Download PDF
Strategic IT planning leads to million-dollar savings
Technology Category
- Application Infrastructure & Middleware - Data Exchange & Integration
Applicable Industries
- Oil & Gas
Applicable Functions
- Business Operation
Use Cases
- Infrastructure Inspection
- Asset Lifecycle Management
Services
- System Integration
The Challenge
The global player in the oil and gas industry was spending over $1 billion annually on technology to organize, store, and share information that drives the business. However, the enterprise IT infrastructure had become complicated due to piecemeal construction throughout the company’s business units and a tangled web of legacy systems from mergers and acquisitions dating back to the early 1980s. The company had an estimated 8,000 applications costing over $600 million to run annually. Despite the significant annual expenditure on new systems, there was no alignment to a multi-year road map. Application strategies were inconsistent across the business units, and there was no common architecture or strategy.
About The Customer
The customer is a global player in the oil and gas industry. They provide customers with fuel, energy, and petrochemicals. The company has a workforce of over 85,000 employees worldwide and generates annual revenues of over $300 billion. The enterprise portfolio includes upstream and downstream sectors, and exploration and production take place in over 30 countries. The company spends over $1 billion annually on technology to help organize, store, and share the information that drives the business.
The Solution
The company's enterprise architecture team came up with a solution called the Bill of IT, a revolutionary way of optimizing the enterprise’s investment and simplifying the complex legacy of 8,000 applications. The Bill of IT comprises a list of all the IT components in an organization and how they fit together to support the business processes. The team first undertook a rigorous survey of the application landscape, mapping applications to business processes, and classifying applications according to whether they were critical or strategic. Only those fitting both criteria became part of the Bill of IT. The enterprise architects worked with more than 300 people from around the organization to define the future Bill of IT: what the company’s business processes would be and the IT infrastructure needed to support this. Once a Bill of IT was established for each business unit, a road map and spending framework were agreed upon to align spending as closely as possible to the strategic goals.
Operational Impact
Quantitative Benefit
Related Case Studies.
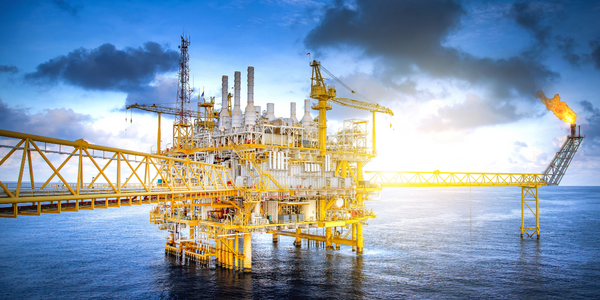
Case Study
Taking Oil and Gas Exploration to the Next Level
DownUnder GeoSolutions (DUG) wanted to increase computing performance by 5 to 10 times to improve seismic processing. The solution must build on current architecture software investments without sacrificing existing software and scale computing without scaling IT infrastructure costs.
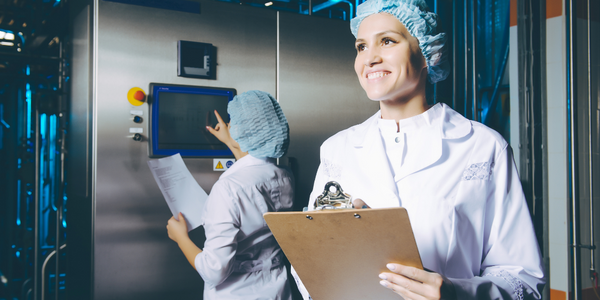
Case Study
Remote Wellhead Monitoring
Each wellhead was equipped with various sensors and meters that needed to be monitored and controlled from a central HMI, often miles away from the assets in the field. Redundant solar and wind generators were installed at each wellhead to support the electrical needs of the pumpstations, temperature meters, cameras, and cellular modules. In addition to asset management and remote control capabilities, data logging for remote surveillance and alarm notifications was a key demand from the customer. Terra Ferma’s solution needed to be power efficient, reliable, and capable of supporting high-bandwidth data-feeds. They needed a multi-link cellular connection to a central server that sustained reliable and redundant monitoring and control of flow meters, temperature sensors, power supply, and event-logging; including video and image files. This open-standard network needed to interface with the existing SCADA and proprietary network management software.
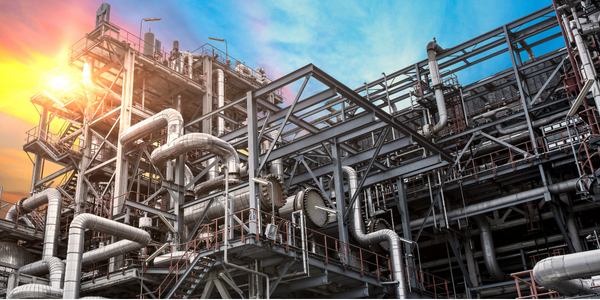
Case Study
Refinery Saves Over $700,000 with Smart Wireless
One of the largest petroleum refineries in the world is equipped to refine various types of crude oil and manufacture various grades of fuel from motor gasoline to Aviation Turbine Fuel. Due to wear and tear, eight hydrogen valves in each refinery were leaking, and each cost $1800 per ton of hydrogen vented. The plant also had leakage on nearly 30 flare control hydrocarbon valves. The refinery wanted a continuous, online monitoring system that could catch leaks early, minimize hydrogen and hydrocarbon production losses, and improve safety for maintenance.