Download PDF
Vida Health's Transformation: Personalized Healthcare through Modern Data Stack
Technology Category
- Analytics & Modeling - Big Data Analytics
- Functional Applications - Enterprise Resource Planning Systems (ERP)
Applicable Industries
- Healthcare & Hospitals
- Oil & Gas
Applicable Functions
- Product Research & Development
- Quality Assurance
Use Cases
- Experimentation Automation
- Leasing Finance Automation
Services
- Cloud Planning, Design & Implementation Services
- Testing & Certification
The Challenge
Vida Health, a digital health company, was facing challenges with its data infrastructure. The company collects data on customers' medical history, past insurance claims, lab test results, and log data from health-tech devices to provide personalized virtual care. However, their custom-built solution using Python scripts and cron jobs to load and transform data in BigQuery was not scalable and often failed when data volume spiked. The pipeline was poorly documented and understood by only a few people on the data team, leading to reporting downtime of 2-3 days when issues arose. The company had recently consolidated its data engineering, data science, and data analytics functions into one team, aiming to improve collaboration. However, the existing data infrastructure was not reliable or accessible enough to best serve their customers and meet their goal of onboarding more than ten new clients in less than six months.
About The Customer
Vida Health is a San Francisco-based digital health company founded in 2014. The company provides personalized virtual care to individuals with chronic conditions such as diabetes, obesity, and depression through employer-sponsored plans. To tailor support and resources to individual needs, Vida Health collects data on the customer's medical history, past insurance claims, lab test results, and log data from health-tech devices such as fitness trackers and digital scales. The data enables Vida Health to monitor user progress, adjust treatment plans as needed, and give users visibility into results via the Vida Health mobile app. The company has a team size of 400 and uses a data stack comprising dbt Cloud, Fivetran Enterprise, Google Cloud, BigQuery, and Looker.
The Solution
Vida Health implemented Fivetran and dbt Cloud to transform their data infrastructure. Fivetran was used to centralize data from all their SaaS applications and proprietary Protected Health Information (PHI) from multiple sources into one source-of-truth warehouse. This provided built-in automation and security, especially crucial when handling health data. The company now uses Fivetran to centralize data from 148 different connectors into one BigQuery. Once the data was loaded into BigQuery with Fivetran, the team used dbt Cloud to refactor old pipeline code into modular SQL queries that could be more easily read, reused, and maintained. dbt Cloud made the data transformation process accessible to Vida Health employees across clinical research, product, and data teams, enabling them to share knowledge, add more precision to their data insights and product, and move faster. The company now uses built-in features from dbt Cloud and Fivetran to prevent issues that could create pipeline downtime and ensure a quick recovery when incidents occur.
Operational Impact
Quantitative Benefit
Related Case Studies.
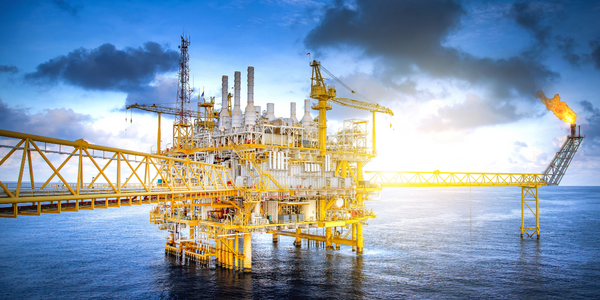
Case Study
Taking Oil and Gas Exploration to the Next Level
DownUnder GeoSolutions (DUG) wanted to increase computing performance by 5 to 10 times to improve seismic processing. The solution must build on current architecture software investments without sacrificing existing software and scale computing without scaling IT infrastructure costs.
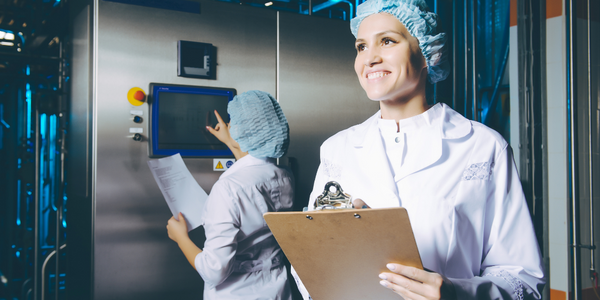
Case Study
Remote Wellhead Monitoring
Each wellhead was equipped with various sensors and meters that needed to be monitored and controlled from a central HMI, often miles away from the assets in the field. Redundant solar and wind generators were installed at each wellhead to support the electrical needs of the pumpstations, temperature meters, cameras, and cellular modules. In addition to asset management and remote control capabilities, data logging for remote surveillance and alarm notifications was a key demand from the customer. Terra Ferma’s solution needed to be power efficient, reliable, and capable of supporting high-bandwidth data-feeds. They needed a multi-link cellular connection to a central server that sustained reliable and redundant monitoring and control of flow meters, temperature sensors, power supply, and event-logging; including video and image files. This open-standard network needed to interface with the existing SCADA and proprietary network management software.
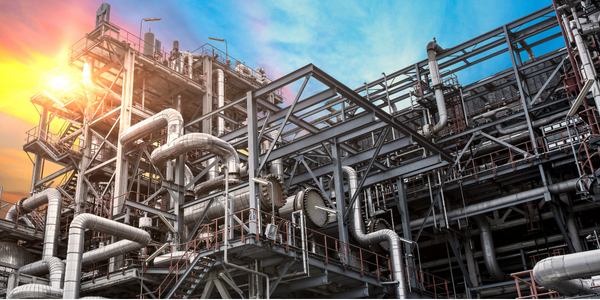
Case Study
Refinery Saves Over $700,000 with Smart Wireless
One of the largest petroleum refineries in the world is equipped to refine various types of crude oil and manufacture various grades of fuel from motor gasoline to Aviation Turbine Fuel. Due to wear and tear, eight hydrogen valves in each refinery were leaking, and each cost $1800 per ton of hydrogen vented. The plant also had leakage on nearly 30 flare control hydrocarbon valves. The refinery wanted a continuous, online monitoring system that could catch leaks early, minimize hydrogen and hydrocarbon production losses, and improve safety for maintenance.
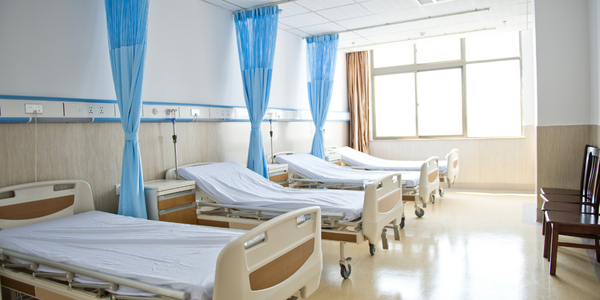
Case Study
Hospital Inventory Management
The hospital supply chain team is responsible for ensuring that the right medical supplies are readily available to clinicians when and where needed, and to do so in the most efficient manner possible. However, many of the systems and processes in use at the cancer center for supply chain management were not best suited to support these goals. Barcoding technology, a commonly used method for inventory management of medical supplies, is labor intensive, time consuming, does not provide real-time visibility into inventory levels and can be prone to error. Consequently, the lack of accurate and real-time visibility into inventory levels across multiple supply rooms in multiple hospital facilities creates additional inefficiency in the system causing over-ordering, hoarding, and wasted supplies. Other sources of waste and cost were also identified as candidates for improvement. Existing systems and processes did not provide adequate security for high-cost inventory within the hospital, which was another driver of cost. A lack of visibility into expiration dates for supplies resulted in supplies being wasted due to past expiry dates. Storage of supplies was also a key consideration given the location of the cancer center’s facilities in a dense urban setting, where space is always at a premium. In order to address the challenges outlined above, the hospital sought a solution that would provide real-time inventory information with high levels of accuracy, reduce the level of manual effort required and enable data driven decision making to ensure that the right supplies were readily available to clinicians in the right location at the right time.