Download PDF
Reducing Material Costs by up to 30%
Technology Category
- Analytics & Modeling - Predictive Analytics
- Functional Applications - Manufacturing Execution Systems (MES)
Applicable Industries
- Food & Beverage
Applicable Functions
- Quality Assurance
- Process Manufacturing
Use Cases
- Machine Condition Monitoring
- Predictive Maintenance
- Process Control & Optimization
Services
- Software Design & Engineering Services
- System Integration
The Challenge
Customer satisfaction is a critical issue for the McCormick Flavor Division, which produces sauces, dressings, and condiments for major restaurants and fast food chains. The company faced challenges in presenting data during customer audits and needed to improve their process control to reduce waste and improve the bottom line. They also needed to better understand the natural variation in their processes to make adjustments closer to target fill weights and reduce material costs.
About The Customer
McCormick & Company, Inc. is a global leader in flavor, producing a wide range of products including sauces, dressings, and condiments for some of the world's largest restaurants and fast food chains. The McCormick Flavor Division, located in South Bend, Indiana, is dedicated to maintaining high customer satisfaction and continuously improving their processes. The company has a strong focus on quality and efficiency, leveraging advanced data acquisition and analysis tools to optimize their operations and meet stringent customer requirements.
The Solution
McCormick implemented Hertzler's GainSeeker Suite to enhance their data acquisition and process control capabilities. By using control charts within the GainSeeker Suite, the company was able to listen to the 'voice of the process' and understand natural variations. This allowed them to adjust processes closer to target fill weights and reduce material costs. The automated data collection capabilities of GainSeeker significantly reduced the cost of obtaining data, enabling the company to perform more frequent and targeted checks. This system also allowed McCormick to better understand the operating range of their equipment and reset specifications to reflect actual process capabilities. The company plans to expand the use of GainSeeker to include temperature monitoring for coolers, ensuring tight temperature control and automatic notifications for special cause variations.
Operational Impact
Quantitative Benefit
Related Case Studies.
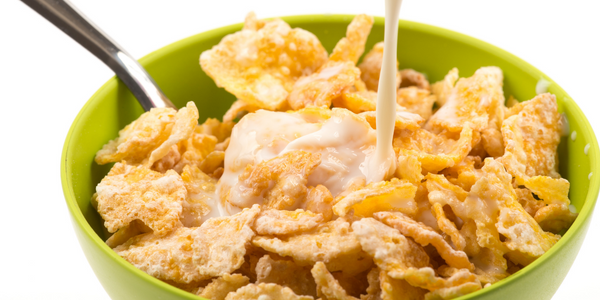
Case Study
The Kellogg Company
Kellogg keeps a close eye on its trade spend, analyzing large volumes of data and running complex simulations to predict which promotional activities will be the most effective. Kellogg needed to decrease the trade spend but its traditional relational database on premises could not keep up with the pace of demand.
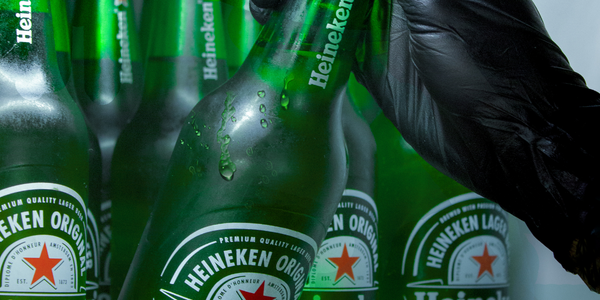
Case Study
HEINEKEN Uses the Cloud to Reach 10.5 Million Consumers
For 2012 campaign, the Bond promotion, it planned to launch the campaign at the same time everywhere on the planet. That created unprecedented challenges for HEINEKEN—nowhere more so than in its technology operation. The primary digital content for the campaign was a 100-megabyte movie that had to play flawlessly for millions of viewers worldwide. After all, Bond never fails. No one was going to tolerate a technology failure that might bruise his brand.Previously, HEINEKEN had supported digital media at its outsourced datacenter. But that datacenter lacked the computing resources HEINEKEN needed, and building them—especially to support peak traffic that would total millions of simultaneous hits—would have been both time-consuming and expensive. Nor would it have provided the geographic reach that HEINEKEN needed to minimize latency worldwide.
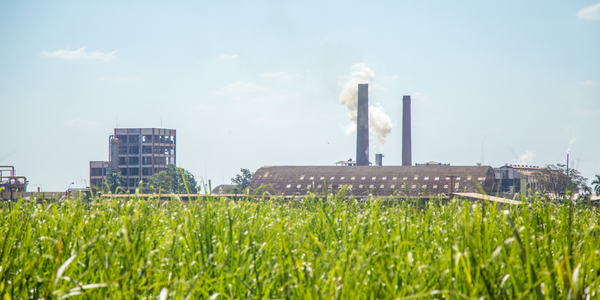
Case Study
Energy Management System at Sugar Industry
The company wanted to use the information from the system to claim under the renewable energy certificate scheme. The benefit to the company under the renewable energy certificates is Rs 75 million a year. To enable the above, an end-to-end solution for load monitoring, consumption monitoring, online data monitoring, automatic meter data acquisition which can be exported to SAP and other applications is required.
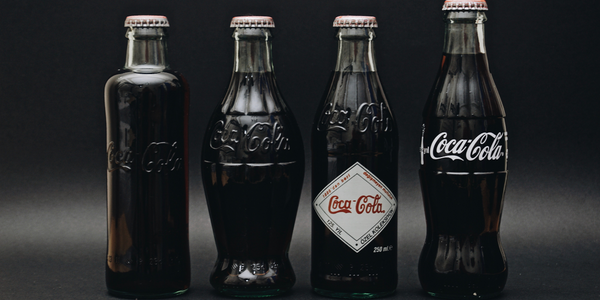
Case Study
Coca Cola Swaziland Conco Case Study
Coco Cola Swaziland, South Africa would like to find a solution that would enable the following results: - Reduce energy consumption by 20% in one year. - Formulate a series of strategic initiatives that would enlist the commitment of corporate management and create employee awareness while helping meet departmental targets and investing in tools that assist with energy management. - Formulate a series of tactical initiatives that would optimize energy usage on the shop floor. These would include charging forklifts and running cold rooms only during off-peak periods, running the dust extractors only during working hours and basing lights and air-conditioning on someone’s presence. - Increase visibility into the factory and other processes. - Enable limited, non-intrusive control functions for certain processes.
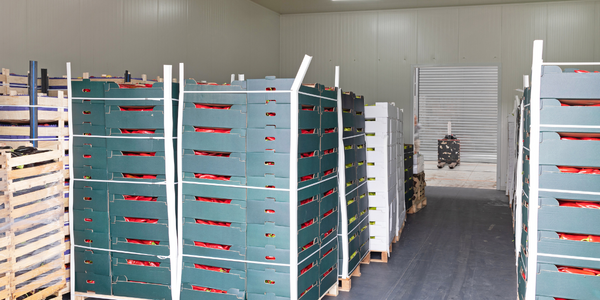
Case Study
Temperature Monitoring for Restaurant Food Storage
When it came to implementing a solution, Mr. Nesbitt had an idea of what functionality that he wanted. Although not mandated by Health Canada, Mr. Nesbitt wanted to ensure quality control issues met the highest possible standards as part of his commitment to top-of-class food services. This wish list included an easy-to use temperature-monitoring system that could provide a visible display of the temperatures of all of his refrigerators and freezers, including historical information so that he could review the performance of his equipment. It also had to provide alert notification (but email alerts and SMS text message alerts) to alert key staff in the event that a cooling system was exceeding pre-set warning limits.
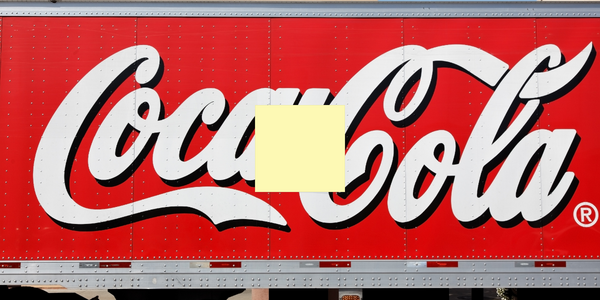
Case Study
Coca-Cola Refreshments, U.S.
Coca-Cola Refreshments owns and manages Coca-Cola branded refrigerators in retail establishments. Legacy systems were used to locate equipment information by logging onto multiple servers which took up to 8 hours to update information on 30-40 units. The company had no overall visibility into equipment status or maintenance history.