Download PDF
Pacific Coffee Enhances Customer Loyalty and Secures POS Platform with Check Point Safe@Office
Technology Category
- Cybersecurity & Privacy - Network Security
- Networks & Connectivity - Gateways
Applicable Industries
- Buildings
- Retail
Applicable Functions
- Procurement
- Sales & Marketing
Use Cases
- Inventory Management
- Tamper Detection
Services
- Cybersecurity Services
- System Integration
The Challenge
Pacific Coffee Company, a rapidly growing coffee chain with around 80 retail outlets throughout Singapore, Hong Kong, and China, faced a significant challenge when transitioning from conventional cash registers to a modern, integrated Point-of-Sale (POS) system. The challenge was primarily related to network security, especially with the introduction of a new customer loyalty card program, the Perfect Cup Card. This card, which replaced the previous paper card system, required the secure sharing of real-time transaction data between the POS terminals in coffee outlets and the main data center. The company needed a solution that could securely handle this data transfer, protect the POS systems from potential security threats, and support the new sales and marketing initiatives associated with the Perfect Cup Card.
About The Customer
Pacific Coffee Company Limited, established in 1992, has been providing world-class coffee to meet the growing demand for specialty coffee beverages in Hong Kong, China, and Singapore. The company has around 80 retail outlets throughout these regions, with over 60 stores in Hong Kong. Pacific Coffee Company is committed to technology, offering customers the ultimate in communication services. The chain is known for its world-class coffee, great tasting food, comfortable surroundings, and in-store Internet availability. The company is also focused on enhancing customer loyalty through innovative programs like the Perfect Cup Card.
The Solution
Pacific Coffee Company adopted Check Point Safe@Office VPN to support its customer loyalty program and protect real-time data as it travels across the Internet. The Safe@Office appliance was installed in every coffeehouse, connecting to the data center of the Perfect Cup Card service provider. The implementation was simple and quick, with the rollout to nearly sixty coffeehouses completed within 12 days. Safe@Office was chosen after a month-long evaluation that reviewed criteria including link rebuild, traffic shopping, reliability, and compatibility with other firewall systems. It provided the best performance/price ratio among all the solutions evaluated. The Safe@Office appliances are designed to work in extreme environments, such as near coffee machines and food preparation areas, and are largely unaffected when the air-conditioning is switched off overnight.
Operational Impact
Quantitative Benefit
Related Case Studies.
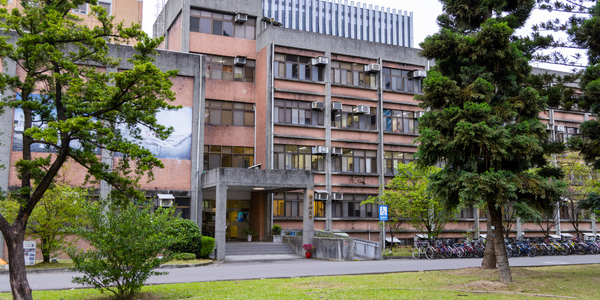
Case Study
Energy Saving & Power Monitoring System
Recently a university in Taiwan was experiencing dramatic power usage increases due to its growing number of campus buildings and students. Aiming to analyze their power consumption and increase their power efficiency across 52 buildings, the university wanted to build a power management system utilizing web-based hardware and software. With these goals in mind, they contacted Advantech to help them develop their system and provide them with the means to save energy in the years to come.
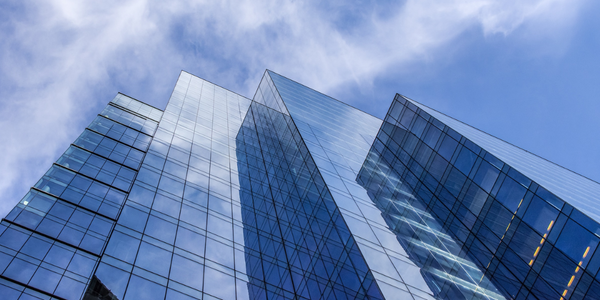
Case Study
Intelligent Building Automation System and Energy Saving Solution
One of the most difficult problems facing the world is conserving energy in buildings. However, it is not easy to have a cost-effective solution to reduce energy usage in a building. One solution for saving energy is to implement an intelligent building automation system (BAS) which can be controlled according to its schedule. In Indonesia a large university with a five floor building and 22 classrooms wanted to save the amount of energy being used.
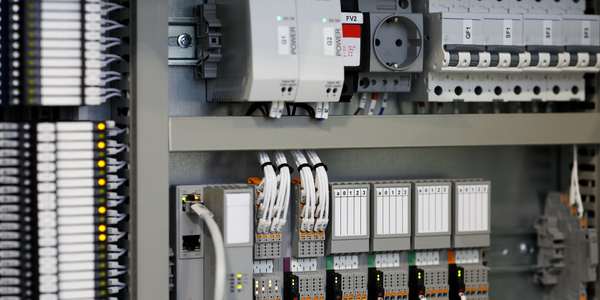
Case Study
Improving Production Line Efficiency with Ethernet Micro RTU Controller
Moxa was asked to provide a connectivity solution for one of the world's leading cosmetics companies. This multinational corporation, with retail presence in 130 countries, 23 global braches, and over 66,000 employees, sought to improve the efficiency of their production process by migrating from manual monitoring to an automatic productivity monitoring system. The production line was being monitored by ABB Real-TPI, a factory information system that offers data collection and analysis to improve plant efficiency. Due to software limitations, the customer needed an OPC server and a corresponding I/O solution to collect data from additional sensor devices for the Real-TPI system. The goal is to enable the factory information system to more thoroughly collect data from every corner of the production line. This will improve its ability to measure Overall Equipment Effectiveness (OEE) and translate into increased production efficiencies. System Requirements • Instant status updates while still consuming minimal bandwidth to relieve strain on limited factory networks • Interoperable with ABB Real-TPI • Small form factor appropriate for deployment where space is scarce • Remote software management and configuration to simplify operations
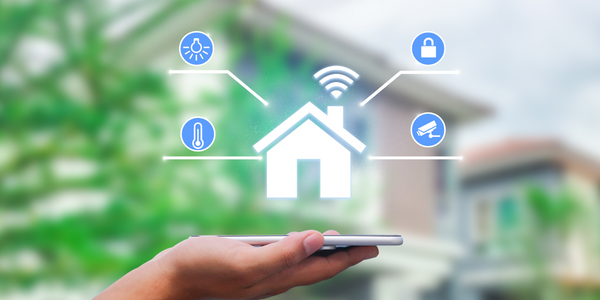
Case Study
Powering Smart Home Automation solutions with IoT for Energy conservation
Many industry leaders that offer Smart Energy Management products & solutions face challenges including:How to build a scalable platform that can automatically scale-up to on-board ‘n’ number of Smart home devicesData security, solution availability, and reliability are the other critical factors to deal withHow to create a robust common IoT platform that handles any kind of smart devicesHow to enable data management capabilities that would help in intelligent decision-making