Download PDF
Leveraging AWS for Enhanced Data Processing: A GumGum Case Study
Applicable Industries
- Oil & Gas
Applicable Functions
- Sales & Marketing
Use Cases
- Inventory Management
The Challenge
GumGum, a leading provider of programmatic, native, and social analytics software solutions, was facing a significant challenge in managing its data. The company generates more than 1 billion events, equivalent to approximately 6 TB of data, every single day. This massive amount of data needed to be processed continuously to eliminate bottlenecks and expedite decision-making for customers. The company was in dire need of a solution that could scale quickly to handle the rapidly growing traffic and data. The challenge was not just about managing the volume of data but also about processing it in real-time to provide valuable insights to customers.
About The Customer
GumGum is a renowned company known for creating the in-image advertising category. The company offers products based on its patented image recognition technology, delivering programmatic, native, and social analytics software solutions. GumGum reaches 400 million visitors as they view images and content across more than 2,000 premium publishers. The company's customers' ads benefit from 20 percent higher viewability and 10 times the engagement of traditional display options. This results in superior brand lift for marketers and increased revenue for publishers. GumGum works with more than half of AdAge’s top 100 U.S. advertising spenders, including Disney, L’Oreal, Toyota, and Samsung. The company is headquartered in Santa Monica, California, with six additional offices in the United States and the United Kingdom.
The Solution
GumGum turned to Amazon Web Services (AWS) to address its data management challenges. The company now runs ad servers that generate event data, which is written to logs and uploaded to Amazon Simple Storage Solution (Amazon S3) on an hourly basis. The output is then stored in Amazon Redshift. To manage the workflow for production, testing, and development, GumGum uses Amazon Data Pipeline services. For inventory forecasting and hourly data processing, the company uses Amazon Elastic MapReduce (Amazon EMR) to run Apache Spark and Hadoop respectively. Additionally, GumGum provides its users with a proprietary dashboard that displays data from the reporting server, ensuring that customers have access to real-time insights.
Operational Impact
Quantitative Benefit
Related Case Studies.
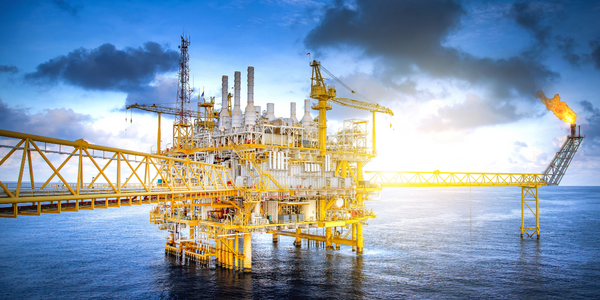
Case Study
Taking Oil and Gas Exploration to the Next Level
DownUnder GeoSolutions (DUG) wanted to increase computing performance by 5 to 10 times to improve seismic processing. The solution must build on current architecture software investments without sacrificing existing software and scale computing without scaling IT infrastructure costs.
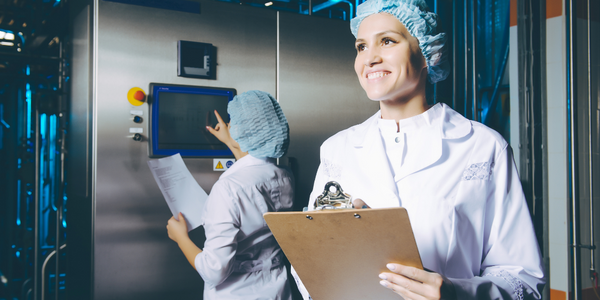
Case Study
Remote Wellhead Monitoring
Each wellhead was equipped with various sensors and meters that needed to be monitored and controlled from a central HMI, often miles away from the assets in the field. Redundant solar and wind generators were installed at each wellhead to support the electrical needs of the pumpstations, temperature meters, cameras, and cellular modules. In addition to asset management and remote control capabilities, data logging for remote surveillance and alarm notifications was a key demand from the customer. Terra Ferma’s solution needed to be power efficient, reliable, and capable of supporting high-bandwidth data-feeds. They needed a multi-link cellular connection to a central server that sustained reliable and redundant monitoring and control of flow meters, temperature sensors, power supply, and event-logging; including video and image files. This open-standard network needed to interface with the existing SCADA and proprietary network management software.
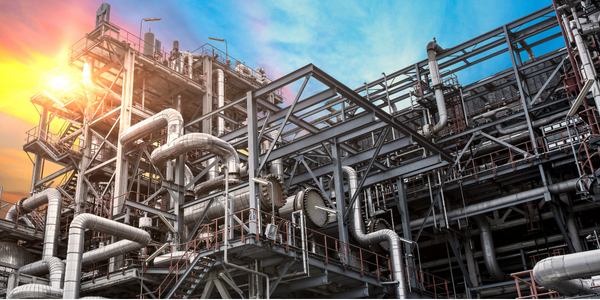
Case Study
Refinery Saves Over $700,000 with Smart Wireless
One of the largest petroleum refineries in the world is equipped to refine various types of crude oil and manufacture various grades of fuel from motor gasoline to Aviation Turbine Fuel. Due to wear and tear, eight hydrogen valves in each refinery were leaking, and each cost $1800 per ton of hydrogen vented. The plant also had leakage on nearly 30 flare control hydrocarbon valves. The refinery wanted a continuous, online monitoring system that could catch leaks early, minimize hydrogen and hydrocarbon production losses, and improve safety for maintenance.