Download PDF
Rapid Expansion of BDS Group Inc. with Axon Software
Technology Category
- Networks & Connectivity - Global Navigation Satellite System (GNSS)
Applicable Industries
- Automotive
- Buildings
Applicable Functions
- Procurement
Use Cases
- Driver Performance Monitoring
- Time Sensitive Networking
Services
- System Integration
The Challenge
BDS Group Inc., a trucking company specializing in heavy haul and fluid hauling, was facing significant operational challenges due to its rapid growth. The company, which operates out of Camrose, Alberta, and Watford City, North Dakota, had expanded from 11 trucks to 80 in less than six months. This rapid expansion put a strain on their existing operational processes, particularly in terms of paperwork and invoicing. Prior to implementing Axon software, the company was using multiple software programs for different aspects of the business, which was inefficient and time-consuming. Invoicing was a particularly cumbersome process, with tickets having to go through three sets of eyes before being processed. This was not only slow but also required drivers to physically bring paperwork into the office, further delaying the process.
About The Customer
BDS Group Inc. is a trucking company that specializes in heavy haul and fluid hauling. The company operates heavy trucks, ranging from 6-axle to 60-axle, and picker trucks, from 45-ton to 250-ton. BDS Group Inc. operates out of Camrose, Alberta, and Watford City, North Dakota. The company was founded in 1978 by Bill Simons with a single truck and has since grown significantly. Today, the company is managed by Bill's sons, Ryan and Michael, and has expanded to operate 80 trucks, including both company-owned and owner-operated vehicles.
The Solution
BDS Group Inc. implemented Axon software to streamline their operations and manage their rapid growth. The software allowed the company to consolidate all their operations into one program, significantly simplifying their processes. The Axon Link app, in particular, revolutionized their invoicing process. Drivers could now upload their tickets directly through the app, eliminating the need for them to physically bring paperwork into the office. This allowed invoices to be processed in a matter of minutes, significantly speeding up the process. The software also helped the company manage their growing number of owner operators, providing detailed statements and allowing them to be set up just like employees. Additionally, the software's Work Order/Shop system was integrated with the trucking and accounting system, allowing for direct invoicing of customers without the need for extra work orders or tickets.
Operational Impact
Quantitative Benefit
Related Case Studies.
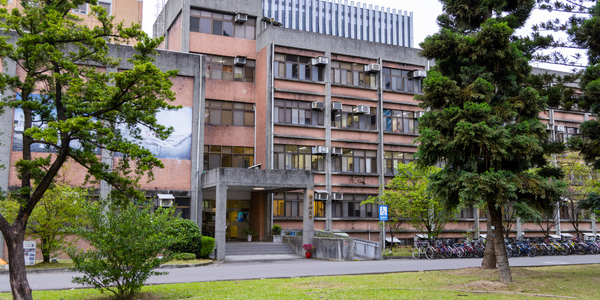
Case Study
Energy Saving & Power Monitoring System
Recently a university in Taiwan was experiencing dramatic power usage increases due to its growing number of campus buildings and students. Aiming to analyze their power consumption and increase their power efficiency across 52 buildings, the university wanted to build a power management system utilizing web-based hardware and software. With these goals in mind, they contacted Advantech to help them develop their system and provide them with the means to save energy in the years to come.
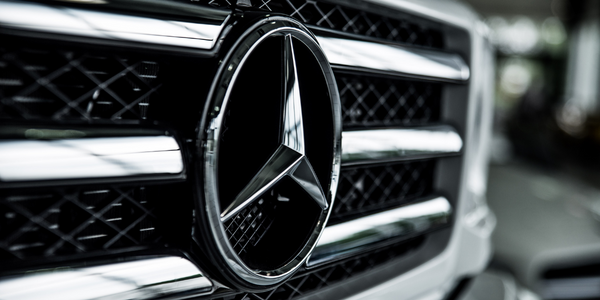
Case Study
Integral Plant Maintenance
Mercedes-Benz and his partner GAZ chose Siemens to be its maintenance partner at a new engine plant in Yaroslavl, Russia. The new plant offers a capacity to manufacture diesel engines for the Russian market, for locally produced Sprinter Classic. In addition to engines for the local market, the Yaroslavl plant will also produce spare parts. Mercedes-Benz Russia and his partner needed a service partner in order to ensure the operation of these lines in a maintenance partnership arrangement. The challenges included coordinating the entire maintenance management operation, in particular inspections, corrective and predictive maintenance activities, and the optimizing spare parts management. Siemens developed a customized maintenance solution that includes all electronic and mechanical maintenance activities (Integral Plant Maintenance).
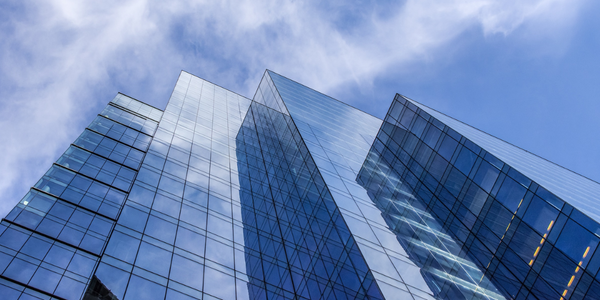
Case Study
Intelligent Building Automation System and Energy Saving Solution
One of the most difficult problems facing the world is conserving energy in buildings. However, it is not easy to have a cost-effective solution to reduce energy usage in a building. One solution for saving energy is to implement an intelligent building automation system (BAS) which can be controlled according to its schedule. In Indonesia a large university with a five floor building and 22 classrooms wanted to save the amount of energy being used.
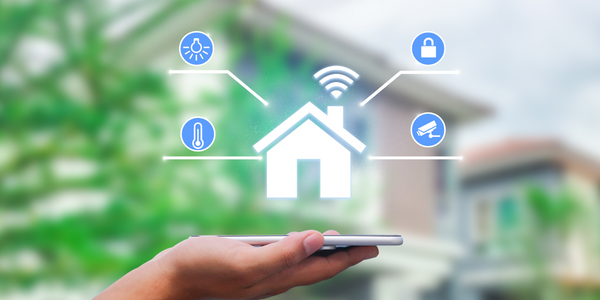
Case Study
Powering Smart Home Automation solutions with IoT for Energy conservation
Many industry leaders that offer Smart Energy Management products & solutions face challenges including:How to build a scalable platform that can automatically scale-up to on-board ‘n’ number of Smart home devicesData security, solution availability, and reliability are the other critical factors to deal withHow to create a robust common IoT platform that handles any kind of smart devicesHow to enable data management capabilities that would help in intelligent decision-making