Download PDF
KTY Engenharia Improves Production Processes with AVEVA's Visual Engineering
Technology Category
- Application Infrastructure & Middleware - Data Exchange & Integration
Applicable Industries
- Oil & Gas
Applicable Functions
- Discrete Manufacturing
- Product Research & Development
Use Cases
- Manufacturing System Automation
- Predictive Maintenance
Services
- System Integration
- Software Design & Engineering Services
The Challenge
KTY Engenharia, a company serving the oil & gas, energy, and infrastructure industries, was facing challenges in managing the vast amount of data involved in their engineering projects. The company was dealing with multiple projects concurrently, requiring regular contact with external partners and interoperability of tools used by all parties. The company was committed to continuously evolving and improving its working practices, and mastering the use of AVEVA tools was considered core to this strategy. One of the main concerns was the reliability and trustworthiness of information shared between documents. Large projects involved a complex interchange of documents and multidisciplinary information, where the slightest error could cause significant delays.
About The Customer
KTY Engenharia is a Brazil-based company that has been serving the oil & gas, energy, and infrastructure industries both domestically and abroad for over 30 years. The company is committed to continuously evolving and bringing its customers the best in engineering practices. KTY Engenharia is constantly evaluating new technologies to improve its working practices and considers mastering the use of AVEVA tools core to this strategy. The company believes this demonstrates to its customers that KTY is always evolving. KTY Engenharia has a commitment to best practice, which it considers a key part of its competitive advantage.
The Solution
AVEVA consultants introduced KTY Engenharia to the advanced dimension of design direction that could be achieved by integrating AVEVA Electrical with AVEVA Instrumentation to harness the process improvements achievable with visual engineering. The two solutions share the same SQL database, enabling the firm to share and control equipment and connections, besides making cable management via 3D models. Applying the cable routing solution via a 3D model enabled the KTY electrical team to route more than 4,000 cable runs (more than 200 km of cables) and obtain more accurate data from voltage drop calculations, and precise materials lists, generating savings for its customers.
Operational Impact
Quantitative Benefit
Related Case Studies.
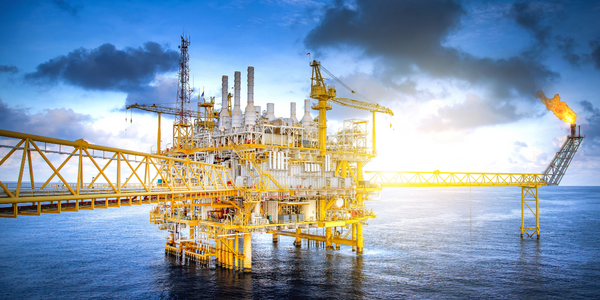
Case Study
Taking Oil and Gas Exploration to the Next Level
DownUnder GeoSolutions (DUG) wanted to increase computing performance by 5 to 10 times to improve seismic processing. The solution must build on current architecture software investments without sacrificing existing software and scale computing without scaling IT infrastructure costs.
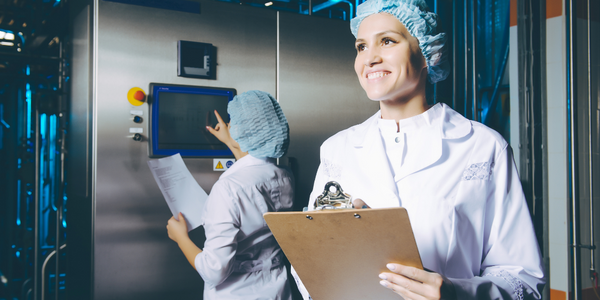
Case Study
Remote Wellhead Monitoring
Each wellhead was equipped with various sensors and meters that needed to be monitored and controlled from a central HMI, often miles away from the assets in the field. Redundant solar and wind generators were installed at each wellhead to support the electrical needs of the pumpstations, temperature meters, cameras, and cellular modules. In addition to asset management and remote control capabilities, data logging for remote surveillance and alarm notifications was a key demand from the customer. Terra Ferma’s solution needed to be power efficient, reliable, and capable of supporting high-bandwidth data-feeds. They needed a multi-link cellular connection to a central server that sustained reliable and redundant monitoring and control of flow meters, temperature sensors, power supply, and event-logging; including video and image files. This open-standard network needed to interface with the existing SCADA and proprietary network management software.
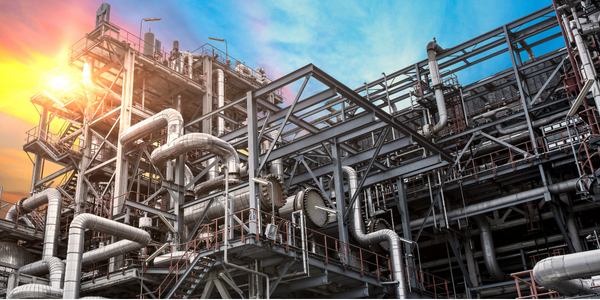
Case Study
Refinery Saves Over $700,000 with Smart Wireless
One of the largest petroleum refineries in the world is equipped to refine various types of crude oil and manufacture various grades of fuel from motor gasoline to Aviation Turbine Fuel. Due to wear and tear, eight hydrogen valves in each refinery were leaking, and each cost $1800 per ton of hydrogen vented. The plant also had leakage on nearly 30 flare control hydrocarbon valves. The refinery wanted a continuous, online monitoring system that could catch leaks early, minimize hydrogen and hydrocarbon production losses, and improve safety for maintenance.