Download PDF
Lumo Energy's Transformation through Nintex Promapp
Applicable Industries
- Equipment & Machinery
- Renewable Energy
Applicable Functions
- Quality Assurance
Use Cases
- Personnel Tracking & Monitoring
- Visual Quality Detection
Services
- Testing & Certification
The Challenge
Lumo Energy, a subsidiary of Snowy Hydro Limited, faced a significant challenge in documenting its business processes. The company's efforts were hampered by a fast-paced environment, high staff turnover, and ownership issues. The result was a wastage of substantial resources, both time and money, with only 50 completed processes documented in physical folders. The executive leadership lacked confidence in the process documentation and sought a new model for capturing and improving their processes. The company needed a solution that would not only help them document their processes but also promote collaboration and standardization across the organization.
About The Customer
Lumo Energy is a subsidiary of Snowy Hydro Limited, one of Australia’s largest and oldest renewable energy generators. The company operates in Victoria, New South Wales, South Australia, and Queensland. Lumo Energy was facing challenges in documenting its business processes due to a fast-paced environment and high staff turnover. The company needed a solution that would help them document their processes, promote collaboration, and standardize processes across the organization.
The Solution
Lumo Energy turned to Nintex Promapp, a business process management tool, to address their challenges. The company established an Executive Process Improvement Forum to agree on a process governance policy and approach, and to drive Lumo’s Lean Six Sigma improvement program. The tool was chosen for its ability to promote consistent process delivery, staff collaboration, and ownership of aligned processes. Lumo implemented the tool by grouping processes by function rather than by business unit, encouraging staff to think in terms of 'what we do' rather than 'what business unit I’m in'. The second aspect of the implementation was to drive business ownership by getting business owners to prioritize the program and set aside resources to capture processes. The implementation was successful, with the publication of around 500 processes in the first 12 months.
Operational Impact
Quantitative Benefit
Related Case Studies.
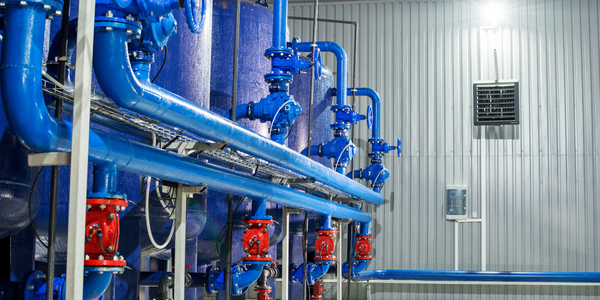
Case Study
Smart Water Filtration Systems
Before working with Ayla Networks, Ozner was already using cloud connectivity to identify and solve water-filtration system malfunctions as well as to monitor filter cartridges for replacements.But, in June 2015, Ozner executives talked with Ayla about how the company might further improve its water systems with IoT technology. They liked what they heard from Ayla, but the executives needed to be sure that Ayla’s Agile IoT Platform provided the security and reliability Ozner required.
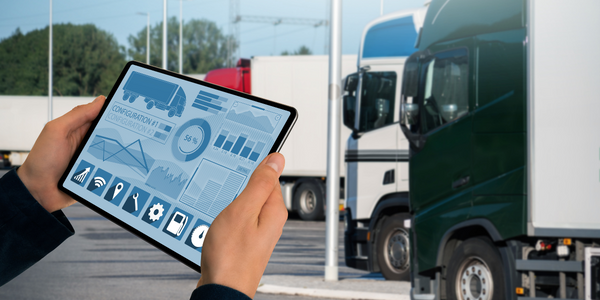
Case Study
IoT enabled Fleet Management with MindSphere
In view of growing competition, Gämmerler had a strong need to remain competitive via process optimization, reliability and gentle handling of printed products, even at highest press speeds. In addition, a digitalization initiative also included developing a key differentiation via data-driven services offers.
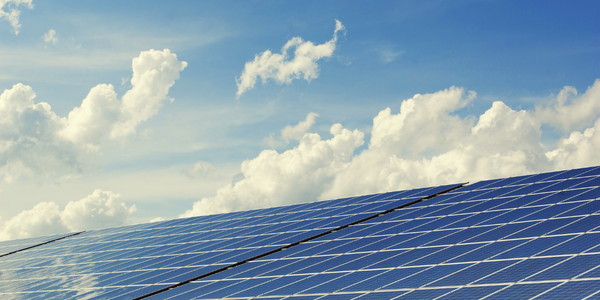
Case Study
Remote Monitoring & Predictive Maintenance App for a Solar Energy System
The maintenance & tracking of various modules was an overhead for the customer due to the huge labor costs involved. Being an advanced solar solutions provider, they wanted to ensure early detection of issues and provide the best-in-class customer experience. Hence they wanted to automate the whole process.
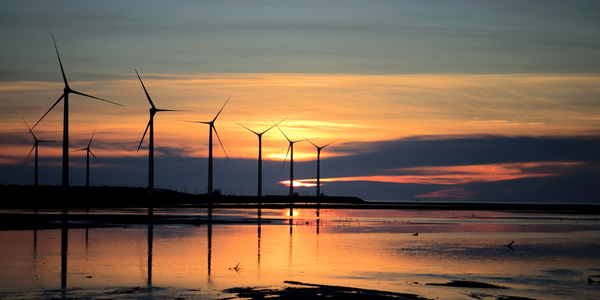
Case Study
Vestas: Turning Climate into Capital with Big Data
Making wind a reliable source of energy depends greatly on the placement of the wind turbines used to produce electricity. Turbulence is a significant factor as it strains turbine components, making them more likely to fail. Vestas wanted to pinpoint the optimal location for wind turbines to maximize power generation and reduce energy costs.
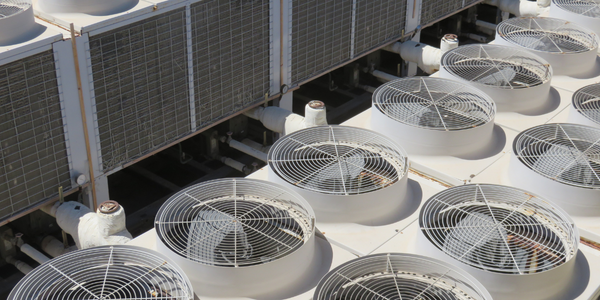
Case Study
Predictive Maintenance for Industrial Chillers
For global leaders in the industrial chiller manufacturing, reliability of the entire production process is of the utmost importance. Chillers are refrigeration systems that produce ice water to provide cooling for a process or industrial application. One of those leaders sought a way to respond to asset performance issues, even before they occur. The intelligence to guarantee maximum reliability of cooling devices is embedded (pre-alarming). A pre-alarming phase means that the cooling device still works, but symptoms may appear, telling manufacturers that a failure is likely to occur in the near future. Chillers who are not internet connected at that moment, provide little insight in this pre-alarming phase.
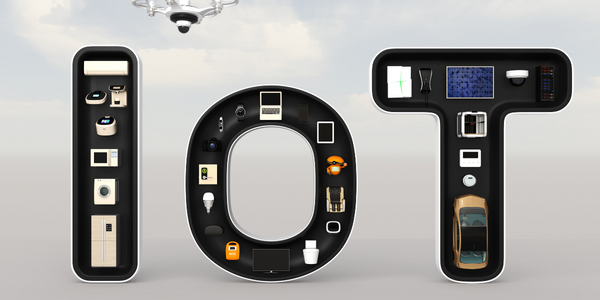
Case Study
Premium Appliance Producer Innovates with Internet of Everything
Sub-Zero faced the largest product launch in the company’s history:It wanted to launch 60 new products as scheduled while simultaneously opening a new “greenfield” production facility, yet still adhering to stringent quality requirements and manage issues from new supply-chain partners. A the same time, it wanted to increase staff productivity time and collaboration while reducing travel and costs.