Remote Gas Pipeline Tunnel Temperature Monitoring System
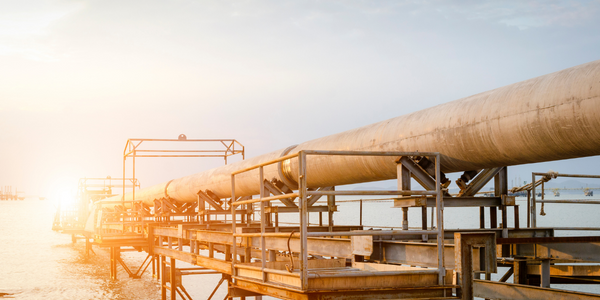
- Automation & Control - Supervisory Control & Data Acquisition (SCADA)
- Sensors - Temperature Sensors
- Oil & Gas
- Process Manufacturing
- Machine Condition Monitoring
One of Singapore's leading engineering and system integration providers needed exactly the right solution for a challenging gas pipeline application. With experience in assembling systems for many different vertical markets such as oil and gas networks, factory automation, and building automation, this system integrator realized that monitoring the temperature of a gas pipeline tunnel is crucial for safe operations. In the confined space of a tunnel, temperature rises easily, and the overheating could cause pipeline fractures that could lead to gas leaks or even explosions. Meanwhile, the long and narrow dimensions inherent to a tunnel meant that more home run cables must be installed to link all the temperature gauge data acquisition I/O devices back to the pipeline's SCADA system, increasing cabling costs. With these stakes and in these conditions, the simple act of regularly taking the temperature transforms into a formidable yet absolutely necessary requirement. System Requirements • Real-time tunnel temperature monitoring to provide early excessive heat warnings • Data acquisition and system management with SCADA system • Ethernet data acquisition system, but with efficient, cost-effective wiring
Moxa's ioLogik E1240 8AI daisy-chainable I/O proved up to the task. The ioLogik E1240 has two switch ports that can be used to daisy-chain one E1240 to another, reducing wiring costs by up to 15%. Moreover, the ioLogik E1240 supports Active OPC Server, which enables real-time temperature updates to the SCADA system. This Active OPC Server utilizes push technologies that not only reduces bandwidth consumption significantly but also increases system response time. Compared with traditional polling architectures that place extra demands on the network and SCADA CPU, active push-based tags that update the Active OPC Server automatically greatly reduces the demands on the system. The ioLogik's auto tag generation features delivers additional efficiency gains to SCADA builders by simplifying the creation of up to eight analog tags. Analog tags can be generated with just a few clicks and a press of the tag generation button. Product Solutions: ioLogik E1240 • Remote Ethernet I/O with 2-port Ethernet switch and 8 AIs • Two built-in Ethernet ports for cost-effective daisy-chain topologies • Free push-based Active OPC Server to seamless connect with any SCADA system • Push-based tag update architecture delivers real-time monitoring at reduces network load
Related Case Studies.
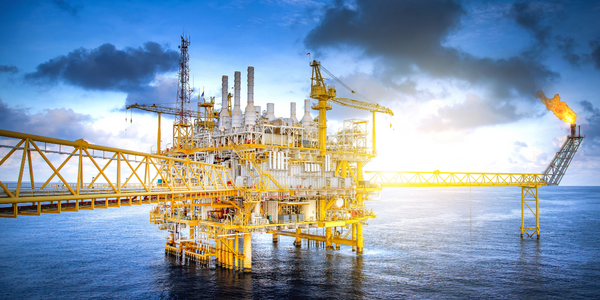
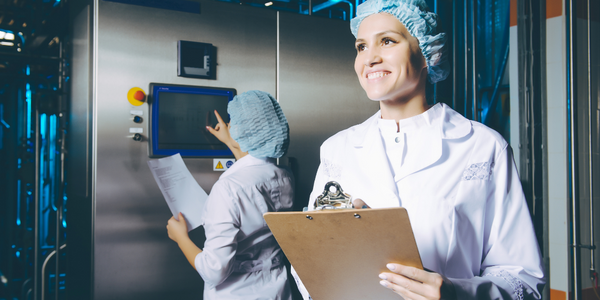
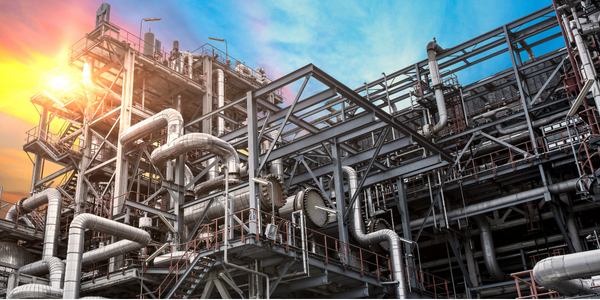