Download PDF
State-of-the-art SPC System Drives Financial Results
Technology Category
- Functional Applications - Enterprise Resource Planning Systems (ERP)
- Analytics & Modeling - Real Time Analytics
Applicable Industries
- Food & Beverage
Applicable Functions
- Quality Assurance
- Process Manufacturing
Use Cases
- Predictive Maintenance
- Process Control & Optimization
- Remote Asset Management
Services
- System Integration
- Training
The Challenge
In one facility, the company produces more than 435,000 pounds of finished product every day on 22 packaging lines. While the plant is a sparkling clean state-of-the-art facility, the methods they used to control their processes haven’t always been as sophisticated. As recently as two years ago, the SPC system used for weight control was a paper-based X-Bar and R chart. With clipboard and pencil in hand, quality technicians would measure the package weights of small samples periodically from each package line. They would then compute the average weight of the sample and the range and record the information, along with some process data, on a standard form. The information was then submitted to a quality analyst at the end of each shift. The next morning, the analyst reviewed the data for missing information or errors, corrected any mistakes, and then passed it along to a key-punch operator to be keyed into a computer-based SPC package. Two days after the process data was collected, X-Bar and R charts were printed out along with Process Capability information for review by quality engineers and production managers. With only this rear view mirror perspective, managers and engineers were caught in a daily routine of trying to understand what happened at least two days before. And if process changes were not detected when they happened, product holds and costly sorting and repackaging would result. The need for timely information pointed to the need for a technology improvement, but the clean room environment at the company’s plants creates a unique challenge for technology solutions. Any hardware installed on the manufacturing floor has to tolerate hose-downs with a disinfecting solution. Traditional technology solutions – hardened computers or putting computers in sealed enclosures – were prohibitively expensive and never made it to the shop floor. That changed with the advent of low-cost wireless networks and portable handheld devices.
About The Customer
A leading producer of high-quality food products has used Statistical Process Control (SPC) to monitor package weights for more than 25 years. The company operates a state-of-the-art facility that produces more than 435,000 pounds of finished product every day on 22 packaging lines. Despite their advanced production capabilities, the methods they used to control their processes were not always sophisticated. The company faced challenges in maintaining timely and accurate process control data, which led to inefficiencies and potential product holds. The clean room environment at their plants also posed unique challenges for implementing new technology solutions. The company sought to improve their SPC system to gain financial benefits and enhance their process control capabilities.
The Solution
The company decided to implement a new SPC system using Personal Digital Assistants (PDA) and Hertzler Systems’ GainSeeker Suite. The PDA-based system allowed quality technicians to access product and process documentation, record audit findings, and perform package weight SPC directly from the shop floor. This eliminated the need for paper-based records and reduced errors caused by redundant keying of process measures. The GainSeeker Suite enabled real-time data collection and analysis, providing immediate feedback to operators and management. The system was deployed on a central server, simplifying deployment, support, data backup, and software updates. It also integrated with the company's ERP system for giveaway reporting, providing timely and accurate business metrics. The project team found that GainSeeker could do even more than expected, including customizable alarms for out-of-control conditions and real-time reporting of key performance metrics. The system's ease of use and flexibility made it suitable for a wide range of applications across multiple plants.
Operational Impact
Quantitative Benefit
Related Case Studies.
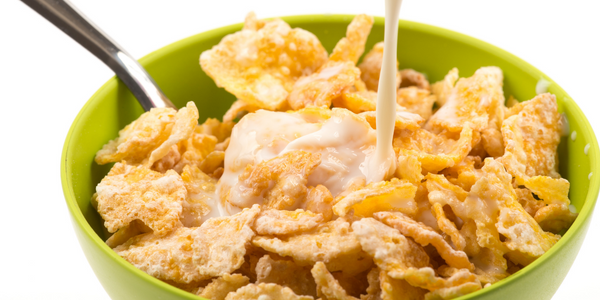
Case Study
The Kellogg Company
Kellogg keeps a close eye on its trade spend, analyzing large volumes of data and running complex simulations to predict which promotional activities will be the most effective. Kellogg needed to decrease the trade spend but its traditional relational database on premises could not keep up with the pace of demand.
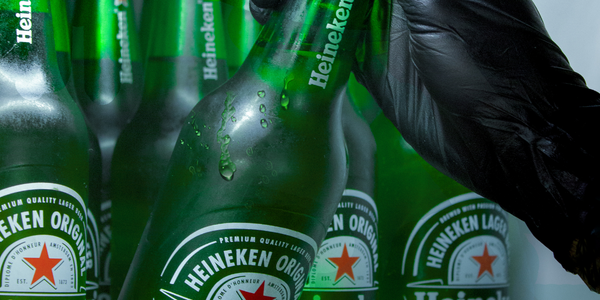
Case Study
HEINEKEN Uses the Cloud to Reach 10.5 Million Consumers
For 2012 campaign, the Bond promotion, it planned to launch the campaign at the same time everywhere on the planet. That created unprecedented challenges for HEINEKEN—nowhere more so than in its technology operation. The primary digital content for the campaign was a 100-megabyte movie that had to play flawlessly for millions of viewers worldwide. After all, Bond never fails. No one was going to tolerate a technology failure that might bruise his brand.Previously, HEINEKEN had supported digital media at its outsourced datacenter. But that datacenter lacked the computing resources HEINEKEN needed, and building them—especially to support peak traffic that would total millions of simultaneous hits—would have been both time-consuming and expensive. Nor would it have provided the geographic reach that HEINEKEN needed to minimize latency worldwide.
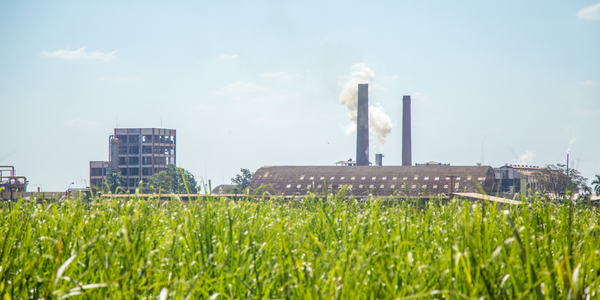
Case Study
Energy Management System at Sugar Industry
The company wanted to use the information from the system to claim under the renewable energy certificate scheme. The benefit to the company under the renewable energy certificates is Rs 75 million a year. To enable the above, an end-to-end solution for load monitoring, consumption monitoring, online data monitoring, automatic meter data acquisition which can be exported to SAP and other applications is required.
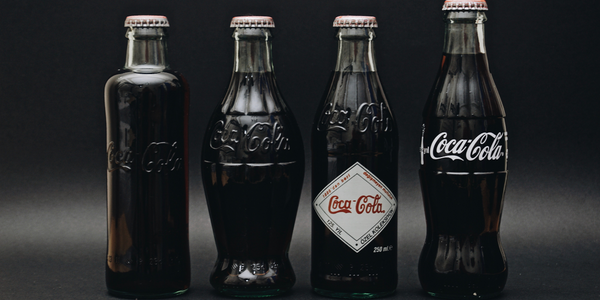
Case Study
Coca Cola Swaziland Conco Case Study
Coco Cola Swaziland, South Africa would like to find a solution that would enable the following results: - Reduce energy consumption by 20% in one year. - Formulate a series of strategic initiatives that would enlist the commitment of corporate management and create employee awareness while helping meet departmental targets and investing in tools that assist with energy management. - Formulate a series of tactical initiatives that would optimize energy usage on the shop floor. These would include charging forklifts and running cold rooms only during off-peak periods, running the dust extractors only during working hours and basing lights and air-conditioning on someone’s presence. - Increase visibility into the factory and other processes. - Enable limited, non-intrusive control functions for certain processes.
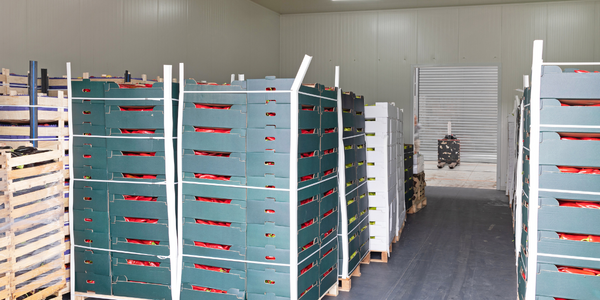
Case Study
Temperature Monitoring for Restaurant Food Storage
When it came to implementing a solution, Mr. Nesbitt had an idea of what functionality that he wanted. Although not mandated by Health Canada, Mr. Nesbitt wanted to ensure quality control issues met the highest possible standards as part of his commitment to top-of-class food services. This wish list included an easy-to use temperature-monitoring system that could provide a visible display of the temperatures of all of his refrigerators and freezers, including historical information so that he could review the performance of his equipment. It also had to provide alert notification (but email alerts and SMS text message alerts) to alert key staff in the event that a cooling system was exceeding pre-set warning limits.
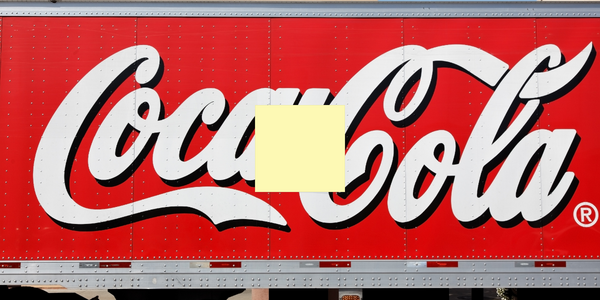
Case Study
Coca-Cola Refreshments, U.S.
Coca-Cola Refreshments owns and manages Coca-Cola branded refrigerators in retail establishments. Legacy systems were used to locate equipment information by logging onto multiple servers which took up to 8 hours to update information on 30-40 units. The company had no overall visibility into equipment status or maintenance history.