Download PDF
WISE Employment Enhances Process Management with Nintex Promapp®
Technology Category
- Analytics & Modeling - Process Analytics
- Drones - Drone Flight & Navigation Software
Applicable Industries
- Education
- Marine & Shipping
Applicable Functions
- Maintenance
- Product Research & Development
Use Cases
- Personnel Tracking & Monitoring
- Process Control & Optimization
Services
- Training
The Challenge
WISE Employment, a not-for-profit employment services provider in Australia, was grappling with outdated, non-standardized process management and minimal continuous improvement. The organization was experiencing significant growth due to changes in government rules around Disability Employment Services (DES), which allowed job seekers to choose their provider. However, this growth highlighted the need for a more efficient and consistent approach to process management. WISE's processes were documented in a mix of Microsoft Word, Excel, and Visio, leading to inconsistencies, errors, inefficiencies, and duplication of work. Many of these processes were out of date, mapped in non-standard formats, and stored in various locations, with no specific individual responsible for them. This lack of centralized process management led to inconsistent customer experiences and hindered continuous improvement.
About The Customer
WISE Employment is a not-for-profit employment services provider based in Australia. Founded in 1992, the organization has grown from two people to a team of almost 1,000 employees. WISE Employment's mission is to empower people to enrich the community, and its ultimate goal is to help the most disadvantaged achieve long-term and sustainable employment. Each year, WISE helps more than 34,000 people across Australia through their Disability Employment Services and jobactive programs to find sustainable employment. In addition to supporting job seekers, WISE also runs a growing Social Enterprise that provides work for people with a disability through commercial cleaning services and grounds maintenance.
The Solution
WISE Employment turned to Nintex Promapp® to document its processes and establish a culture of continuous improvement. The organization set four key goals for its Nintex Promapp strategy: creating a culture of continuous improvement, placing the customer at the heart of their thinking, providing staff with process clarity and consistency, and quickly onboarding new staff. Nintex Promapp’s easy-to-use navigation allowed WISE employees to map and provide feedback on processes with minimal training. The navigation was personalized by roles, so staff only saw the processes relevant to them. Once mapped, WISE could apply value stream mapping and customer-centered design principles to improve the efficiency and effectiveness of their processes. Nintex Promapp also facilitated staff collaboration on processes and continuous improvement by providing a platform for feedback.
Operational Impact
Quantitative Benefit
Related Case Studies.
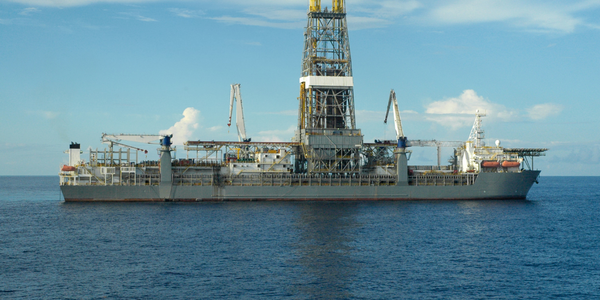
Case Study
Drill ship power challenge: hybrid solution solves distribution issues
Aspin Kemp & Associates (AKA), a manufacturer of electrical power and control systems headquartered in Montague, PEI, encountered one with its hybrid power initiative, the first hybrid drill floor destined for installation on ultra-deepwater drill ships operated by Transocean, Swiss offshore drilling contractors. Since on-site modification was impossible and scrap recycling of any modifications was unacceptable, the enclosures had to arrive ready-to-install.
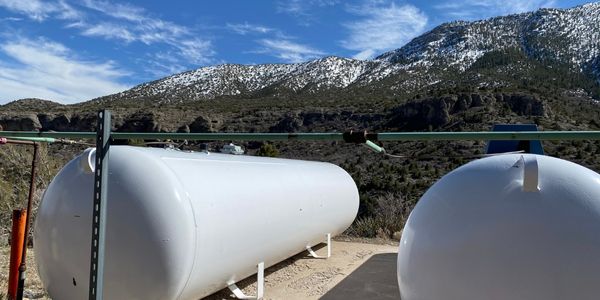
Case Study
Ensures Tanker Safety and Emissions Compliance
Storage tanks are irregular in shape and a certain amount of mathematical modelling is required to get an accurate representation of volume and, more importantly, the weight of material in each tank. In addition, countries have different emission regulations, so the ships position needed to be accurately known in order to geotag emission data.
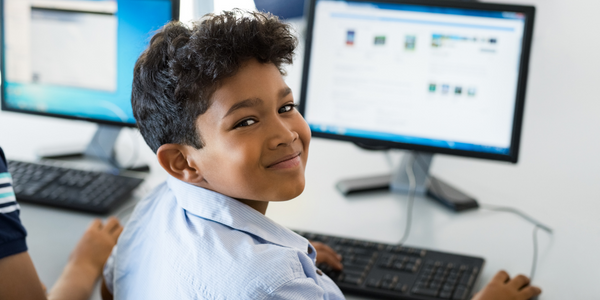
Case Study
IoT platform Enables Safety Solutions for U.S. School Districts
Designed to alert drivers when schoolchildren are present, especially in low-visibility conditions, school-zone flasher signals are typically updated manually at each school. The switching is based on the school calendar and manually changed when an unexpected early dismissal occurs, as in the case of a weather-event altering the normal schedule. The process to reprogram the flashers requires a significant effort by school district personnel to implement due to the large number of warning flashers installed across an entire school district.
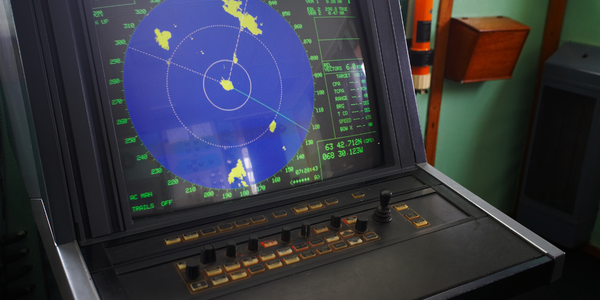
Case Study
Real-time Networked Sonar System for Ships
A multinational, knowledge-based corporation that delivers marine electronics solutions is utilizing industrial Ethernet technology to help ensure that operations at sea are dependable and optimal. Based in Europe, the company has nearly 4000 employees working in 20 countries around the world, and produces high-tech systems for offshore oil and gas operations, merchant marine systems, and various applications for the defense and aerospace industries. The company produces products and systems used by merchant vessels and offshore installations for positioning, navigation, automation, as well as for surveying and monitoring the seabed, and for fishing vessels and fi sheries research. As one of the major suppliers of high quality marine electronics in the world, their products include chart plotters for yachts, triple redundant dynamic positioning systems for oil drilling rigs, and sonar and instrument systems for scientifi c research vessels. Products used for marine applications must be rugged enough to endure the corrosive effects of salt water, and be able to withstand excessive amounts of vibration and shock. For this reason, the company only uses DNV and GL certified products and components to ensure that their systems can meet the high standards required by the maritime industry.
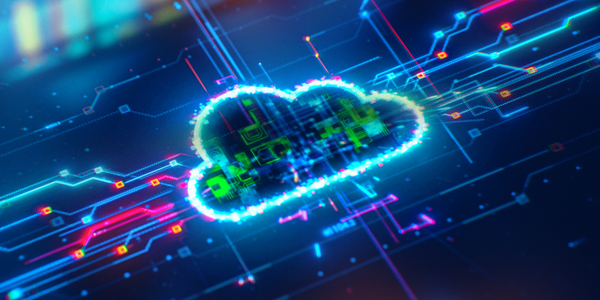
Case Study
Fleet Management Connectivity Solution for Marzam
Marzam, in order to ensure the best service, invested 3 million dollars in the construction of 2 fuel oil tanks with 40k gallons and 10k gallons capacity each, located in Manta, Ecuador. The customer needs to keep fleet operations going with fuel available at all times in order to guarantee quality of service. KEY ELEMENTS FOR THE CUSTOMER: Real-time level monitoring: Tank infrastructure remote level monitoring. Configure alerts and notifications when reaching critical values to avoid the need for emergency refills and optimize supply schedules. Real-time consumption monitoring: The customer needed an easy way to monitor in real-time accurate values of consumption.
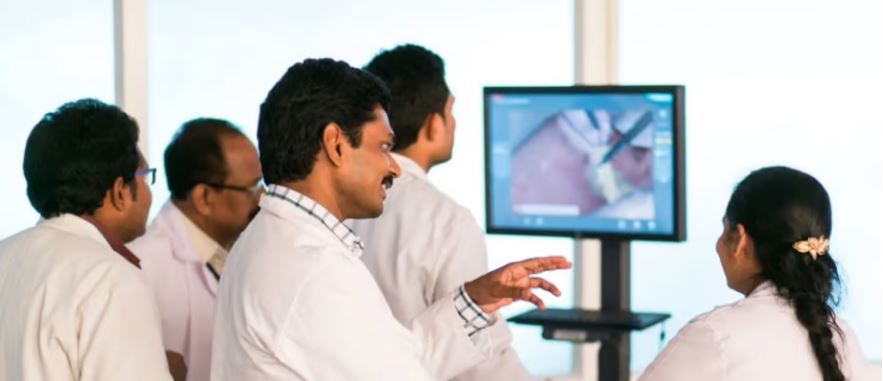
Case Study
Revolutionizing Medical Training in India: GSL Smart Lab and the LAP Mentor
The GSL SMART Lab, a collective effort of the GSL College of Medicine and the GSL College of Nursing and Health Science, was facing a challenge in providing superior training to healthcare professionals. As clinical medicine was becoming more focused on patient safety and quality of care, the need for medical simulation to bridge the educational gap between the classroom and the clinical environment was becoming increasingly apparent. Dr. Sandeep Ganni, the director of the GSL SMART Lab, envisioned a world-class surgical and medical training center where physicians and healthcare professionals could learn skills through simulation training. He was looking for different simulators for different specialties to provide both basic and advanced simulation training. For laparoscopic surgery, he was interested in a high fidelity simulator that could provide basic surgical and suturing skills training for international accreditation as well as specific hands-on training in complex laparoscopic procedures for practicing physicians in India.