Download PDF
Ultra Petroleum: Fueling greater internal efficiency and pain-free financial reporting with automation
Technology Category
- Analytics & Modeling - Real Time Analytics
Applicable Industries
- Oil & Gas
Use Cases
- Regulatory Compliance Monitoring
Services
- Data Science Services
The Challenge
Ultra Petroleum Corp., an independent oil and gas company, was facing the challenge of meeting demanding financial reporting requirements without adding to its headcount. The U.S. Securities and Exchange Commission (SEC) requires public companies like Ultra to file financial statements, including annual 10-K and quarterly 10-Q financial reports. These statements must be tagged using eXtensible Business Reporting Language (XBRL), a global standard for exchanging business information. For many companies, the XBRL requirement has more than doubled their SEC reporting workload. Ultra began looking for a solution that would return control of SEC reporting to the people who knew the company’s finances best: its accounting department.
About The Customer
Ultra Petroleum Corp. is an independent oil and gas company engaged in the exploration, acquisition development, production and operation of oil and natural gas properties. The company is headquartered in Houston, Texas, and its primary focus is the development of its natural gas reserves in southwest Wyoming. Recent volatility in the commodities market has led to a dramatic fall in oil and gas prices, which means that businesses in the oil and gas sector are facing tough choices in order to protect their profitability. In these challenging times, oil and gas producers are looking for new internal efficiencies: over the long term, a company that runs a leaner business than its rivals is more likely to gain a competitive advantage.
The Solution
To automate its financial reporting and processes, Ultra chose to deploy IBM® Cognos® Disclosure Management. Today, Ultra uses the solution to assemble its annual 10-K and quarterly 10-Q SEC reports, other financial statements, board reports, news releases and SOX process narratives, leveraging the automated XBRL tagging feature. By basing all reporting on the same source data—the company’s General Ledger—Ultra can be confident that all employees, external auditors and investors are working with the same figures.
Operational Impact
Quantitative Benefit
Related Case Studies.
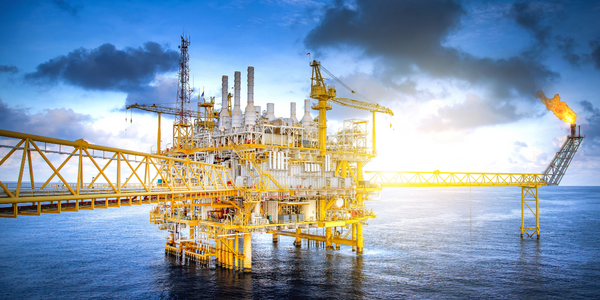
Case Study
Taking Oil and Gas Exploration to the Next Level
DownUnder GeoSolutions (DUG) wanted to increase computing performance by 5 to 10 times to improve seismic processing. The solution must build on current architecture software investments without sacrificing existing software and scale computing without scaling IT infrastructure costs.
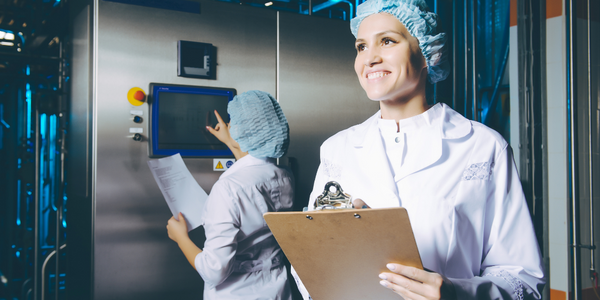
Case Study
Remote Wellhead Monitoring
Each wellhead was equipped with various sensors and meters that needed to be monitored and controlled from a central HMI, often miles away from the assets in the field. Redundant solar and wind generators were installed at each wellhead to support the electrical needs of the pumpstations, temperature meters, cameras, and cellular modules. In addition to asset management and remote control capabilities, data logging for remote surveillance and alarm notifications was a key demand from the customer. Terra Ferma’s solution needed to be power efficient, reliable, and capable of supporting high-bandwidth data-feeds. They needed a multi-link cellular connection to a central server that sustained reliable and redundant monitoring and control of flow meters, temperature sensors, power supply, and event-logging; including video and image files. This open-standard network needed to interface with the existing SCADA and proprietary network management software.
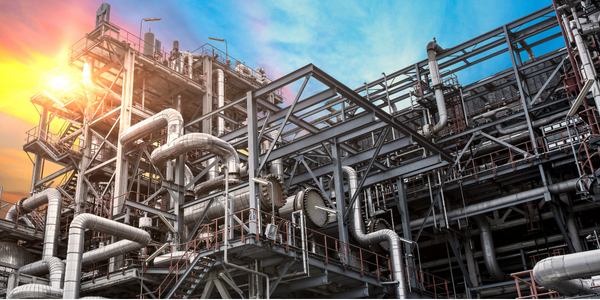
Case Study
Refinery Saves Over $700,000 with Smart Wireless
One of the largest petroleum refineries in the world is equipped to refine various types of crude oil and manufacture various grades of fuel from motor gasoline to Aviation Turbine Fuel. Due to wear and tear, eight hydrogen valves in each refinery were leaking, and each cost $1800 per ton of hydrogen vented. The plant also had leakage on nearly 30 flare control hydrocarbon valves. The refinery wanted a continuous, online monitoring system that could catch leaks early, minimize hydrogen and hydrocarbon production losses, and improve safety for maintenance.