Download PDF
Industrias Haber’s Stays on Point in the Cutting Room with Lectra Technology
Technology Category
- Functional Applications - Manufacturing Execution Systems (MES)
- Functional Applications - Product Lifecycle Management Systems (PLM)
Applicable Industries
- Apparel
- Retail
Applicable Functions
- Discrete Manufacturing
- Quality Assurance
Use Cases
- Manufacturing System Automation
- Predictive Maintenance
- Process Control & Optimization
Services
- System Integration
- Training
The Challenge
Industrias Haber’s, a leading Mexican manufacturer of suits and uniforms, faced the challenge of managing the production of 130,000 garments per month efficiently. The company needed to reduce its time to market and keep its offerings cost-competitive without sacrificing quality. With increasing competition and the need to deliver orders on shorter turnaround times, Haber’s was under pressure to make its operations more cost-efficient while maintaining high standards of fit and quality.
About The Customer
Industrias Haber’s is a 100% Mexican company that designs, manufactures, and retails suits and uniforms for men and women. The company operates its own brands, including High Life, Robert’s, and Men’s Fashion, and collaborates with renowned brands such as Hugo Boss, Ermenegildo Zegna, Canali, Valentino, and Armani. With a strong presence in Mexico, the company exports to Canada, the US, and Mexico. Starting as a small family operation producing 20 suits a day, Industrias Haber’s has grown to become one of the largest suit and uniform manufacturers in Mexico, with 120 retail stores across the country.
The Solution
Industrias Haber’s partnered with Lectra to automate its patternmaking process and later decided to revamp its cutting room. The company implemented Lectra’s marker making and cut-order planning technology, combined with high-speed Vector cutting machines. This automation allowed Haber’s to reduce fabric waste by 3-4%, improve product quality by 20-25%, boost production efficiency by 10%, and cut the manufacturing process from 15 to 10 days. The new system enabled the company to compete on speed while maintaining superior quality and service. Additionally, the use of Optiplan technology allowed for simulations of different production scenarios, making the manufacturing process more flexible and agile.
Operational Impact
Quantitative Benefit
Related Case Studies.
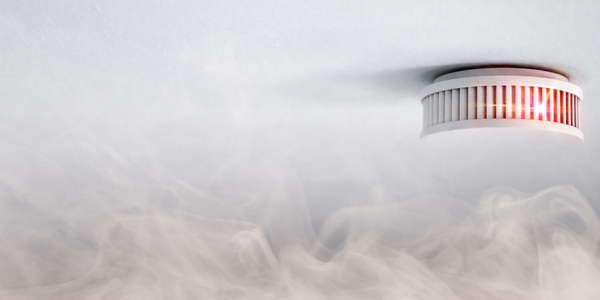
Case Study
Fire Alarm System and Remote Monitoring Sytem
Fire alarm systems are essential in providing an early warning in the event of fire. They help to save lives and protect property whilst also fulfilling the needs of insurance companies and government departments.Fire alarm systems typically consist of several inter-linked components, such as smoke detectors, heat detector, carbon monoxide, manual call points, sounders, alarm and buzzer. The fire alarm system should give immediate information in order to prevent the fire spread and protect live and property.To get maximum protection a shoe manufacturer in Indonesia opted for a new fire alarm system to monitor 13 production sites spread over 160 hectars. Although the company had an existing fire alarm system, it could not be monitored remotely.It was essential that the new system would be able to be monitored from a central control room. It needed to be able to connect to the existing smoke detector and manual call point. Information should be easily collected and passed on to the Supervisory Control and Data Acquisition (SCADA) system. Furthermore, the system should have several features such as alarm management, auto reporting, being connected to many client computers without additional cost, and run 24/7 without fails. The company also needed a system which could be implemented without changing the architecture of the existing fire alarm system.
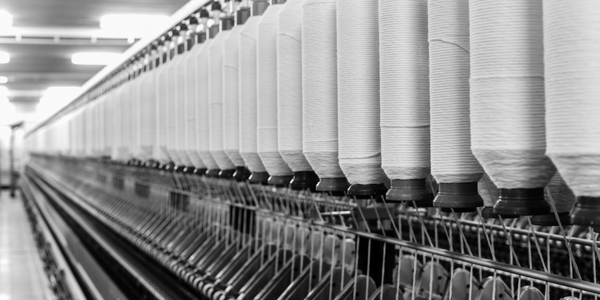
Case Study
IoT Applications and Upgrades in Textile Plant
At any given time, the textile company’s manufacturing facility has up to 2,000 textile carts in use. These carts are pushed from room to room, carrying materials or semi-finished products. Previously, a paper with a hand-written description was attached to each cart. This traditional method of processing made product tracking extremely difficult. Additionally, making sure that every cart of materials or semi-finished products went to its correct processing work station was also a problem. Therefore, the company desired an intelligent solution for tracking assets at their factories. They also wanted a solution that would help them collect process data so they could improve their manufacturing efficiency.
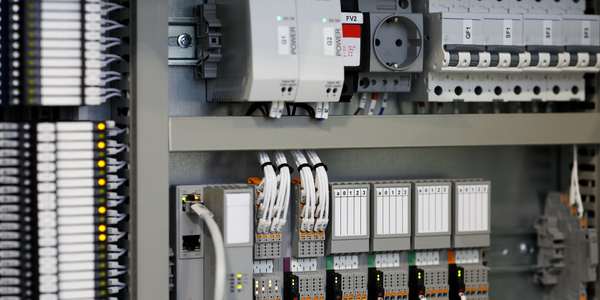
Case Study
Improving Production Line Efficiency with Ethernet Micro RTU Controller
Moxa was asked to provide a connectivity solution for one of the world's leading cosmetics companies. This multinational corporation, with retail presence in 130 countries, 23 global braches, and over 66,000 employees, sought to improve the efficiency of their production process by migrating from manual monitoring to an automatic productivity monitoring system. The production line was being monitored by ABB Real-TPI, a factory information system that offers data collection and analysis to improve plant efficiency. Due to software limitations, the customer needed an OPC server and a corresponding I/O solution to collect data from additional sensor devices for the Real-TPI system. The goal is to enable the factory information system to more thoroughly collect data from every corner of the production line. This will improve its ability to measure Overall Equipment Effectiveness (OEE) and translate into increased production efficiencies. System Requirements • Instant status updates while still consuming minimal bandwidth to relieve strain on limited factory networks • Interoperable with ABB Real-TPI • Small form factor appropriate for deployment where space is scarce • Remote software management and configuration to simplify operations
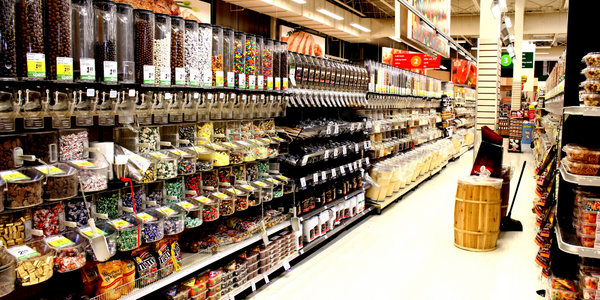
Case Study
How Sirqul’s IoT Platform is Crafting Carrefour’s New In-Store Experiences
Carrefour Taiwan’s goal is to be completely digital by end of 2018. Out-dated manual methods for analysis and assumptions limited Carrefour’s ability to change the customer experience and were void of real-time decision-making capabilities. Rather than relying solely on sales data, assumptions, and disparate systems, Carrefour Taiwan’s CEO led an initiative to find a connected IoT solution that could give the team the ability to make real-time changes and more informed decisions. Prior to implementing, Carrefour struggled to address their conversion rates and did not have the proper insights into the customer decision-making process nor how to make an immediate impact without losing customer confidence.
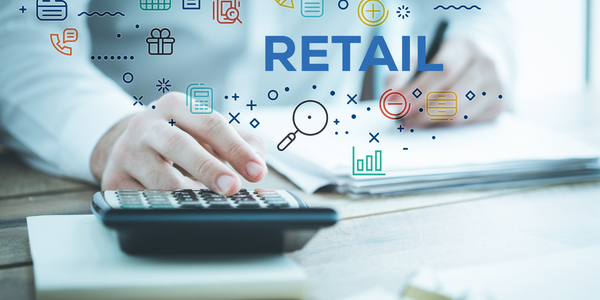
Case Study
Digital Retail Security Solutions
Sennco wanted to help its retail customers increase sales and profits by developing an innovative alarm system as opposed to conventional connected alarms that are permanently tethered to display products. These traditional security systems were cumbersome and intrusive to the customer shopping experience. Additionally, they provided no useful data or analytics.