Download PDF
Improving Customer Experience and Order Efficiency: A Case Study on enviolo
Technology Category
- Application Infrastructure & Middleware - Data Exchange & Integration
- Application Infrastructure & Middleware - Middleware, SDKs & Libraries
Applicable Industries
- Automotive
Applicable Functions
- Procurement
- Warehouse & Inventory Management
Use Cases
- Last Mile Delivery
- Personnel Tracking & Monitoring
Services
- System Integration
The Challenge
enviolo, a supplier of innovative bicycle parts, was facing a significant challenge in managing their order processing and customer experience. They had a dedicated team monitoring their Shopify store, but the team was manually processing all orders, regardless of size. This process involved copying and pasting each order from the Shopify storefront into NetSuite for fulfillment. Additionally, new customer profiles had to be created twice, once in Shopify and once in NetSuite, which was also done manually. This resulted in a delay in visibility on the availability of parts, leading to slow, inefficient, and error-prone fulfillment of orders. The manual process was not only tedious but also affected employee morale and productivity. The company was looking for a solution that would seamlessly integrate their systems and improve their backend process.
About The Customer
enviolo is a company based in Amsterdam, Noord-Holland that supplies bicycle manufacturers with stepless and automatic shifting bicycle parts incorporating the revolutionary NuVinci technology. The company's technology allows cyclists to focus less on changing gears and more on their surroundings. enviolo is a division of Fallbrook Technologies Inc and operated under the name “NuVinci Cycling” up until December 2017. The company is committed to providing an excellent, easy experience for bike shops and mechanics to order parts directly. They use Shopify to host a B2B storefront and NetSuite as their ERP to serve as a centralized source of information about customers and orders.
The Solution
The solution to enviolo's challenge was integrating their Shopify and NetSuite platforms. However, they needed a solution that didn't require a developer to maintain and wouldn't involve months of building an ad-hoc integration. The consultant developing the Shopify storefront recommended Celigo, an industry-leading integration platform. With Celigo's Shopify-NetSuite Integration App, enviolo was able to quickly sync their orders between NetSuite and Shopify. This automated the order-to-cash process and provided the team with real-time visibility into their inventory levels, order status, and payment status. The company is also planning to integrate with Zendesk to further enhance customer support. By integrating it with their ERP, they will be able to see customers’ info, order history, and questions all in one place.
Operational Impact
Quantitative Benefit
Related Case Studies.
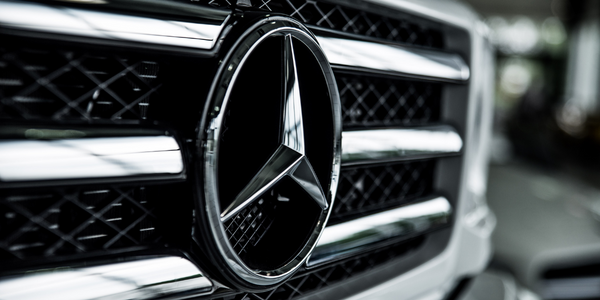
Case Study
Integral Plant Maintenance
Mercedes-Benz and his partner GAZ chose Siemens to be its maintenance partner at a new engine plant in Yaroslavl, Russia. The new plant offers a capacity to manufacture diesel engines for the Russian market, for locally produced Sprinter Classic. In addition to engines for the local market, the Yaroslavl plant will also produce spare parts. Mercedes-Benz Russia and his partner needed a service partner in order to ensure the operation of these lines in a maintenance partnership arrangement. The challenges included coordinating the entire maintenance management operation, in particular inspections, corrective and predictive maintenance activities, and the optimizing spare parts management. Siemens developed a customized maintenance solution that includes all electronic and mechanical maintenance activities (Integral Plant Maintenance).
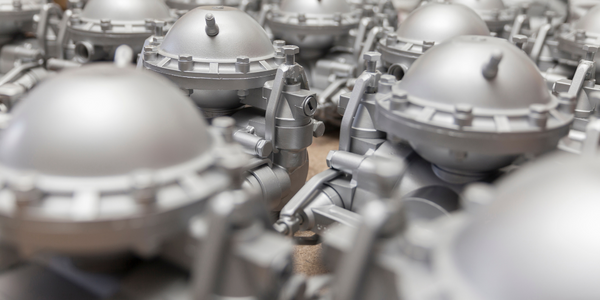
Case Study
Monitoring of Pressure Pumps in Automotive Industry
A large German/American producer of auto parts uses high-pressure pumps to deburr machined parts as a part of its production and quality check process. They decided to monitor these pumps to make sure they work properly and that they can see any indications leading to a potential failure before it affects their process.