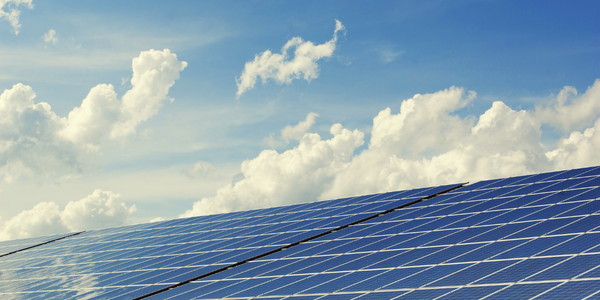
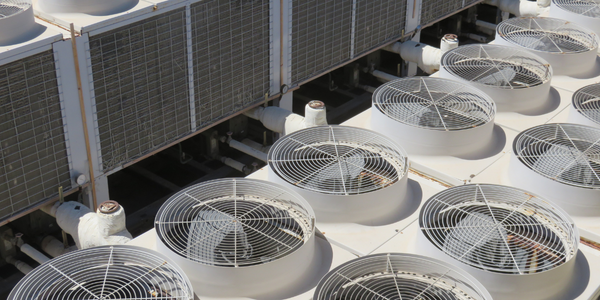
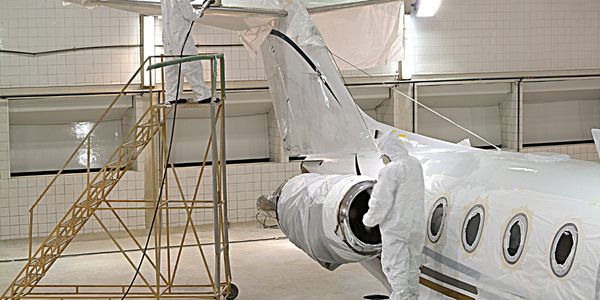
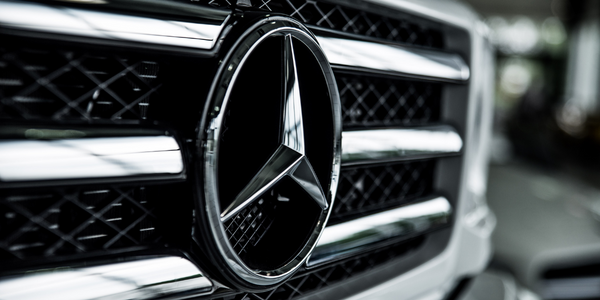
