Download PDF
Pranav Vikas Achieves Material Savings and Optimised Product Designs with Altair HyperWorks™ Solutions
Technology Category
- Analytics & Modeling - Digital Twin / Simulation
- Sensors - Utility Meters
Applicable Industries
- Life Sciences
- Oil & Gas
Applicable Functions
- Facility Management
- Product Research & Development
Use Cases
- Manufacturing Process Simulation
- Virtual Prototyping & Product Testing
Services
- Testing & Certification
The Challenge
Pranav Vikas (India) Private Limited (PVL), a leading heat-exchanger manufacturer in India, faced several challenges in their manufacturing process. The rapidly changing vehicle market and customer requirements necessitated the use of lightweight materials for components to maintain compact product sizes. This required thorough testing and implementation of every new material for product optimization, pushing the team to innovate and develop new manufacturing processes and engineering techniques. Additionally, PVL had to address warranty issues in existing products. Two distinct challenges were faced in recent projects: an oil cooler failure on the Pad-Plate joint for a model that had been in operation for five years, and the need for a design overhaul of the inlet/outlet pipes of a heat exchanger product that required weight reduction without causing warranty failure issues.
About The Customer
Pranav Vikas (India) Private Limited (PVL) is one of the largest and most diversified heat-exchanger manufacturers in India with over two decades of experience. PVL operates out of three locations in India, each focusing on specific product lines and market segments. The company is the only fully integrated Condenser manufacturer in India with their own state-of-the-art Micro-tube facility. PVL serves leading global and Indian Original Equipment Manufacturers (OEMs) in the Passenger, Commercial, and Off-road vehicle segments. Some of their major customers include Mahindra and Mahindra, Bajaj Auto Ltd., Tata Motors, Sanden Vikas/Maruti Suzuki, General Motors, Hindustan Motors, Honda, Kawasaki, Hero MotoCorp, VE Commercial Vehicles Ltd., Escorts, Haier, Videocon, Kohler, and Bergstrom.
The Solution
PVL chose Altair HyperWorks as their partner for design and simulation requirements. For the oil cooler failure issue, the team simulated the oil cooler in Altair HyperWorks for Road Load and Engine Vibration Load conditions. The simulations revealed that a fixture in the assembly process was causing pre-stressing of the oil cooler, leading to the Pad-Plate joint failure. The fixture was removed, resolving the issue. For the pipe bend issue, the team used Altair HyperMesh™ and Altair OptiStruct to simulate the heat exchanger inlet/outlet pipes, significantly reducing the product weight. To address concerns about warranty failures due to thinning and thickening during the bending process, the team used Altair HyperForm™ for bending of the pipes and measured the thinning and thickening percentages. The required structural analysis on the pipes yielded positive results, leading to lighter pipes without concerns of warranty failures.
Operational Impact
Quantitative Benefit
Related Case Studies.
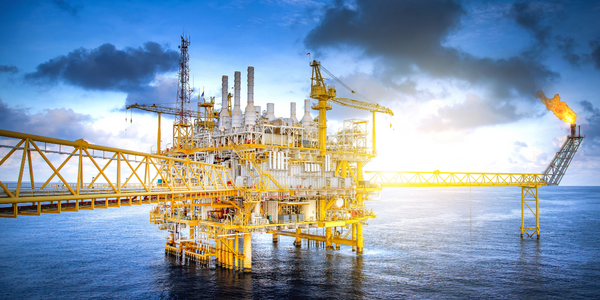
Case Study
Taking Oil and Gas Exploration to the Next Level
DownUnder GeoSolutions (DUG) wanted to increase computing performance by 5 to 10 times to improve seismic processing. The solution must build on current architecture software investments without sacrificing existing software and scale computing without scaling IT infrastructure costs.
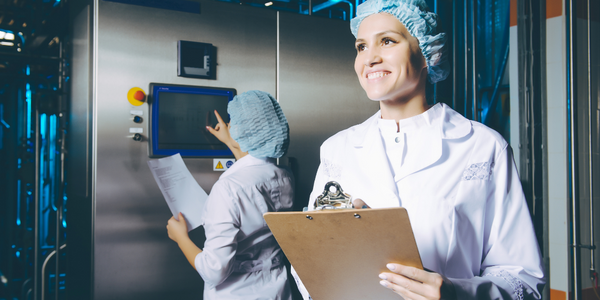
Case Study
Remote Wellhead Monitoring
Each wellhead was equipped with various sensors and meters that needed to be monitored and controlled from a central HMI, often miles away from the assets in the field. Redundant solar and wind generators were installed at each wellhead to support the electrical needs of the pumpstations, temperature meters, cameras, and cellular modules. In addition to asset management and remote control capabilities, data logging for remote surveillance and alarm notifications was a key demand from the customer. Terra Ferma’s solution needed to be power efficient, reliable, and capable of supporting high-bandwidth data-feeds. They needed a multi-link cellular connection to a central server that sustained reliable and redundant monitoring and control of flow meters, temperature sensors, power supply, and event-logging; including video and image files. This open-standard network needed to interface with the existing SCADA and proprietary network management software.
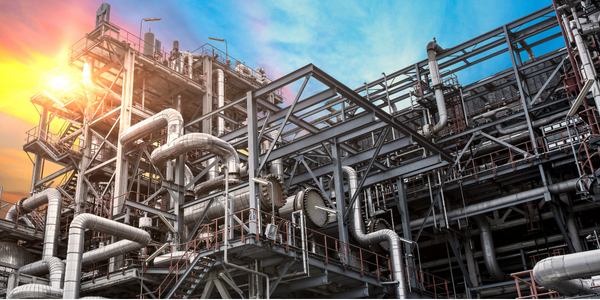
Case Study
Refinery Saves Over $700,000 with Smart Wireless
One of the largest petroleum refineries in the world is equipped to refine various types of crude oil and manufacture various grades of fuel from motor gasoline to Aviation Turbine Fuel. Due to wear and tear, eight hydrogen valves in each refinery were leaking, and each cost $1800 per ton of hydrogen vented. The plant also had leakage on nearly 30 flare control hydrocarbon valves. The refinery wanted a continuous, online monitoring system that could catch leaks early, minimize hydrogen and hydrocarbon production losses, and improve safety for maintenance.