Download PDF
Simulating Lubrication Flow to Predict Traction Oil Distribution Inside a NuVinci® Product
Technology Category
- Infrastructure as a Service (IaaS) - Cloud Computing
- Sensors - Liquid Detection Sensors
Applicable Industries
- Automotive
- Oil & Gas
Applicable Functions
- Maintenance
- Product Research & Development
Use Cases
- Transportation Simulation
- Virtual Reality
Services
- Cloud Planning, Design & Implementation Services
- System Integration
The Challenge
Fallbrook Technologies Inc., a technology development company, was facing a challenge in improving oil flow within their patented NuVinci® transmission system. The transmission system is a crucial part of their product line, which includes urban mobility vehicles, cars and trucks, industrial equipment, and more. The oil flow within the system directly affects the transmission’s efficiency, durability, power, capacity, and cost. However, physically evaluating the design of such a complex transmission system was practically unfeasible. The company needed a cost-effective, efficient, and robust method to provide internal lubrication and predict the effectiveness of a design scenario. They also required an effective solver/software to guide the design process in the innovation process.
About The Customer
Fallbrook Technologies Inc. is a technology development company based in Cedar Park, Texas. The company’s core technology is the patented NuVinci® transmission, a continuously variable planetary (CVP) technology. This technology enables performance and efficiency improvements for machines that use an engine, pump, motor, or geared transmission system. Their product range includes urban mobility vehicles, cars and trucks, industrial equipment, and more. Fallbrook’s unique collective development model and community approach to leverage NuVinci technology helps accelerate product development, resulting in improved energy management, higher performance, more effective, reliable controls and sustainable solutions. Their initial commercial product, a continuously variable transmission (CVT) for bicycles, now includes a rider-needs-based portfolio comprised of five group sets.
The Solution
Fallbrook turned to Altair for a solution. Altair provided an integrated solution that included advanced GPU hardware, high-performance computing (HPC), and the Altair nanoFluidX™ software. The nanoFluidX software, an advanced CFD solver, was used to simulate lubrication flow inside of a NuVinci product. It predicts the flow in complex geometries with complex motion, such as oiling in powertrain systems with rotating gears and shafts, using the smoothed-particle hydrodynamics (SPH) method. The model for simulation was generated with process-oriented finite element modeling software, Altair Simlab™. This included meshing of the system, material and property assignment, motion definition for all internal parts, and particle generation for the SPH mesh to represent the oil. Altair’s HPC cloud computing solution helped alleviate the computational expense of such a large-scale model, without the need for Fallbrook to deal with maintenance of the cloud computing system and associated hardware.
Operational Impact
Quantitative Benefit
Related Case Studies.
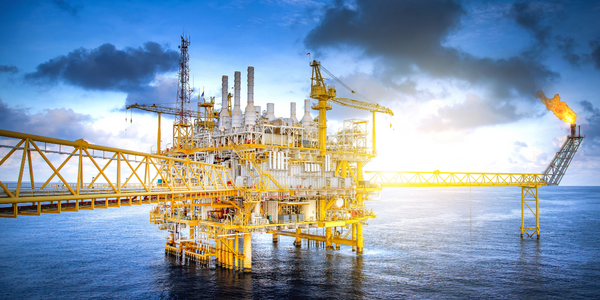
Case Study
Taking Oil and Gas Exploration to the Next Level
DownUnder GeoSolutions (DUG) wanted to increase computing performance by 5 to 10 times to improve seismic processing. The solution must build on current architecture software investments without sacrificing existing software and scale computing without scaling IT infrastructure costs.
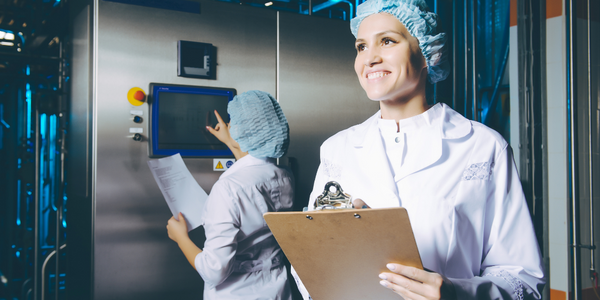
Case Study
Remote Wellhead Monitoring
Each wellhead was equipped with various sensors and meters that needed to be monitored and controlled from a central HMI, often miles away from the assets in the field. Redundant solar and wind generators were installed at each wellhead to support the electrical needs of the pumpstations, temperature meters, cameras, and cellular modules. In addition to asset management and remote control capabilities, data logging for remote surveillance and alarm notifications was a key demand from the customer. Terra Ferma’s solution needed to be power efficient, reliable, and capable of supporting high-bandwidth data-feeds. They needed a multi-link cellular connection to a central server that sustained reliable and redundant monitoring and control of flow meters, temperature sensors, power supply, and event-logging; including video and image files. This open-standard network needed to interface with the existing SCADA and proprietary network management software.
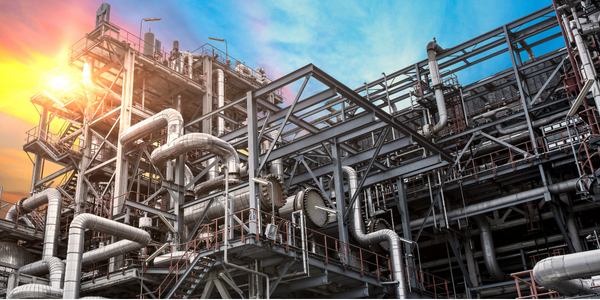
Case Study
Refinery Saves Over $700,000 with Smart Wireless
One of the largest petroleum refineries in the world is equipped to refine various types of crude oil and manufacture various grades of fuel from motor gasoline to Aviation Turbine Fuel. Due to wear and tear, eight hydrogen valves in each refinery were leaking, and each cost $1800 per ton of hydrogen vented. The plant also had leakage on nearly 30 flare control hydrocarbon valves. The refinery wanted a continuous, online monitoring system that could catch leaks early, minimize hydrogen and hydrocarbon production losses, and improve safety for maintenance.
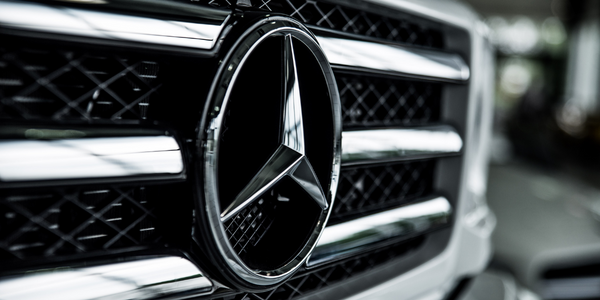
Case Study
Integral Plant Maintenance
Mercedes-Benz and his partner GAZ chose Siemens to be its maintenance partner at a new engine plant in Yaroslavl, Russia. The new plant offers a capacity to manufacture diesel engines for the Russian market, for locally produced Sprinter Classic. In addition to engines for the local market, the Yaroslavl plant will also produce spare parts. Mercedes-Benz Russia and his partner needed a service partner in order to ensure the operation of these lines in a maintenance partnership arrangement. The challenges included coordinating the entire maintenance management operation, in particular inspections, corrective and predictive maintenance activities, and the optimizing spare parts management. Siemens developed a customized maintenance solution that includes all electronic and mechanical maintenance activities (Integral Plant Maintenance).