Download PDF
Using Automated Storage to Optimize Costs and Improve Quality
Technology Category
- Functional Applications - Warehouse Management Systems (WMS)
- Automation & Control - Automation & Process Control Systems
- Analytics & Modeling - Predictive Analytics
Applicable Industries
- Food & Beverage
- Consumer Goods
Applicable Functions
- Warehouse & Inventory Management
- Logistics & Transportation
Use Cases
- Warehouse Automation
- Inventory Management
- Predictive Maintenance
Services
- System Integration
- Software Design & Engineering Services
- Training
The Challenge
In 2013, Trinchero Family Estates decided to centralize its bottling and distribution with its production in a new facility that would leverage automation. The facility had to support seamless product movement between production and distribution as well as accommodate products received from co-manufacturers and other TFE bottling sites. The primary challenge was achieving the throughput and speed desired. The goal was to run 3-4 bottling lines while also bringing in product from co-manufacturers and bottling sites in Napa Valley. They needed to move product into storage fast and ship fast. Other challenges included consolidating inventory from two distribution centers into one high-density location and providing visibility and control of product as it moved through bottling and distribution.
About The Customer
Trinchero Family Estates is a worldwide leader in the wine industry, with more than 45 acclaimed wine and spirits brands and a global presence in nearly 50 countries. The family-owned business has been passed through three generations of Trincheros since it was founded in 1947, expanding steadily as it grew sales and added brands. The Sutter Home brand alone has grown into one of the top wine brands in the U.S. with sales of more than 10 million cases annually. However, while the company was growing its portfolio and reach, inefficiencies crept into the supply chain. Bottling and distribution were spread across two facilities in Napa Valley, physically removed from the company’s largest wine production facility in Lodi, California. That required bulk wine to be shipped across the Napa Valley to be bottled and distributed from various facilities that relied upon classic manual storage and distribution operations.
The Solution
Trinchero engaged with Swisslog Warehouse and Distribution Solutions to develop an automated distribution system that could be integrated with bottling in a new facility in Lodi, California. They chose the Swisslog PowerStore system, a robotic storage and retrieval system designed for deep lane storage of palletized loads. The solution featured a four-module Swisslog PowerStore system and more than 3,500 feet of Swisslog ProMove conveyors connecting bottling and receiving with the PowerStore system. The PowerStore system provides high-density storage in nine vertical layers and intelligently manages inventory to optimize compaction and support first-in first-out management. The system can store more than 72,000 pallets—over 4 million cases—in just 190,000 square feet, with throughputs of up to 249 pallets per hour. Integration of Trinchero’s SAP system with the new Swisslog WMS allows for continuous communication, maintaining visibility and control over products as they transition from production and receiving into the automated storage system and through shipping.
Operational Impact
Quantitative Benefit
Related Case Studies.
.png)
Case Study
Improving Vending Machine Profitability with the Internet of Things (IoT)
The vending industry is undergoing a sea change, taking advantage of new technologies to go beyond just delivering snacks to creating a new retail location. Intelligent vending machines can be found in many public locations as well as company facilities, selling different types of goods and services, including even computer accessories, gold bars, tickets, and office supplies. With increasing sophistication, they may also provide time- and location-based data pertaining to sales, inventory, and customer preferences. But at the end of the day, vending machine operators know greater profitability is driven by higher sales and lower operating costs.
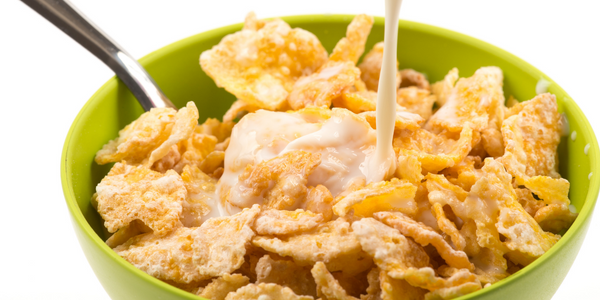
Case Study
The Kellogg Company
Kellogg keeps a close eye on its trade spend, analyzing large volumes of data and running complex simulations to predict which promotional activities will be the most effective. Kellogg needed to decrease the trade spend but its traditional relational database on premises could not keep up with the pace of demand.
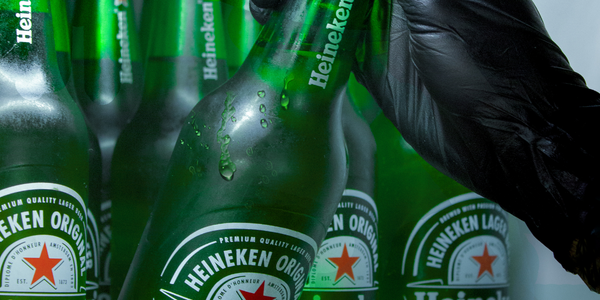
Case Study
HEINEKEN Uses the Cloud to Reach 10.5 Million Consumers
For 2012 campaign, the Bond promotion, it planned to launch the campaign at the same time everywhere on the planet. That created unprecedented challenges for HEINEKEN—nowhere more so than in its technology operation. The primary digital content for the campaign was a 100-megabyte movie that had to play flawlessly for millions of viewers worldwide. After all, Bond never fails. No one was going to tolerate a technology failure that might bruise his brand.Previously, HEINEKEN had supported digital media at its outsourced datacenter. But that datacenter lacked the computing resources HEINEKEN needed, and building them—especially to support peak traffic that would total millions of simultaneous hits—would have been both time-consuming and expensive. Nor would it have provided the geographic reach that HEINEKEN needed to minimize latency worldwide.
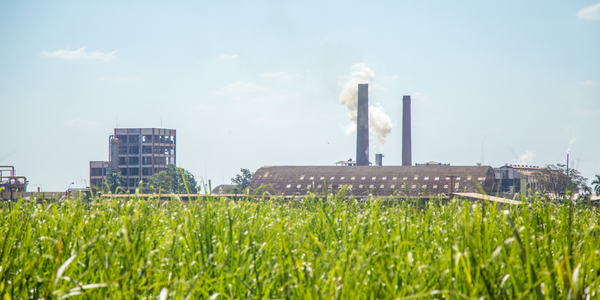
Case Study
Energy Management System at Sugar Industry
The company wanted to use the information from the system to claim under the renewable energy certificate scheme. The benefit to the company under the renewable energy certificates is Rs 75 million a year. To enable the above, an end-to-end solution for load monitoring, consumption monitoring, online data monitoring, automatic meter data acquisition which can be exported to SAP and other applications is required.
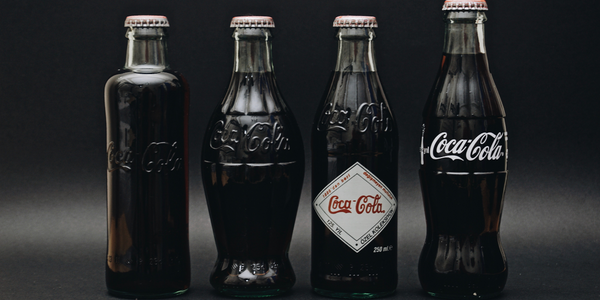
Case Study
Coca Cola Swaziland Conco Case Study
Coco Cola Swaziland, South Africa would like to find a solution that would enable the following results: - Reduce energy consumption by 20% in one year. - Formulate a series of strategic initiatives that would enlist the commitment of corporate management and create employee awareness while helping meet departmental targets and investing in tools that assist with energy management. - Formulate a series of tactical initiatives that would optimize energy usage on the shop floor. These would include charging forklifts and running cold rooms only during off-peak periods, running the dust extractors only during working hours and basing lights and air-conditioning on someone’s presence. - Increase visibility into the factory and other processes. - Enable limited, non-intrusive control functions for certain processes.