Download PDF
Strong Leaders, Strong Results: Our Path to Data Analysis, Literacy, and Governance
Technology Category
- Analytics & Modeling - Big Data Analytics
- Analytics & Modeling - Data-as-a-Service
Applicable Industries
- Oil & Gas
Applicable Functions
- Discrete Manufacturing
- Business Operation
Use Cases
- Predictive Maintenance
- Manufacturing System Automation
Services
- Data Science Services
- System Integration
The Challenge
Gazprom Neft, one of the top three oil-producing companies in Russia, was facing challenges in making data-based decisions due to the lack of a robust Business Intelligence (BI) unit. The company was already a year into their journey with Qlik, a data analytics platform, when the BI Department Head joined in 2013. The task was to further develop the internal Qlik-based processes. However, the allocation of resources was a major challenge, especially server resources. The company was also not always on schedule in the purchasing of new equipment. Change management was another challenge, particularly overcoming internal resistance without clear signaling from company leadership.
About The Customer
Gazprom Neft Group, celebrating its 25th anniversary in 2020, is one of the top three oil-producing companies in Russia. The company is involved in every stage of oil-based products, from hydrocarbon exploration and the production of high-quality oil and gas to the retail sale of a wide variety of petroleum products. Gazprom Neft has operations in many areas of the world, including South America and Africa. With more than 70 subsidiaries related to production, refining, and direct sales, it is one of the largest energy operations in the world. In 2019, the company's net profit was over $5 billion USD and it currently employs over 50,000 people.
The Solution
Despite the challenges, the company had full support from top management, especially the CFO, who was interested in the potential benefits of a robust BI unit. This support led to a revolution of sorts, leading to a transformation into a data-driven culture. The company took its time to develop expertise and structures for data analysis, data literacy, and data governance. As the company's data analysis competence grew, so did the team. By the end of 2014, the BI office had one developer and two analysts, all of whom were required to know structured query language (SQL). A year later, mathematical statistics and languages like Python were added to the required skills. As the functionality developed, so too did the various categories of staff expertise. The company also worked closely with a number of universities, offering internships to students from a variety of backgrounds, many of whom eventually joined the organization as full-time employees.
Operational Impact
Quantitative Benefit
Related Case Studies.
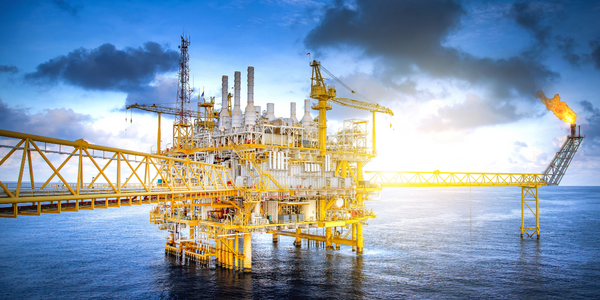
Case Study
Taking Oil and Gas Exploration to the Next Level
DownUnder GeoSolutions (DUG) wanted to increase computing performance by 5 to 10 times to improve seismic processing. The solution must build on current architecture software investments without sacrificing existing software and scale computing without scaling IT infrastructure costs.
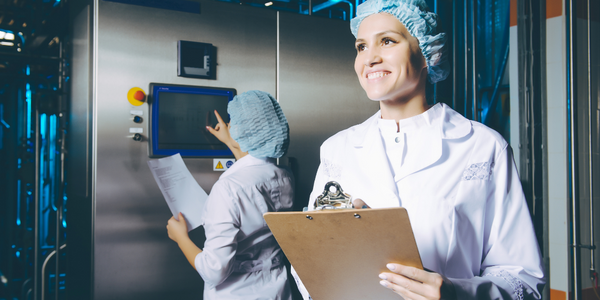
Case Study
Remote Wellhead Monitoring
Each wellhead was equipped with various sensors and meters that needed to be monitored and controlled from a central HMI, often miles away from the assets in the field. Redundant solar and wind generators were installed at each wellhead to support the electrical needs of the pumpstations, temperature meters, cameras, and cellular modules. In addition to asset management and remote control capabilities, data logging for remote surveillance and alarm notifications was a key demand from the customer. Terra Ferma’s solution needed to be power efficient, reliable, and capable of supporting high-bandwidth data-feeds. They needed a multi-link cellular connection to a central server that sustained reliable and redundant monitoring and control of flow meters, temperature sensors, power supply, and event-logging; including video and image files. This open-standard network needed to interface with the existing SCADA and proprietary network management software.
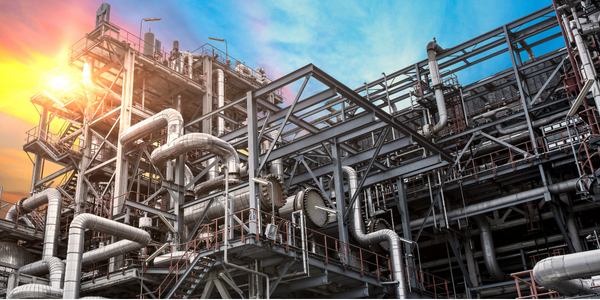
Case Study
Refinery Saves Over $700,000 with Smart Wireless
One of the largest petroleum refineries in the world is equipped to refine various types of crude oil and manufacture various grades of fuel from motor gasoline to Aviation Turbine Fuel. Due to wear and tear, eight hydrogen valves in each refinery were leaking, and each cost $1800 per ton of hydrogen vented. The plant also had leakage on nearly 30 flare control hydrocarbon valves. The refinery wanted a continuous, online monitoring system that could catch leaks early, minimize hydrogen and hydrocarbon production losses, and improve safety for maintenance.