Download PDF
Leveraging BIM for Efficient Interior Design: A Case Study of Itoya Renovation
Technology Category
- Analytics & Modeling - Virtual & Augmented Reality Software
- Wearables - Virtual Reality Glasses, Headsets & Controllers
Applicable Industries
- Buildings
- Retail
Applicable Functions
- Product Research & Development
Use Cases
- Virtual Prototyping & Product Testing
- Virtual Reality
The Challenge
Ikeda architectural design, led by architect Yoichiro Ikeda, was tasked with the renovation of 'Itoya', one of the largest stationary stores in Japan. The challenge was to simultaneously renovate multiple stores, including two main stores in Ginza, Tokyo, and another in Yokohama. The renovation involved swapping different floors between the two Tokyo stores while refurbishing all the floors at the same time. The renovation mainly consisted of designing new shelving and display islands, with the floor, wall, ceiling, and lighting remaining as they were. The schedule for the renovation was extremely tight, adding to the complexity of the project. The firm was uncertain if they could meet the deadline, and there was a need for a solution that would ensure timely completion and client satisfaction.
About The Customer
The customer in this case study is 'Itoya', one of the largest stationary stores in Japan, established in 1904. Itoya has two main stores in Ginza, the central part of Tokyo, and a total of nine stores across the country. The firm specializes in stationery and is popular and famous in Japan. Each floor in the stores is dedicated to different types of products, such as expensive stationaries for writing or notebooks. The customer requested the renovation of the two main stores and another one in Yokohama, which amounted to five floors’ interiors.
The Solution
The firm implemented a full-scale Building Information Modeling (BIM) operation using Archicad to manage the renovation project. The BIM design allowed the firm to create more detailed visuals than just 2D drawings, including texture and materials, helping the clients understand the proposed design content in the early stage. The firm was able to design the space and the furniture after the first meeting with the client, and by the second meeting, they provided renderings and walk-throughs with BIMx. The firm responded swiftly to changes using Archicad, and the client confirmed those changes by viewing the 3D models. The communication between the architect and the client was seamless and fast, and the wishes of the client were incorporated accurately. The 3D models of the fixtures and the furniture created for this project were stored as a 3D object database, allowing for quick responses to any additional renovation requests by the client.
Operational Impact
Quantitative Benefit
Related Case Studies.
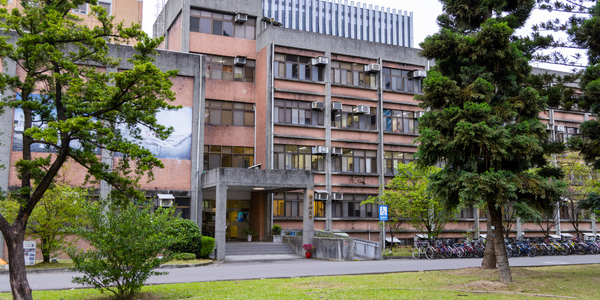
Case Study
Energy Saving & Power Monitoring System
Recently a university in Taiwan was experiencing dramatic power usage increases due to its growing number of campus buildings and students. Aiming to analyze their power consumption and increase their power efficiency across 52 buildings, the university wanted to build a power management system utilizing web-based hardware and software. With these goals in mind, they contacted Advantech to help them develop their system and provide them with the means to save energy in the years to come.
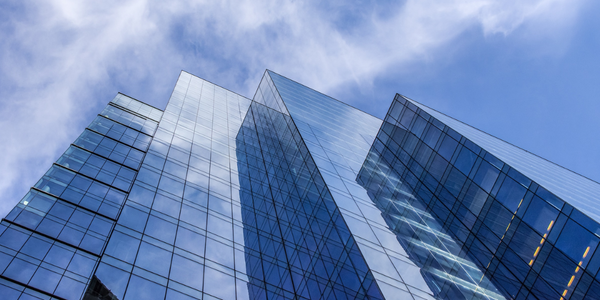
Case Study
Intelligent Building Automation System and Energy Saving Solution
One of the most difficult problems facing the world is conserving energy in buildings. However, it is not easy to have a cost-effective solution to reduce energy usage in a building. One solution for saving energy is to implement an intelligent building automation system (BAS) which can be controlled according to its schedule. In Indonesia a large university with a five floor building and 22 classrooms wanted to save the amount of energy being used.
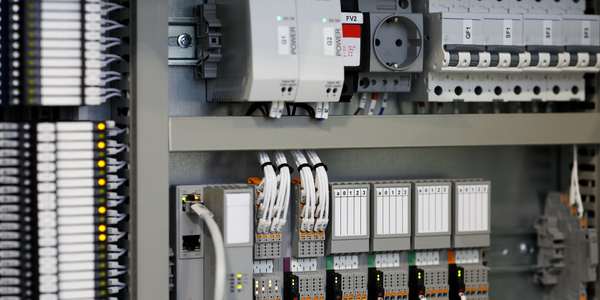
Case Study
Improving Production Line Efficiency with Ethernet Micro RTU Controller
Moxa was asked to provide a connectivity solution for one of the world's leading cosmetics companies. This multinational corporation, with retail presence in 130 countries, 23 global braches, and over 66,000 employees, sought to improve the efficiency of their production process by migrating from manual monitoring to an automatic productivity monitoring system. The production line was being monitored by ABB Real-TPI, a factory information system that offers data collection and analysis to improve plant efficiency. Due to software limitations, the customer needed an OPC server and a corresponding I/O solution to collect data from additional sensor devices for the Real-TPI system. The goal is to enable the factory information system to more thoroughly collect data from every corner of the production line. This will improve its ability to measure Overall Equipment Effectiveness (OEE) and translate into increased production efficiencies. System Requirements • Instant status updates while still consuming minimal bandwidth to relieve strain on limited factory networks • Interoperable with ABB Real-TPI • Small form factor appropriate for deployment where space is scarce • Remote software management and configuration to simplify operations
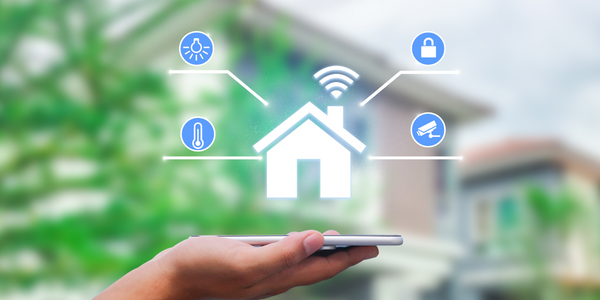
Case Study
Powering Smart Home Automation solutions with IoT for Energy conservation
Many industry leaders that offer Smart Energy Management products & solutions face challenges including:How to build a scalable platform that can automatically scale-up to on-board ‘n’ number of Smart home devicesData security, solution availability, and reliability are the other critical factors to deal withHow to create a robust common IoT platform that handles any kind of smart devicesHow to enable data management capabilities that would help in intelligent decision-making