Download PDF
Imerys S.A. Saves USD 180K/year and Reduces Time Spent On Tracking By 52 Days
Technology Category
- Functional Applications - Remote Monitoring & Control Systems
- Analytics & Modeling - Real Time Analytics
Applicable Industries
- Mining
Applicable Functions
- Logistics & Transportation
- Business Operation
Use Cases
- Track & Trace of Assets
- Fleet Management
- Supply Chain Visibility
Services
- System Integration
- Software Design & Engineering Services
The Challenge
Imerys S.A. faced significant challenges with their manual, spreadsheet-based container tracking system. This method caused frequent errors in shipment management, leading to operational downtime. Each country required a dedicated resource to validate and update tracking data daily, which was time-consuming and inefficient. The lack of real-time shipment visibility resulted in high detention and demurrage fees, further impacting their operations. Additionally, data silos hindered customer service and made it difficult to benchmark shipping lines' KPIs effectively.
About The Customer
Imerys S.A. is a global leader in the production and processing of industrial minerals. The company leverages 10,000 containers annually in the APAC region alone and manages 300,000 tons of cargo in the same area. With operations in 142 countries and a customer base exceeding 15,000, Imerys S.A. is a significant player in the industrial minerals market. Their extensive logistics operations necessitate efficient and accurate container tracking to maintain high standards of customer service and operational efficiency.
The Solution
To address these challenges, Imerys S.A. implemented Shipsy's real-time container tracking solution. This solution provides a single, unified dashboard that offers greater visibility and control over container freight movement across multimodal logistics operations. By eliminating the need for manual tracking, the solution significantly reduces the time and resources required for container management. The real-time tracking capabilities ensure that all container statuses are updated automatically every few hours, providing critical insights for cross-border logistics planning. Additionally, the solution simplifies reporting and enhances customer satisfaction by offering proactive container status monitoring and instant notifications for delays and customs clearance issues.
Operational Impact
Quantitative Benefit
Related Case Studies.
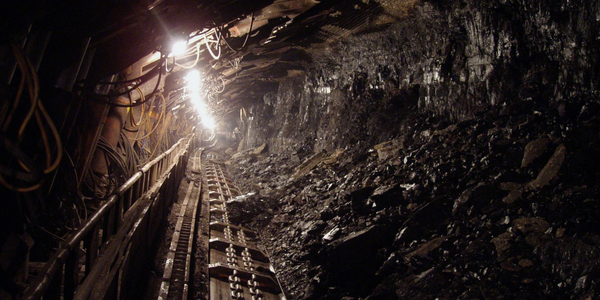
Case Study
Underground Mining Safety
The goal was to produce a safety system to monitor and support underground mining operations; existing systems were either too simple (i.e. phone line) or overly complex and expensive, inhibiting deployment, and providing little-to-no support in event of an accident. Given the dangerous nature of the mining work environment and the strict regulations placed on the industry, the solution would have to comply with Mine Safety and Health Administration (MSHA) regulations. Yet the product needed to allow for simple deployment to truly be a groundbreaking solution - increasing miner safety and changing daily operations for the better.
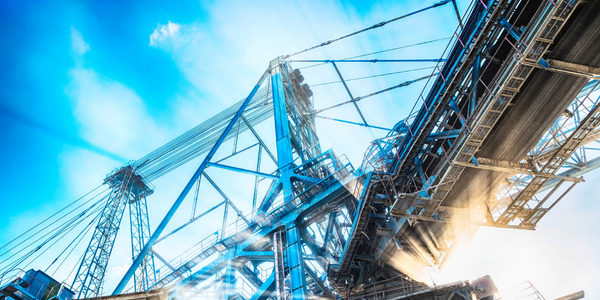
Case Study
Mining Firm Quadruples Production, with Internet of Everything
Dundee Precious Metal’s flagship mine, in Chelopech, Bulgaria, produces a gold, copper, and silver concentrate set a goal to increase production by 30%. Dundee wanted to increase production quality and output without increasing headcount and resources, improve miner safety, and minimize cost.
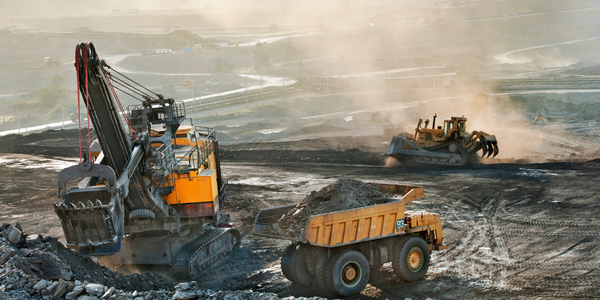
Case Study
Fastenal Builds the Future of Manufacturing with MachineMetrics
Fastenal's objective was to better understand their machine downtime, utilization, quality issues, and to embrace cutting-edge manufacturing technology/process improvement capabilities to bring their team to the next level. However, there was a lack of real-time data, visualization, and actionable insights made this transition impossible.
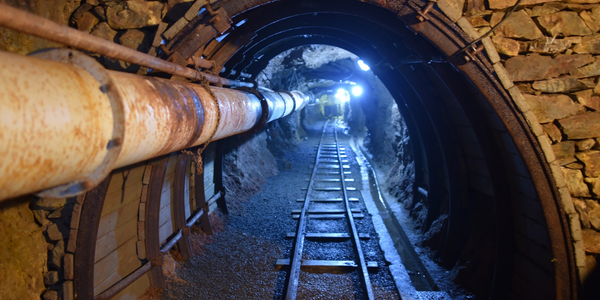
Case Study
Joy Mining Systems
Joy equipment faces many challenges. The first is machine integration and control. The business end of the machine has a rapidly-spinning cylinder with 6-inch diamond-studded cutting teeth. It chews through rock at rates measured in tens of tons per minute. The system grinds through the rock in front, creating a rectangular mine tunnel. Hydraulic lifters support the ceiling as the machine moves forward. Automated drills and screws drive 3-ft long screws into the ceiling to stabilize it. The rock and coal fall into a set of gathering "fingers" below the cutting cylinder. These fingers scoop up the rock and coal and deposit it onto a conveyor belt. The conveyor passes under the machine and out the back. A train of conveyor belt cars, up to a mile long, follows the cutter into the mine. The rock shoots along this train at over 400 feet per minute until it empties into rail cars at the end. Current systems place an operator cage next to the cutter. Choking dust (potentially explosive), the risk of collapse and the proximity of metal and rock mayhem make the operator cage a hazardous location.
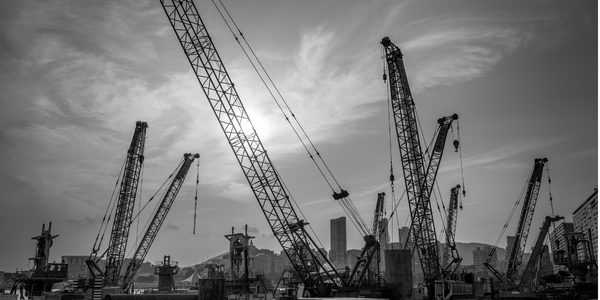
Case Study
Improved Monitoring in Industrial Manufacturing Facility
When your crane is moving tons of magma-hot iron, you can’t afford an unexpected failure. McWane Ductile knew monitoring the crane motor metrics within their facility could help prevent a mechanical failure that would strand an enormous bucket of molten metal overhead. Unfortunately, their legacy wired monitoring system couldn’t work with moving objects in this extreme environment. If they could integrate wireless capabilities into their existing equipment they could extend their monitoring capabilities without starting over from scratch.