Download PDF
Raising safety, efficiency and quality in steel production with proactive maintenance planning
Technology Category
- Functional Applications - Enterprise Asset Management Systems (EAM)
Applicable Industries
- Metals
Applicable Functions
- Maintenance
Use Cases
- Predictive Maintenance
Services
- System Integration
The Challenge
Outokumpu, a leading manufacturer of steel products, realized that by moving from reactive to proactive maintenance for its production line machines, it could improve availability, efficiency, quality and safety at its Avesta steel mill. The mill is known for the special grades of stainless steel it produces for the offshore oil and gas industry. Delivering a product that can withstand corrosive saltwater and extreme weather conditions requires very precise control of production processes. At the same time, production needs to be efficient and uninterrupted to meet the expectations of demanding clients, whose multi-million dollar offshore construction projects depend on Outokumpu’s ability to deliver the right materials at the right time. The company's top priority is always to keep all its employees safe while they work in the mill.
About The Customer
Outokumpu is a leading manufacturer of steel products, with its headquarters in Espoo, Finland. The company's mill in Avesta, Sweden is known for the special grades of stainless steel it produces for the offshore oil and gas industry. The mill employs around 700 people, recycling scrap steel into specialized grades of stainless steel products. The products are designed to withstand corrosive saltwater and extreme weather conditions, making them ideal for use in the offshore oil and gas industries. The mill's production processes need to be efficient and uninterrupted to meet the expectations of its demanding clients, whose multi-million dollar offshore construction projects depend on Outokumpu’s ability to deliver the right materials at the right time.
The Solution
Outokumpu, working with IBM Business Partner Enfo Framsteg, designed a new maintenance process that treats each machine as an individual, transforming availability and performance. The company has been using IBM Maximo Asset Management software to organize its maintenance processes at Avesta for over 20 years. Enfo Framsteg helped Outokumpu reconfigure its Maximo landscape to take greater advantage of the Maximo Scheduler tool, which proved a vital advantage in re-engineering the company’s maintenance processes. The new process gives Outokumpu a much better ability to plan ahead and get all the right resources in place before starting on a maintenance job. Instead of purchasing and storing spare parts for production line machines on the off-chance that they will be needed, the company can be much smarter about only ordering what it needs, saving considerable costs.
Operational Impact
Quantitative Benefit
Related Case Studies.
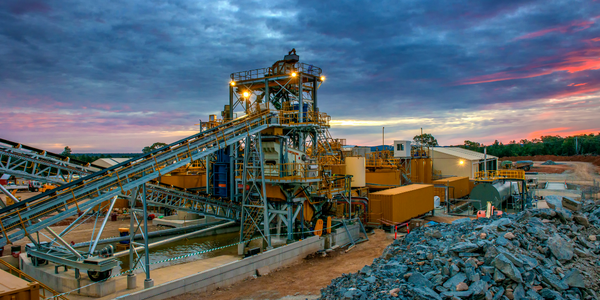
Case Study
Goldcorp: Internet of Things Enables the Mine of the Future
Goldcorp is committed to responsible mining practices and maintaining maximum safety for its workers. At the same time, the firm is constantly exploring ways to improve the efficiency of its operations, extend the life of its assets, and control costs. Goldcorp needed technology that can maximize production efficiency by tracking all mining operations, keep employees safe with remote operations and monitoring of hazardous work areas and control production costs through better asset and site management.
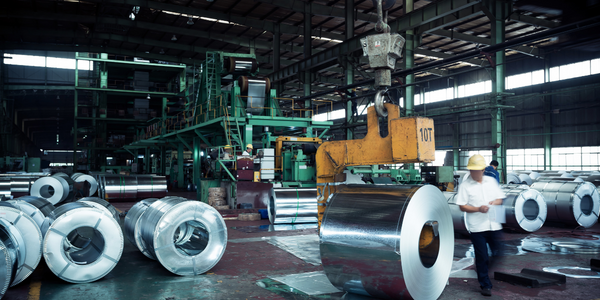
Case Study
KSP Steel Decentralized Control Room
While on-site in Pavlodar, Kazakhstan, the DAQRI team of Business Development and Solutions Architecture personnel worked closely with KSP Steel’s production leadership to understand the steel production process, operational challenges, and worker pain points.
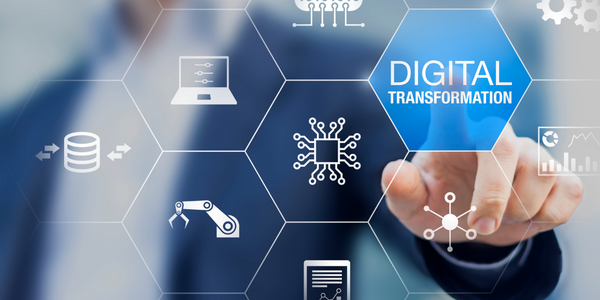
Case Study
Bluescope Steel on Path to Digitally Transform Operations and IT
Increasing competition and fluctuations in the construction market prompted BlueScope Steel to look toward digital transformation of its four businesses, including modern core applications and IT infrastructure. BlueScope needed to modernize its infrastructure and adopt new technologies to improve operations and supply chain efficiency while maintaining and updating an aging application portfolio.
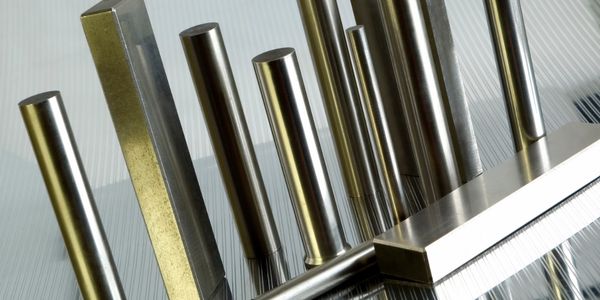
Case Study
RobotStudio Case Study: Benteler Automobiltechnik
Benteler has a small pipe business area for which they produce fuel lines and coolant lines made of aluminum for Porsche and other car manufacturers. One of the problems in production was that when Benteler added new products, production had too much downtime.
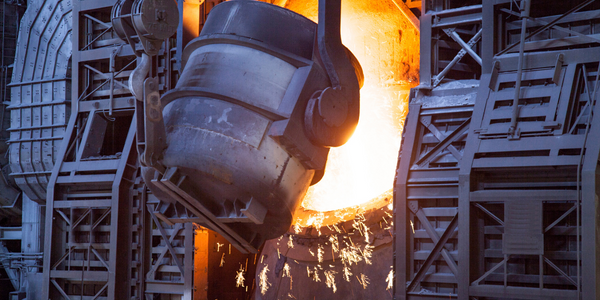
Case Study
Continuous Casting Machines in a Steel Factory
With a very broad range of applications, steel is an important material and has been developed into the most extensive alloy in the engineering world. Since delivering high quality is absolutely crucial for steel plants, ensuring maximum productivity and the best quality production are the keys to competitiveness in the steel industry. Additionally, working conditions in steel factories are not suitable for workers to stay in for long periods of time, so manufactures usually adopt various machines to complete the steel production processes. However, the precision of these machines is often overestimated and the lack of flexibility also makes supervisors unable to adjust operating procedures. A renowned steel factory in Asia planned to improve its Distributed Control System (DCS) of furnaces as well as addressing the problem of insufficient accuracy. However, most well-known international equipment suppliers can not provide a satisfactory solution and local maintenance because the project needed new technologies to more accurately control equipment operations. By implementing Advantech’s automated monitoring and control solution, steel factories can not only improve the manufacturing processes but can also allow users to add additional functions to the existing system so as to make sure the operation runs at high efficiency.
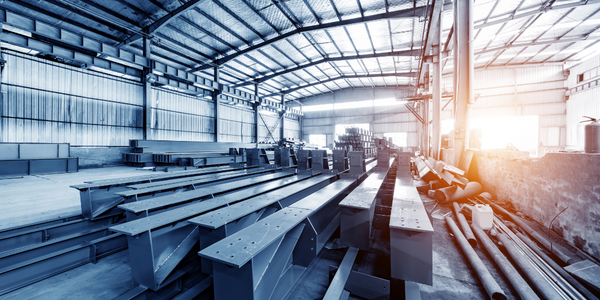
Case Study
Automated Predicitive Analytics For Steel/Metals Industry
Asset to be monitored: Wire Compactor that produces Steel RebarCustomer Faced The Following Challenges:Dependent upon machine uptime.Pressure cylinders within the compactor fail to control compression and speed causing problems in binding the coil.Equipment failure occurs in the final stage of production causing the entire line to stop, can you say bottleneck?Critical asset unequipped with sensors to produce data.