Download PDF
XLDyn's Real-Time Management Visibility in Early Vehicle Requirements Development
Technology Category
- Analytics & Modeling - Real Time Analytics
- Robots - Autonomous Guided Vehicles (AGV)
Applicable Industries
- Aerospace
- Automotive
Applicable Functions
- Product Research & Development
Use Cases
- Real-Time Location System (RTLS)
- Vehicle Performance Monitoring
The Challenge
The automotive, heavy equipment, and aerospace industries face a significant challenge in verifying vehicle requirements, developing design parameters, and providing real-time project status to management. The traditional method of capturing requirements in a Word document is time-consuming and inefficient. Furthermore, the process of verifying these requirements using corporate fuel economy prediction software and cell equations is complex and requires a high level of expertise. Additionally, setting body bending and torsional mode natural frequency targets to meet program objectives is a critical task that requires precision and accuracy. The challenge also extends to the use of a coarse geometry model for dynamic finite element analysis, which requires the transmission of requirements and work requests to the CAE Team. Once completed, the results need to be returned and the status automatically updated, a process that can be prone to delays and inaccuracies.
About The Customer
The customer in this case study is a company operating in the automotive, heavy equipment, and aerospace industries. They are involved in the development of vehicles and need to verify vehicle requirements, develop design parameters, and provide real-time project status to management. They have specific targets for fuel economy and body bending and torsional mode natural frequencies that need to be met. They also use a coarse geometry model for dynamic finite element analysis and work closely with a CAE Team to achieve their objectives.
The Solution
XLDyn's MBSE models with integrated verification methods provide a solution to these challenges. The requirements, initially captured in a Word document, can be imported into XLDyn and converted into a SysML Diagram in a matter of minutes. This not only saves time but also enhances the accuracy and efficiency of the process. The requirements are then verified using the corporate fuel economy prediction software along with cell equations, ensuring that the vehicle meets the Combined City/Highway Fuel Economy target of 26 MPG. Furthermore, body bending and torsional mode natural frequency targets are set to meet program objectives. A coarse geometry model is used for dynamic finite element analysis, with the requirements and work request transmitted to the CAE Team. Once completed, the results are returned and the status automatically updated, providing real-time updates to project status. This allows the Chief Engineer to view the overall status of the vehicle program.
Operational Impact
Quantitative Benefit
Related Case Studies.
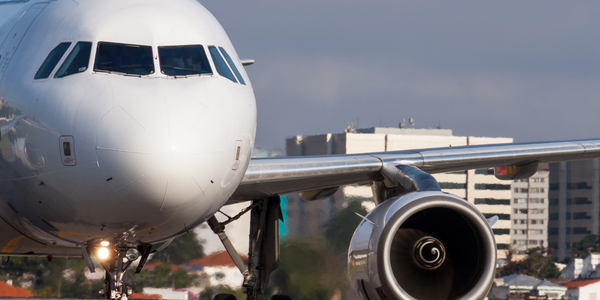
Case Study
Airbus Soars with Wearable Technology
Building an Airbus aircraft involves complex manufacturing processes consisting of thousands of moving parts. Speed and accuracy are critical to business and competitive advantage. Improvements in both would have high impact on Airbus’ bottom line. Airbus wanted to help operators reduce the complexity of assembling cabin seats and decrease the time required to complete this task.
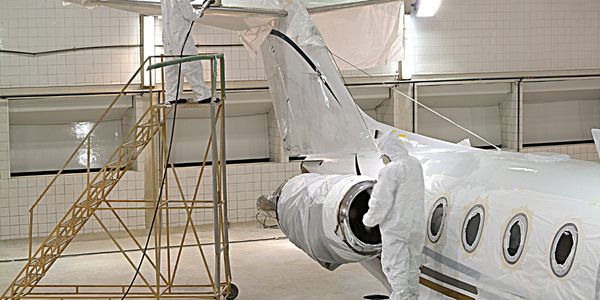
Case Study
Aircraft Predictive Maintenance and Workflow Optimization
First, aircraft manufacturer have trouble monitoring the health of aircraft systems with health prognostics and deliver predictive maintenance insights. Second, aircraft manufacturer wants a solution that can provide an in-context advisory and align job assignments to match technician experience and expertise.
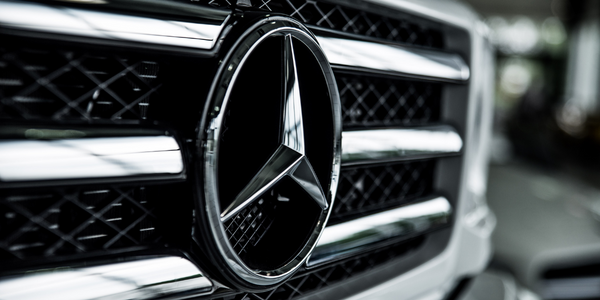
Case Study
Integral Plant Maintenance
Mercedes-Benz and his partner GAZ chose Siemens to be its maintenance partner at a new engine plant in Yaroslavl, Russia. The new plant offers a capacity to manufacture diesel engines for the Russian market, for locally produced Sprinter Classic. In addition to engines for the local market, the Yaroslavl plant will also produce spare parts. Mercedes-Benz Russia and his partner needed a service partner in order to ensure the operation of these lines in a maintenance partnership arrangement. The challenges included coordinating the entire maintenance management operation, in particular inspections, corrective and predictive maintenance activities, and the optimizing spare parts management. Siemens developed a customized maintenance solution that includes all electronic and mechanical maintenance activities (Integral Plant Maintenance).
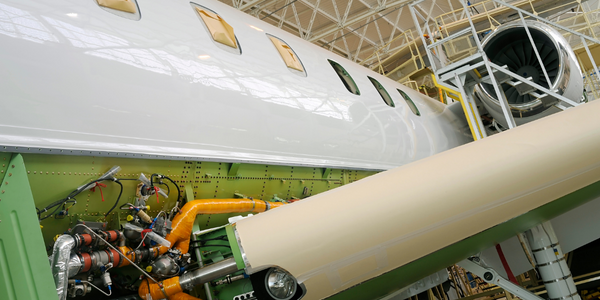
Case Study
Aerospace & Defense Case Study Airbus
For the development of its new wide-body aircraft, Airbus needed to ensure quality and consistency across all internal and external stakeholders. Airbus had many challenges including a very aggressive development schedule and the need to ramp up production quickly to satisfy their delivery commitments. The lack of communication extended design time and introduced errors that drove up costs.