Download PDF
Saving Space and Time through Warehouse Optimization
Technology Category
- Functional Applications - Warehouse Management Systems (WMS)
- Automation & Control - Automation & Process Control Systems
- Functional Applications - Remote Monitoring & Control Systems
Applicable Industries
- Retail
Applicable Functions
- Warehouse & Inventory Management
- Logistics & Transportation
Use Cases
- Warehouse Automation
- Fleet Management
- Inventory Management
Services
- System Integration
- Hardware Design & Engineering Services
- Software Design & Engineering Services
The Challenge
In 2002, The Container Store conducted a 10-year sales growth projection, which concluded that a larger facility would be necessary to contain its distribution center and corporate offices. Two years later, the company combined two smaller facilities into a 1.1 million-square-foot facility in Coppell, Texas. During those two years of planning, Mike Coronado, director of distribution, and the rest of the Distribution and Logistics management team had the challenging task of designing the DC, filling it with new equipment, and getting all systems integrated and running. One of The Container Store’s major initiatives was to ensure productivity and efficiency would be maintained in the new facility, even though it is 80 percent larger than the old distribution center. The Container Store wanted to mitigate increases to travel time by equipment and staff moving throughout the larger facility.
About The Customer
The Container Store is a leading retailer specializing in storage and organization solutions. Founded in 1978, the company has grown to become a prominent name in the retail industry, known for its wide range of products designed to help customers organize their homes and offices. The Container Store operates numerous retail locations across the United States and has a significant online presence. The company is committed to providing innovative and high-quality storage solutions to its customers. In 2002, The Container Store conducted a 10-year sales growth projection, which concluded that a larger facility would be necessary to contain its distribution center and corporate offices. Two years later, the company combined two smaller facilities into a 1.1 million-square-foot facility in Coppell, Texas.
The Solution
To accomplish the goal of designing and optimizing the new distribution center, The Container Store turned to Malin Integrated Handling Solutions, an authorized Raymond Sales and Service Center headquartered in Addison, Texas. Malin’s expertise and ability to provide a full range of material handling solutions were crucial in meeting The Container Store’s goals. Malin helped to design a double-deep racking system in which operators use Raymond Deep-Reach® trucks to maximize pallet positions. The Container Store’s previous distribution centers had very narrow aisles, using turret trucks to move pallets. In the new facility, wider 11-foot aisles allow multiple trucks for higher efficiency. The Container Store conducted focus groups of its DC associates to test, analyze, and choose the best equipment to do their jobs. Despite having years of experience with competitor-brand turret trucks, the focus groups objectively chose Raymond® lift trucks for the new facility. The Container Store’s lift truck fleet today is composed of 51 Raymond trucks, including pallet trucks, Deep-Reach trucks, sit-down and stand-up counterbalanced trucks, Model 5500 orderpickers, and Model 8600 tow tractors. The comprehensive Raymond Asset Protection™ maintenance agreement means a service technician from Malin is on site daily to perform both preventive and as-needed maintenance.
Operational Impact
Quantitative Benefit
Related Case Studies.
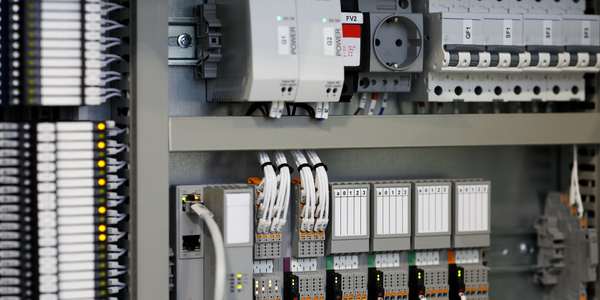
Case Study
Improving Production Line Efficiency with Ethernet Micro RTU Controller
Moxa was asked to provide a connectivity solution for one of the world's leading cosmetics companies. This multinational corporation, with retail presence in 130 countries, 23 global braches, and over 66,000 employees, sought to improve the efficiency of their production process by migrating from manual monitoring to an automatic productivity monitoring system. The production line was being monitored by ABB Real-TPI, a factory information system that offers data collection and analysis to improve plant efficiency. Due to software limitations, the customer needed an OPC server and a corresponding I/O solution to collect data from additional sensor devices for the Real-TPI system. The goal is to enable the factory information system to more thoroughly collect data from every corner of the production line. This will improve its ability to measure Overall Equipment Effectiveness (OEE) and translate into increased production efficiencies. System Requirements • Instant status updates while still consuming minimal bandwidth to relieve strain on limited factory networks • Interoperable with ABB Real-TPI • Small form factor appropriate for deployment where space is scarce • Remote software management and configuration to simplify operations
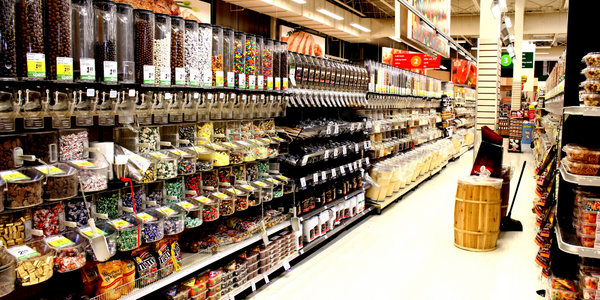
Case Study
How Sirqul’s IoT Platform is Crafting Carrefour’s New In-Store Experiences
Carrefour Taiwan’s goal is to be completely digital by end of 2018. Out-dated manual methods for analysis and assumptions limited Carrefour’s ability to change the customer experience and were void of real-time decision-making capabilities. Rather than relying solely on sales data, assumptions, and disparate systems, Carrefour Taiwan’s CEO led an initiative to find a connected IoT solution that could give the team the ability to make real-time changes and more informed decisions. Prior to implementing, Carrefour struggled to address their conversion rates and did not have the proper insights into the customer decision-making process nor how to make an immediate impact without losing customer confidence.
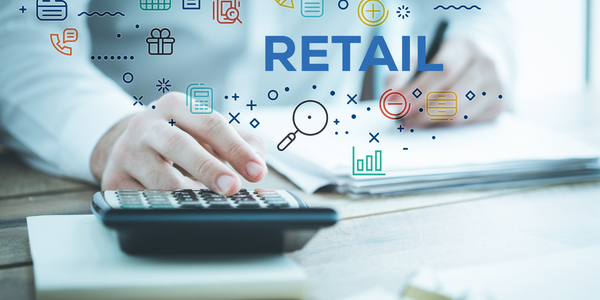
Case Study
Digital Retail Security Solutions
Sennco wanted to help its retail customers increase sales and profits by developing an innovative alarm system as opposed to conventional connected alarms that are permanently tethered to display products. These traditional security systems were cumbersome and intrusive to the customer shopping experience. Additionally, they provided no useful data or analytics.
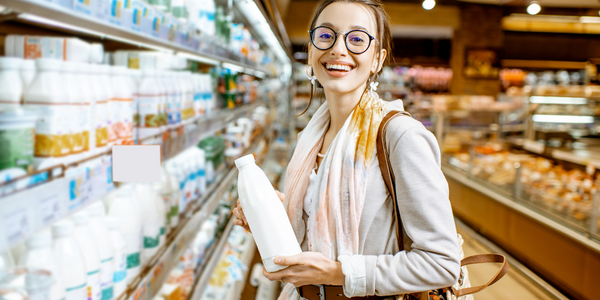
Case Study
Ensures Cold Milk in Your Supermarket
As of 2014, AK-Centralen has over 1,500 Danish supermarkets equipped, and utilizes 16 operators, and is open 24 hours a day, 365 days a year. AK-Centralen needed the ability to monitor the cooling alarms from around the country, 24 hours a day, 365 days a year. Each and every time the door to a milk cooler or a freezer does not close properly, an alarm goes off on a computer screen in a control building in southwestern Odense. This type of alarm will go off approximately 140,000 times per year, equating to roughly 400 alarms in a 24-hour period. Should an alarm go off, then there is only a limited amount of time to act before dairy products or frozen pizza must be disposed of, and this type of waste can quickly start to cost a supermarket a great deal of money.
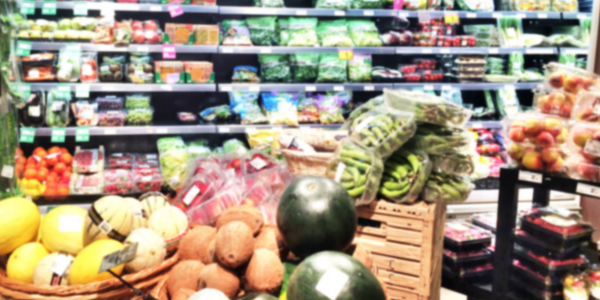
Case Study
Supermarket Energy Savings
The client had previously deployed a one-meter-per-store monitoring program. Given the manner in which energy consumption changes with external temperature, hour of the day, day of week and month of year, a single meter solution lacked the ability to detect the difference between a true problem and a changing store environment. Most importantly, a single meter solution could never identify root cause of energy consumption changes. This approach never reduced the number of truck-rolls or man-hours required to find and resolve issues.