Download PDF
Inspire: A Revolutionary Design Solution for the Oil & Gas Industry
Technology Category
- Sensors - Gas Sensors
- Sensors - Utility Meters
Applicable Industries
- Oil & Gas
Applicable Functions
- Product Research & Development
Use Cases
- Time Sensitive Networking
The Challenge
The Oil and Gas sector is a complex industry that requires intricate and efficient design processes. Traditional CAD design methods often result in heavy, costly, and time-consuming conceptual designs. The industry is constantly seeking ways to reduce material costs, save weight, and expedite the conceptual design process. Furthermore, there is a need to understand different manufacturing techniques better and gain a more comprehensive understanding of the part/assembly. The challenge lies in finding a solution that can address these issues while being easy to use and compatible with existing CAD systems.
About The Customer
The customer in this case study is the Oil and Gas sector. This industry is characterized by its complexity and the need for efficient and effective design processes. The sector is constantly seeking ways to reduce costs, improve efficiency, and expedite processes. The industry also requires a deep understanding of different manufacturing techniques and a comprehensive understanding of the part/assembly. The Oil and Gas sector is likely to benefit significantly from a solution like Inspire, which promises to address these needs and challenges.
The Solution
Inspire, a CAE-driven design tool, offers a revolutionary solution to these challenges. The process begins with the original CAD design, from which package space and load cases are created. The Inspire Concept Shape is then developed, allowing for the exploration of different designs and shapes. The concept shape is validated, and the results are integrated back into the CAD system. The new design, as a result, is 25% lighter than the original. Inspire 2014 offers several benefits, including lower material cost, weight savings, less time spent on conceptual design, the ability to generate more concepts in a shorter time, a better understanding of different manufacturing techniques, and a more comprehensive understanding of the part/assembly. It is also easy to use and features a new analysis feature and export for CAD.
Operational Impact
Quantitative Benefit
Related Case Studies.
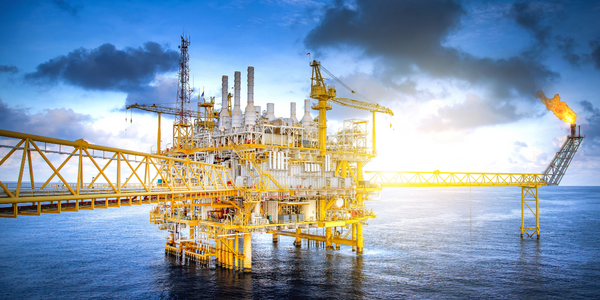
Case Study
Taking Oil and Gas Exploration to the Next Level
DownUnder GeoSolutions (DUG) wanted to increase computing performance by 5 to 10 times to improve seismic processing. The solution must build on current architecture software investments without sacrificing existing software and scale computing without scaling IT infrastructure costs.
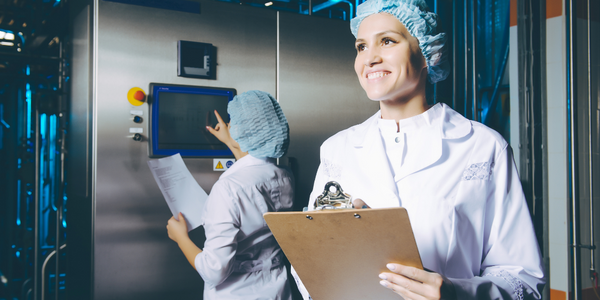
Case Study
Remote Wellhead Monitoring
Each wellhead was equipped with various sensors and meters that needed to be monitored and controlled from a central HMI, often miles away from the assets in the field. Redundant solar and wind generators were installed at each wellhead to support the electrical needs of the pumpstations, temperature meters, cameras, and cellular modules. In addition to asset management and remote control capabilities, data logging for remote surveillance and alarm notifications was a key demand from the customer. Terra Ferma’s solution needed to be power efficient, reliable, and capable of supporting high-bandwidth data-feeds. They needed a multi-link cellular connection to a central server that sustained reliable and redundant monitoring and control of flow meters, temperature sensors, power supply, and event-logging; including video and image files. This open-standard network needed to interface with the existing SCADA and proprietary network management software.
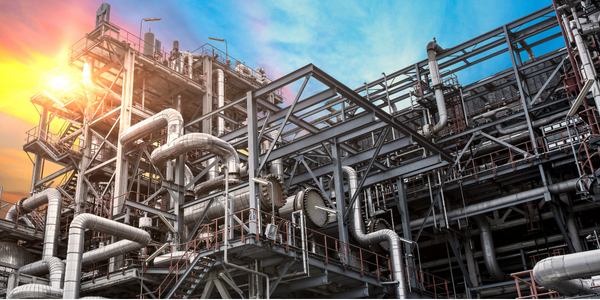
Case Study
Refinery Saves Over $700,000 with Smart Wireless
One of the largest petroleum refineries in the world is equipped to refine various types of crude oil and manufacture various grades of fuel from motor gasoline to Aviation Turbine Fuel. Due to wear and tear, eight hydrogen valves in each refinery were leaking, and each cost $1800 per ton of hydrogen vented. The plant also had leakage on nearly 30 flare control hydrocarbon valves. The refinery wanted a continuous, online monitoring system that could catch leaks early, minimize hydrogen and hydrocarbon production losses, and improve safety for maintenance.