Download PDF
Optimizing Offshore Oil Separation with IoT: A Case Study on Natco Group, Inc.
Technology Category
- Sensors - Gas Sensors
- Sensors - Utility Meters
Applicable Industries
- Chemicals
- Oil & Gas
Applicable Functions
- Product Research & Development
- Quality Assurance
Use Cases
- Intelligent Urban Water Supply Management
- Leakage & Flood Monitoring
Services
- System Integration
- Testing & Certification
The Challenge
As the demand for offshore oil field services continues to rise, NATCO Group, Inc. was faced with the challenge of optimizing the performance of its induced gas flotation (IGF) system for customers producing oil on offshore platforms. The IGF system, which uses gas bubbles to trap oil and solids for separation from wastewater, was not as effective in vertical water treatment vessels due to their limited deck space and weight restrictions. These vertical systems often caused uneven distribution of gas bubbles, making the separation process less efficient. Furthermore, traditional physical testing methods to improve the system were costly, time-consuming, and lacked clear insight into why a design was or wasn't working.
About The Customer
NATCO Group, Inc. is a leading provider of wellhead process equipment, systems, and services used in the production of oil and gas. With over 75 years of experience in designing and manufacturing production equipment, the company has established a strong presence both onshore and offshore in most major oil and gas producing regions of the world. Their commitment to innovation and efficiency is evident in their continuous efforts to optimize their services and products, such as the induced gas flotation (IGF) system, to meet the growing demands of the industry.
The Solution
To overcome these challenges, NATCO's engineers turned to Fluent CFD software. This allowed them to simulate the performance of several initial design concepts before moving to the prototype stage, saving both time and resources. The software verified that the initial design required significant improvement, leading the team to evaluate a number of design variations. After modifying hardware designs for physical testing, they ultimately developed a new design based on the simulation results. This innovative approach not only improved the efficiency of the IGF system but also validated the accuracy of the ANSYS simulation results when the platforms and pumps successfully withstood the loading of mechanical equipment without excessive vibration at key locations during Category 2 Hurricane Gustav in 2008.
Operational Impact
Quantitative Benefit
Related Case Studies.
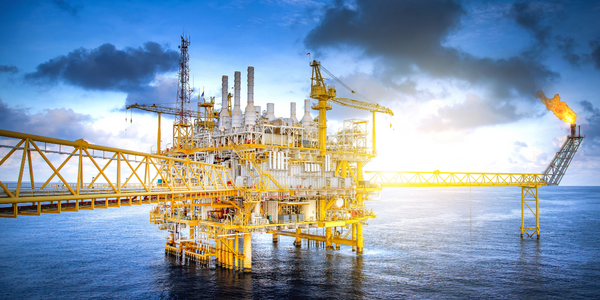
Case Study
Taking Oil and Gas Exploration to the Next Level
DownUnder GeoSolutions (DUG) wanted to increase computing performance by 5 to 10 times to improve seismic processing. The solution must build on current architecture software investments without sacrificing existing software and scale computing without scaling IT infrastructure costs.
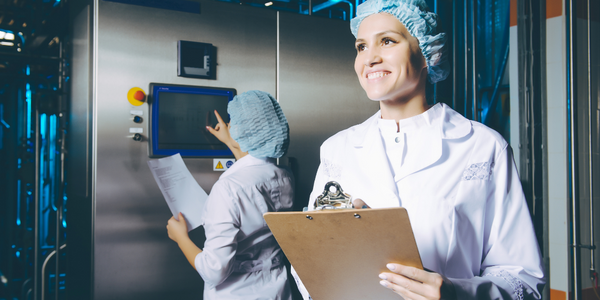
Case Study
Remote Wellhead Monitoring
Each wellhead was equipped with various sensors and meters that needed to be monitored and controlled from a central HMI, often miles away from the assets in the field. Redundant solar and wind generators were installed at each wellhead to support the electrical needs of the pumpstations, temperature meters, cameras, and cellular modules. In addition to asset management and remote control capabilities, data logging for remote surveillance and alarm notifications was a key demand from the customer. Terra Ferma’s solution needed to be power efficient, reliable, and capable of supporting high-bandwidth data-feeds. They needed a multi-link cellular connection to a central server that sustained reliable and redundant monitoring and control of flow meters, temperature sensors, power supply, and event-logging; including video and image files. This open-standard network needed to interface with the existing SCADA and proprietary network management software.
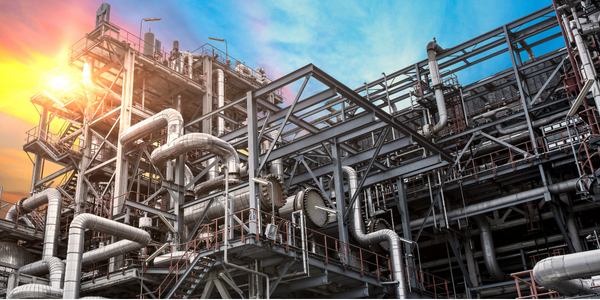
Case Study
Refinery Saves Over $700,000 with Smart Wireless
One of the largest petroleum refineries in the world is equipped to refine various types of crude oil and manufacture various grades of fuel from motor gasoline to Aviation Turbine Fuel. Due to wear and tear, eight hydrogen valves in each refinery were leaking, and each cost $1800 per ton of hydrogen vented. The plant also had leakage on nearly 30 flare control hydrocarbon valves. The refinery wanted a continuous, online monitoring system that could catch leaks early, minimize hydrogen and hydrocarbon production losses, and improve safety for maintenance.
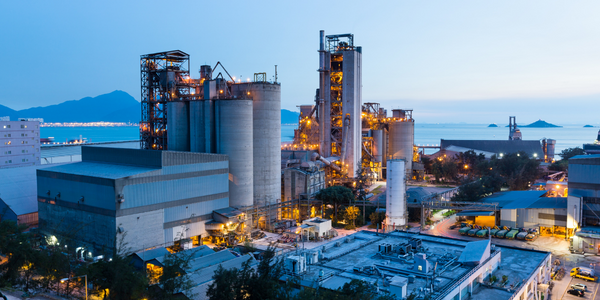
Case Study
Honeywell - Tata Chemicals Improves Data Accessibility with OneWireless
Tata was facing data accessibility challenges in the cement plant control room tapping signals from remote process control areas and other distant locations, including the gas scrubber. Tata needed a wireless solution to extend its control network securely to remote locations that would also provide seamless communication with existing control applications.