Download PDF
HyperWorks: Streamlining Boat Design and Engineering at Sea Ray
Technology Category
- Analytics & Modeling - Digital Twin / Simulation
- Application Infrastructure & Middleware - Middleware, SDKs & Libraries
Applicable Industries
- Automotive
- Marine & Shipping
Applicable Functions
- Product Research & Development
Use Cases
- Structural Health Monitoring
- Time Sensitive Networking
The Challenge
Sea Ray Boats, a leading U.S.-based manufacturer of high-end pleasure boats, is constantly challenged by the need for innovation and change in the luxury boat market. The company introduces eight to 12 new or refreshed designs every year, with the engineering team working on six or seven designs at any given time. The primary challenge in designing boats is creating usable space, which is always in short supply. Much of the design effort focuses on configurable space that can change function to fill more than one need. The design cycle varies with the boat, typically averaging eight to 18 months depending on the size and type of the boat. The engineering team at Sea Ray uses Altair HyperWorks CAE tools exclusively for the entire analysis process of the vessel, from modeling and simulation, to visualization and reporting.
About The Customer
Sea Ray Boats is a leading U.S.-based manufacturer of high-end pleasure boats. The company is part of the Brunswick Boat Group, the world's largest maker of pleasure boats. Sea Ray is known for its handsome, high-performance boats and introduces eight to 12 new or refreshed designs every year. The company's engineering team is based at Merritt Island, near Cocoa Beach and Cape Canaveral on Florida's Space Coast. The team painstakingly creates and analyzes engineering designs for the boats using Altair HyperWorks CAE tools exclusively.
The Solution
Sea Ray has expanded the use of HyperWorks to seven engineers, creating full-system CAE models of entire vessels and looking at designs under a variety of load conditions. The engineering team primarily uses HyperMesh and HyperView to create and assess its full-system structural models. They also use HyperGraph in the Structural Group and the Naval Engineering Group to plot speed, performance and G-loading from instrumented on-water testing. The Mechanical Engineering section recently began using MotionView to simulate the function of a number of mechanisms. Sea Ray relies solely on OptiStruct for structural analysis. The standard Sea Ray model analysis includes inertia relief and vibration simulations on an untrimmed vessel. Later on, point masses that represent the engine, batteries, generators and other non-structural components are added to the simulation model.
Operational Impact
Related Case Studies.
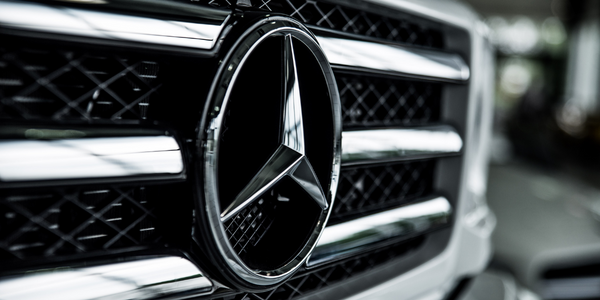
Case Study
Integral Plant Maintenance
Mercedes-Benz and his partner GAZ chose Siemens to be its maintenance partner at a new engine plant in Yaroslavl, Russia. The new plant offers a capacity to manufacture diesel engines for the Russian market, for locally produced Sprinter Classic. In addition to engines for the local market, the Yaroslavl plant will also produce spare parts. Mercedes-Benz Russia and his partner needed a service partner in order to ensure the operation of these lines in a maintenance partnership arrangement. The challenges included coordinating the entire maintenance management operation, in particular inspections, corrective and predictive maintenance activities, and the optimizing spare parts management. Siemens developed a customized maintenance solution that includes all electronic and mechanical maintenance activities (Integral Plant Maintenance).
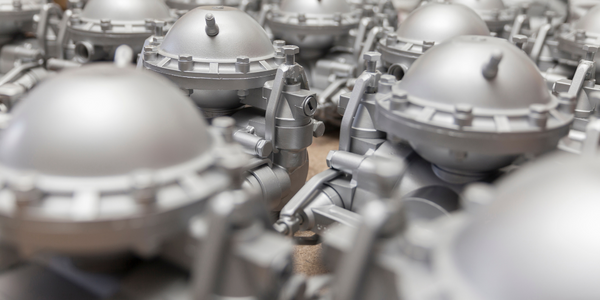
Case Study
Monitoring of Pressure Pumps in Automotive Industry
A large German/American producer of auto parts uses high-pressure pumps to deburr machined parts as a part of its production and quality check process. They decided to monitor these pumps to make sure they work properly and that they can see any indications leading to a potential failure before it affects their process.