Download PDF
Maintenance Management Helps Western Refining Optimize Availability of Plant Assets
Technology Category
- Functional Applications - Enterprise Asset Management Systems (EAM)
Applicable Industries
- Oil & Gas
Applicable Functions
- Maintenance
Use Cases
- Asset Lifecycle Management
- Predictive Maintenance
Services
- System Integration
The Challenge
Western Refining, an independent crude oil refiner and marketer of refined products throughout the Southwest, was using an aging legacy system for asset management. The system, which came with the purchase of the El Paso refinery and terminal assets from Chevron Texaco, promised powerful functionality to automate maintenance, purchasing, inventory, and related accounts payable. However, it was of an earlier generation and was deemed too complex, cumbersome, and expensive to maintain. The company felt they were missing out on opportunities to cut costs and improve efficiency. The functionality was probably there, but they just couldn’t get at it easily. Western Refining’s changing business needs prompted an evaluation of asset management system options.
About The Customer
Western Refining, Inc. is an independent crude oil refiner and marketer of refined products throughout the Southwest. The company has a crude processing capacity in excess of 117,000 barrels per day, with more than 90% of its refined products being light transportation fuels, including gasoline, diesel, and jet fuel. Serving primarily the Southwestern region of the U.S., Western Refining has approximately 4.3 million barrels of storage capacity, and a 45,000-barrel per day marketing terminal. The company is headquartered in El Paso, Texas.
The Solution
Western Refining chose Avantis.PRO Enterprise Asset Management software from AVEVA to replace their aging legacy system. The software helps manage the purchase of materials and services, including items for minor maintenance and repairs, as well as items that are specially requisitioned for projects and office needs. It also helps track materials, maintenance employees, contract labor, and other resources. The company implemented several modules from the Avantis.PRO Enterprise Asset Management suite, including Entity Management, Work Management, Preventive Maintenance, MRO Inventory, and Procurement. The software provides full accountability from the moment that a person issues a work order, requisitions materials, or contracts labor.
Operational Impact
Related Case Studies.
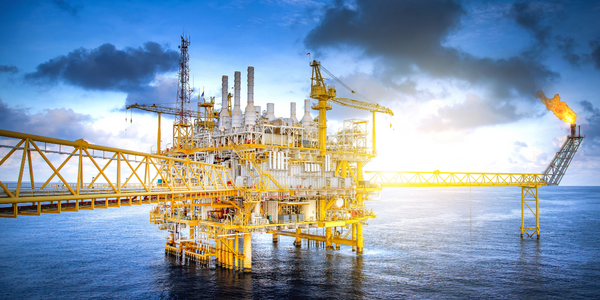
Case Study
Taking Oil and Gas Exploration to the Next Level
DownUnder GeoSolutions (DUG) wanted to increase computing performance by 5 to 10 times to improve seismic processing. The solution must build on current architecture software investments without sacrificing existing software and scale computing without scaling IT infrastructure costs.
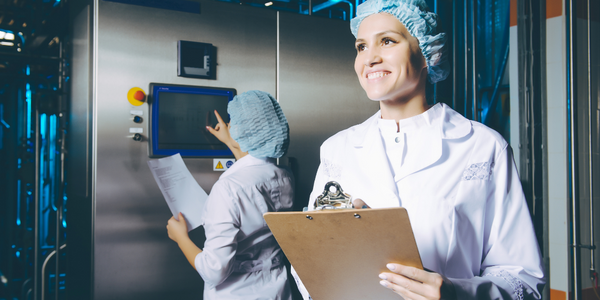
Case Study
Remote Wellhead Monitoring
Each wellhead was equipped with various sensors and meters that needed to be monitored and controlled from a central HMI, often miles away from the assets in the field. Redundant solar and wind generators were installed at each wellhead to support the electrical needs of the pumpstations, temperature meters, cameras, and cellular modules. In addition to asset management and remote control capabilities, data logging for remote surveillance and alarm notifications was a key demand from the customer. Terra Ferma’s solution needed to be power efficient, reliable, and capable of supporting high-bandwidth data-feeds. They needed a multi-link cellular connection to a central server that sustained reliable and redundant monitoring and control of flow meters, temperature sensors, power supply, and event-logging; including video and image files. This open-standard network needed to interface with the existing SCADA and proprietary network management software.
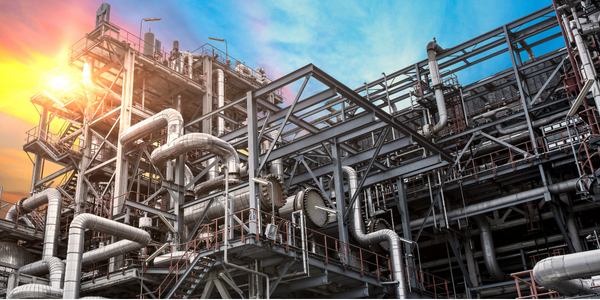
Case Study
Refinery Saves Over $700,000 with Smart Wireless
One of the largest petroleum refineries in the world is equipped to refine various types of crude oil and manufacture various grades of fuel from motor gasoline to Aviation Turbine Fuel. Due to wear and tear, eight hydrogen valves in each refinery were leaking, and each cost $1800 per ton of hydrogen vented. The plant also had leakage on nearly 30 flare control hydrocarbon valves. The refinery wanted a continuous, online monitoring system that could catch leaks early, minimize hydrogen and hydrocarbon production losses, and improve safety for maintenance.