Download PDF
Sujan CooperStandard's Success in Achieving Lightweight and Performance Targets with Altair
Technology Category
- Sensors - Haptic Sensors
- Sensors - Vibration Sensors
Applicable Industries
- Aerospace
- Automotive
Applicable Functions
- Product Research & Development
- Quality Assurance
Use Cases
- Time Sensitive Networking
- Visual Quality Detection
Services
- Testing & Certification
- Training
The Challenge
Sujan CooperStandard, a leading manufacturer of anti-vibration NVH products for automotive companies, faced significant challenges due to the stringent environmental norms and government policies related to pollution control. The automotive industry's pressure to reduce vehicle weight to minimize pollution and increase efficiency put the company under immense pressure to optimize designs and reduce the weight of products and components. Additionally, the fierce competition among automotive companies to launch new products quickly added to the pressure. Traditional methods of designing, developing, and testing products were no longer sufficient to meet the aggressive deadlines set by automotive companies. Sujan CooperStandard needed state-of-the-art software CAE solutions to reduce new product development time and cost while maintaining the product quality standards set by their clients.
About The Customer
Sujan CooperStandard is a collaboration between the Sujan Group and CooperStandard. The Sujan Group, started in 1977, has served almost every aspect of the automobile and vehicle industry, including automotive four and two wheelers applications, railway, aerospace, agricultural, industrial, earth moving and construction applications, as well as marine, power generation, and defense applications. CooperStandard France is the world’s leading supplier of systems and components for the automotive industry. The collaboration between Sujan and CooperStandard has multiplied the group’s capability to serve the market, bringing together the quality experience of Sujan and the design and engineering knowledge of CooperStandard.
The Solution
Sujan CooperStandard invested in Altair CAE Solutions to meet their challenges. Initially, they used Altair HyperWorks only as a pre-processor, but after understanding the software's capabilities, they started using it extensively for both pre-processing and post-processing. The company now heavily relies on Altair pre-processor HyperMesh and post-processor HyperView for meshing and viewing post-processing results. They plan to use Altair OptiStruct and solidThinking Inspire for weight optimization of their components in the future. They are also keen to evaluate Altair RADIOSS, a robust solver, to check its speed and efficiency to further help them save costs. Using the Altair suite of solutions, Sujan CooperStandard consistently meets their time, cost, and quality targets, getting their products right the first time.
Operational Impact
Quantitative Benefit
Related Case Studies.
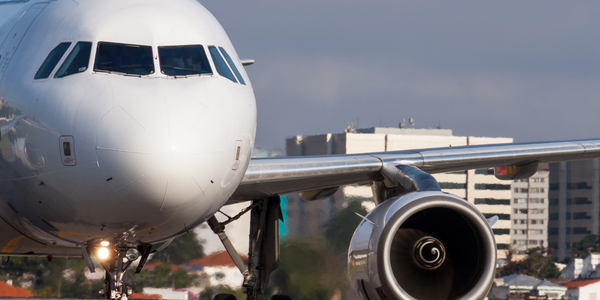
Case Study
Airbus Soars with Wearable Technology
Building an Airbus aircraft involves complex manufacturing processes consisting of thousands of moving parts. Speed and accuracy are critical to business and competitive advantage. Improvements in both would have high impact on Airbus’ bottom line. Airbus wanted to help operators reduce the complexity of assembling cabin seats and decrease the time required to complete this task.
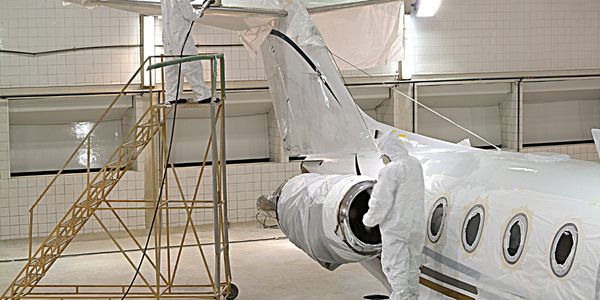
Case Study
Aircraft Predictive Maintenance and Workflow Optimization
First, aircraft manufacturer have trouble monitoring the health of aircraft systems with health prognostics and deliver predictive maintenance insights. Second, aircraft manufacturer wants a solution that can provide an in-context advisory and align job assignments to match technician experience and expertise.
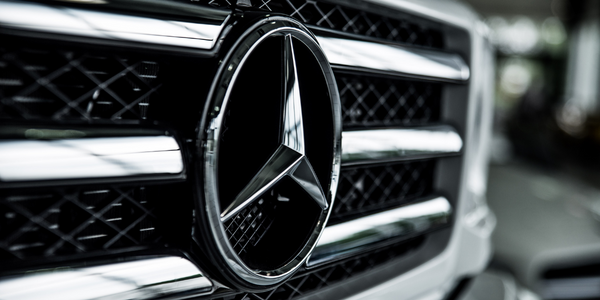
Case Study
Integral Plant Maintenance
Mercedes-Benz and his partner GAZ chose Siemens to be its maintenance partner at a new engine plant in Yaroslavl, Russia. The new plant offers a capacity to manufacture diesel engines for the Russian market, for locally produced Sprinter Classic. In addition to engines for the local market, the Yaroslavl plant will also produce spare parts. Mercedes-Benz Russia and his partner needed a service partner in order to ensure the operation of these lines in a maintenance partnership arrangement. The challenges included coordinating the entire maintenance management operation, in particular inspections, corrective and predictive maintenance activities, and the optimizing spare parts management. Siemens developed a customized maintenance solution that includes all electronic and mechanical maintenance activities (Integral Plant Maintenance).
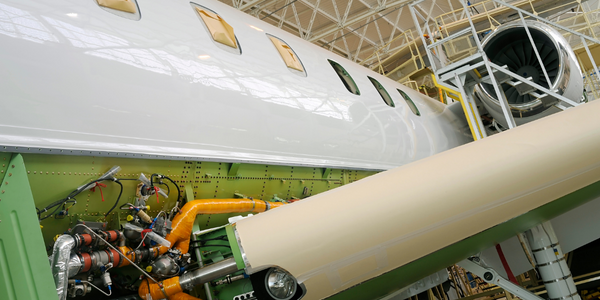
Case Study
Aerospace & Defense Case Study Airbus
For the development of its new wide-body aircraft, Airbus needed to ensure quality and consistency across all internal and external stakeholders. Airbus had many challenges including a very aggressive development schedule and the need to ramp up production quickly to satisfy their delivery commitments. The lack of communication extended design time and introduced errors that drove up costs.