Download PDF
ThyssenKrupp Elevator Americas Reduces Product Costs with aPriori
Technology Category
- Analytics & Modeling - Predictive Analytics
- Functional Applications - Product Lifecycle Management Systems (PLM)
Applicable Functions
- Procurement
- Product Research & Development
Use Cases
- Manufacturing System Automation
- Predictive Maintenance
Services
- Software Design & Engineering Services
- System Integration
The Challenge
ThyssenKrupp Elevator faced challenges in cost management, particularly at the design stage. The process was manual, time-consuming, and inconsistent, leading to delays and inefficiencies. Design engineers focused on product quality, with cost considerations being secondary. The company needed a solution to integrate cost management into the design process without slowing down product development.
About The Customer
ThyssenKrupp Elevator is a leading global elevator company, part of the ThyssenKrupp Group based in Essen, Germany. The company offers a wide range of products including passenger and freight elevators, escalators, and moving walks. With annual sales of 42.6 billion euros and over 177,000 employees globally, ThyssenKrupp Elevator Americas is the largest producer of elevators in the Americas, employing over 13,500 people and generating sales of more than $2.7 billion. The company operates extensively in the United States, Canada, Central, and South America, with significant manufacturing operations in Tennessee.
The Solution
ThyssenKrupp Elevator implemented aPriori, a product cost-management software, to address its cost management challenges. A cross-functional team evaluated the software over 10 weeks, focusing on its ability to provide real-time product-cost information. The team found that aPriori could identify cost savings even in mature product parts and was easy to use for both new and experienced engineers. The software allowed for instant and precise cost assessments from CAD models, enabling more informed design decisions. aPriori was also used by the manufacturing and procurement teams to optimize processes and negotiate better supplier terms.
Operational Impact
Quantitative Benefit
Related Case Studies.
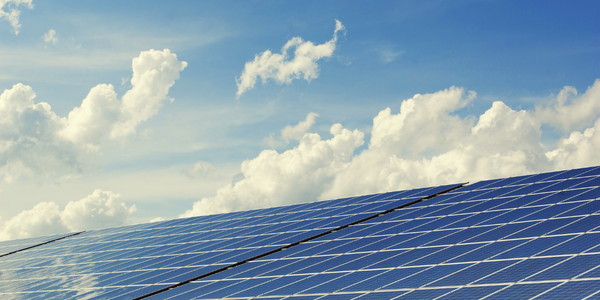
Case Study
Remote Monitoring & Predictive Maintenance App for a Solar Energy System
The maintenance & tracking of various modules was an overhead for the customer due to the huge labor costs involved. Being an advanced solar solutions provider, they wanted to ensure early detection of issues and provide the best-in-class customer experience. Hence they wanted to automate the whole process.
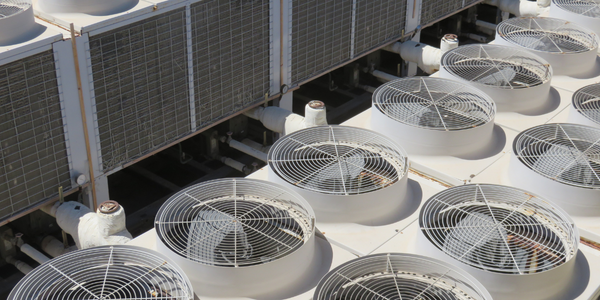
Case Study
Predictive Maintenance for Industrial Chillers
For global leaders in the industrial chiller manufacturing, reliability of the entire production process is of the utmost importance. Chillers are refrigeration systems that produce ice water to provide cooling for a process or industrial application. One of those leaders sought a way to respond to asset performance issues, even before they occur. The intelligence to guarantee maximum reliability of cooling devices is embedded (pre-alarming). A pre-alarming phase means that the cooling device still works, but symptoms may appear, telling manufacturers that a failure is likely to occur in the near future. Chillers who are not internet connected at that moment, provide little insight in this pre-alarming phase.
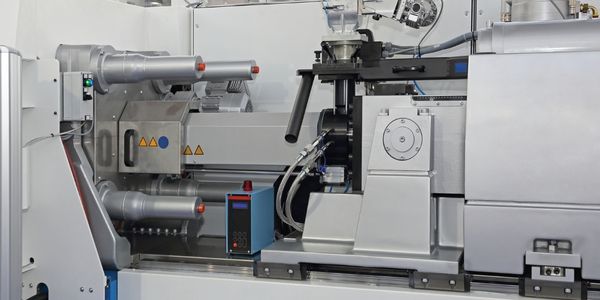
Case Study
Plastic Spoons Case study: Injection Moulding
In order to meet customer expectations by supplying a wide variety of packaging units, from 36 to 1000 spoons per package, a new production and packaging line needed to be built. DeSter wanted to achieve higher production capacity, lower cycle time and a high degree of operator friendliness with this new production line.
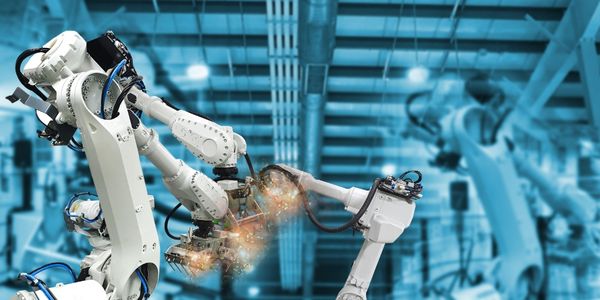
Case Study
Robot Saves Money and Time for US Custom Molding Company
Injection Technology (Itech) is a custom molder for a variety of clients that require precision plastic parts for such products as electric meter covers, dental appliance cases and spools. With 95 employees operating 23 molding machines in a 30,000 square foot plant, Itech wanted to reduce man hours and increase efficiency.
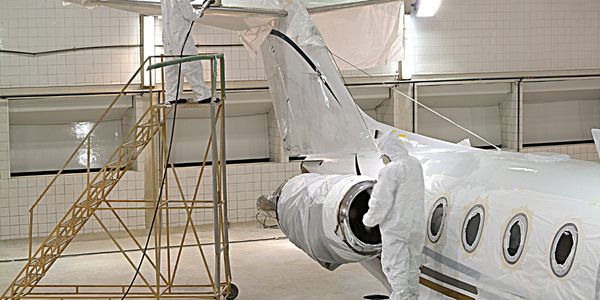
Case Study
Aircraft Predictive Maintenance and Workflow Optimization
First, aircraft manufacturer have trouble monitoring the health of aircraft systems with health prognostics and deliver predictive maintenance insights. Second, aircraft manufacturer wants a solution that can provide an in-context advisory and align job assignments to match technician experience and expertise.
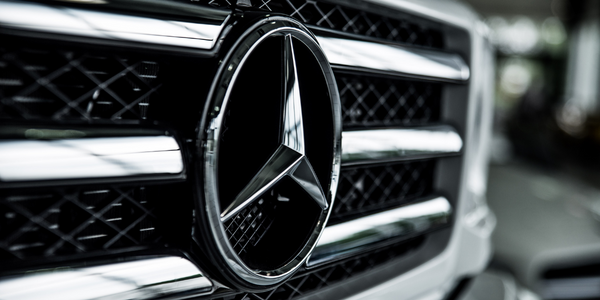
Case Study
Integral Plant Maintenance
Mercedes-Benz and his partner GAZ chose Siemens to be its maintenance partner at a new engine plant in Yaroslavl, Russia. The new plant offers a capacity to manufacture diesel engines for the Russian market, for locally produced Sprinter Classic. In addition to engines for the local market, the Yaroslavl plant will also produce spare parts. Mercedes-Benz Russia and his partner needed a service partner in order to ensure the operation of these lines in a maintenance partnership arrangement. The challenges included coordinating the entire maintenance management operation, in particular inspections, corrective and predictive maintenance activities, and the optimizing spare parts management. Siemens developed a customized maintenance solution that includes all electronic and mechanical maintenance activities (Integral Plant Maintenance).