Download PDF
Seismic Qualification of Industrial PC Rack through Simulation
Technology Category
- Automation & Control - Human Machine Interface (HMI)
- Sensors - Vibration Sensors
Applicable Industries
- Aerospace
- Automotive
Applicable Functions
- Product Research & Development
- Quality Assurance
Use Cases
- Experimentation Automation
- Virtual Prototyping & Product Testing
Services
- System Integration
- Testing & Certification
The Challenge
Hi-Tech Outsourcing Services, a leading architectural engineering construction (AEC) and industrial services provider in India, faced a challenge in the design of computer storage racks. These racks, used to mount servers or desktops, must provide structural support for computers and comply with Bellcore testing standards, the most common set of safety, spatial, and environmental design guidelines applied to telecommunications equipment. The challenge was to ensure compliance with these standards while also meeting the increasing demand for quick turnaround during product development. The company needed to develop products using fewer prototype tests to deliver a faster time to market, all while ensuring the racks could withstand seismic tests.
About The Customer
Hi-Tech Outsourcing Services is a leading provider of architectural engineering construction (AEC) and industrial services in India. The company offers a wide range of solutions for various industries including automotive, aerospace, defense, power plant, chemical, construction, and marine. Hi-Tech Outsourcing Services partners with its clients to provide sound and affordable business solutions. The company is committed to delivering high-quality products that meet industry standards and customer expectations, and it continually seeks innovative ways to improve its product development process.
The Solution
To address this challenge, Hi-Tech Outsourcing Services utilized ANSYS® Professional™ NLS technology. Engineers constructed a 3-D model of the industrial PC rack and performed finite element analysis (FEA) to determine the structural integrity and performance characteristics of the rack system under different seismic loading conditions. The simulation allowed the company to quantify system performance characteristics under the influence of seismic inertia loads based on specification and regulatory documents as well as industry standards. This approach enabled the company to ensure that the rack design complied with the Bellcore seismic testing standard, thus shortening the design cycle and ensuring that the rack design would perform according to the specifications.
Operational Impact
Quantitative Benefit
Related Case Studies.
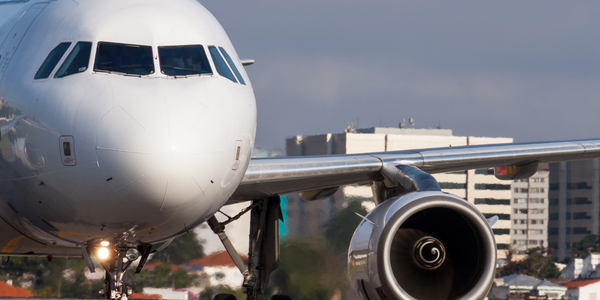
Case Study
Airbus Soars with Wearable Technology
Building an Airbus aircraft involves complex manufacturing processes consisting of thousands of moving parts. Speed and accuracy are critical to business and competitive advantage. Improvements in both would have high impact on Airbus’ bottom line. Airbus wanted to help operators reduce the complexity of assembling cabin seats and decrease the time required to complete this task.
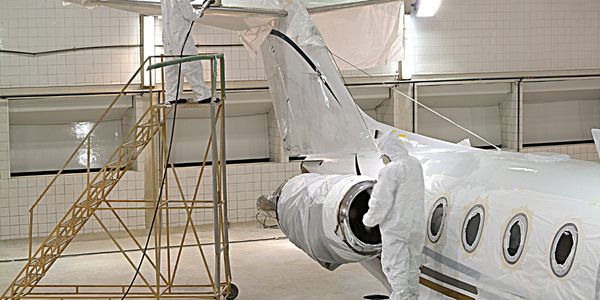
Case Study
Aircraft Predictive Maintenance and Workflow Optimization
First, aircraft manufacturer have trouble monitoring the health of aircraft systems with health prognostics and deliver predictive maintenance insights. Second, aircraft manufacturer wants a solution that can provide an in-context advisory and align job assignments to match technician experience and expertise.
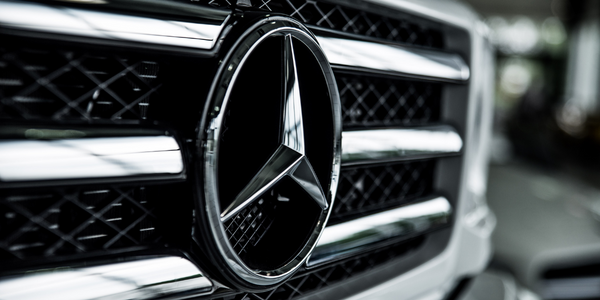
Case Study
Integral Plant Maintenance
Mercedes-Benz and his partner GAZ chose Siemens to be its maintenance partner at a new engine plant in Yaroslavl, Russia. The new plant offers a capacity to manufacture diesel engines for the Russian market, for locally produced Sprinter Classic. In addition to engines for the local market, the Yaroslavl plant will also produce spare parts. Mercedes-Benz Russia and his partner needed a service partner in order to ensure the operation of these lines in a maintenance partnership arrangement. The challenges included coordinating the entire maintenance management operation, in particular inspections, corrective and predictive maintenance activities, and the optimizing spare parts management. Siemens developed a customized maintenance solution that includes all electronic and mechanical maintenance activities (Integral Plant Maintenance).
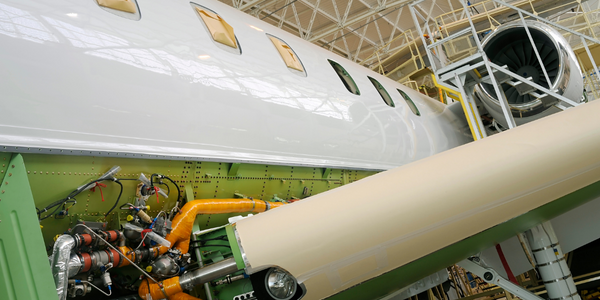
Case Study
Aerospace & Defense Case Study Airbus
For the development of its new wide-body aircraft, Airbus needed to ensure quality and consistency across all internal and external stakeholders. Airbus had many challenges including a very aggressive development schedule and the need to ramp up production quickly to satisfy their delivery commitments. The lack of communication extended design time and introduced errors that drove up costs.