Download PDF
Sage 100 ERP Helps Overlake Oil Remain “All in the Family”
Technology Category
- Functional Applications - Enterprise Resource Planning Systems (ERP)
Applicable Industries
- Oil & Gas
Applicable Functions
- Sales & Marketing
- Business Operation
Use Cases
- Supply Chain Visibility
- Inventory Management
Services
- System Integration
The Challenge
Overlake Oil, a family-owned business in its third generation, was seeking to adopt the latest technology to streamline its operations. The company had computerized its business operations in 1982 with a UNIX-based system. However, by 1988, it had outgrown this system and needed to upgrade. The challenge was to find an accounting package that could seamlessly integrate with custom petroleum industry software. The company wanted more people to have access to the system and to be able to interface with Word, Excel, and the Internet. The company also wanted a system that could support its growth without requiring more staff.
About The Customer
Overlake Oil is a family-owned business based in Kirkland, Washington. The company is in its fifty-second year of business and third generation of family ownership. Founded by Harry Wright in 1947, Overlake has been a Shell affiliate since 1961, distributing Shell fuel and lubricants to commercial, industrial, and manufacturing companies. Steve Merrill, vice president, joined Overlake Oil in 1982. Several years later, Steve and his brother-in-law, Jim Jessen, began managing the business on their own. The company has one location and employs 13 people.
The Solution
Overlake Oil chose to implement Sage 100 ERP on a Novell network, customized for the petroleum industry by Steve Murphy at DM2 Software. Murphy had experience with both computer programming and the petroleum industry. He knew that the software programs available at that time could not provide a satisfactory system that accommodated both accounting functions and the special needs of the industry. Instead of starting from scratch to develop his own integrated accounting/petroleum package, Murphy decided to seek an existing accounting package and add his own petroleum component onto it. Murphy discovered that Sage 100 ERP met his criteria for flexibility and ease of use. Sage, the developer of Sage 100 ERP, and his company, DM2 Software, subsequently entered into a vertical market partnership. DM2 Software develops customized modules for the petroleum industry that seamlessly interface with Sage 100 ERP, providing a powerful package that offers petroleum distributors numerous business management advantages.
Operational Impact
Quantitative Benefit
Related Case Studies.
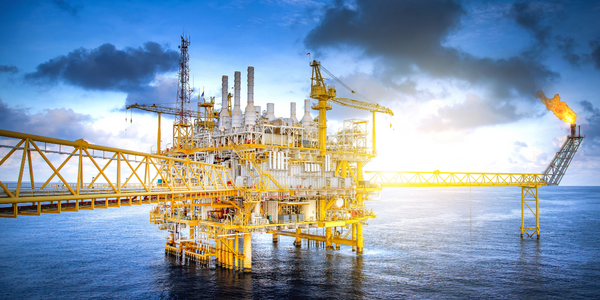
Case Study
Taking Oil and Gas Exploration to the Next Level
DownUnder GeoSolutions (DUG) wanted to increase computing performance by 5 to 10 times to improve seismic processing. The solution must build on current architecture software investments without sacrificing existing software and scale computing without scaling IT infrastructure costs.
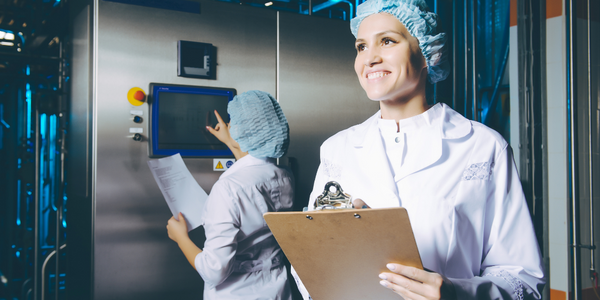
Case Study
Remote Wellhead Monitoring
Each wellhead was equipped with various sensors and meters that needed to be monitored and controlled from a central HMI, often miles away from the assets in the field. Redundant solar and wind generators were installed at each wellhead to support the electrical needs of the pumpstations, temperature meters, cameras, and cellular modules. In addition to asset management and remote control capabilities, data logging for remote surveillance and alarm notifications was a key demand from the customer. Terra Ferma’s solution needed to be power efficient, reliable, and capable of supporting high-bandwidth data-feeds. They needed a multi-link cellular connection to a central server that sustained reliable and redundant monitoring and control of flow meters, temperature sensors, power supply, and event-logging; including video and image files. This open-standard network needed to interface with the existing SCADA and proprietary network management software.
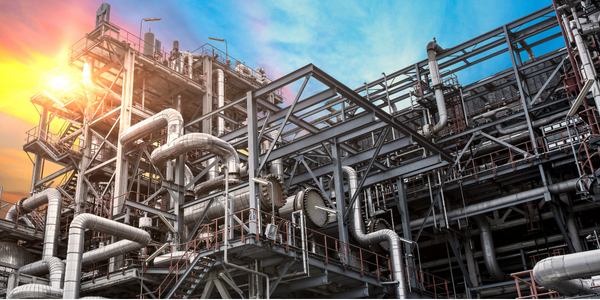
Case Study
Refinery Saves Over $700,000 with Smart Wireless
One of the largest petroleum refineries in the world is equipped to refine various types of crude oil and manufacture various grades of fuel from motor gasoline to Aviation Turbine Fuel. Due to wear and tear, eight hydrogen valves in each refinery were leaking, and each cost $1800 per ton of hydrogen vented. The plant also had leakage on nearly 30 flare control hydrocarbon valves. The refinery wanted a continuous, online monitoring system that could catch leaks early, minimize hydrogen and hydrocarbon production losses, and improve safety for maintenance.