Download PDF
Yamal LNG Enhances Collaboration with AVEVA
Technology Category
- Application Infrastructure & Middleware - Data Exchange & Integration
- Functional Applications - Remote Monitoring & Control Systems
Applicable Industries
- Oil & Gas
Applicable Functions
- Discrete Manufacturing
- Quality Assurance
Use Cases
- Predictive Maintenance
- Remote Asset Management
Services
- System Integration
- Software Design & Engineering Services
The Challenge
Yamal LNG, a joint venture operating in the Russian arctic, faced several challenges in its project. The harsh climate made any setbacks dangerous and costly. The project involved many partners, making it difficult to keep documents up-to-date and approved by all. The need for manual checking of documents every 3-4 months was time-consuming and prone to errors. The process also precluded the simultaneous and common review of documents by teams which were geographically dispersed. The project's location within the Arctic Circle added an additional challenge, as even small delays could have a large impact on time scales if work is pushed into the arctic winter.
About The Customer
Yamal LNG is a joint venture of NOVATEK, TOTAL, CNPC and Silk Road Fund, responsible for the operation of the most northern liquefied natural gas project in the world, located deep in the Russian arctic. The region is ice-bound for seven to nine months of each year. The project encompasses natural gas production from the South Tambey Field, liquefaction and shipping. PJSC “YUZHNIIGIPROGAZ”, a design and project engineering institute, acts as the engineering consultant for the terminal. It specialises in complex plants in polar regions.
The Solution
Yamal LNG and YUZHNIIGIPROGAZ adopted a data-centric approach to mitigate the challenges at every stage of the design and construction. They used AVEVA's Integrated Engineering and Design suite, which enabled the whole project to be created using AVEVA Everything3D. The digital version of the asset allowed pipelines, structural steel, equipment, cables and instruments to be fully incorporated into a 3D model. Regular clash checking and reviews ensured that no errors were transferred to site and onsite rework was kept to an absolute minimum. AVEVA Diagrams helped to generate all the project and instrumentation drawings containing all tagged information. The fully integrated design tools ensured that the 2D and 3D designs were synchronized at all times. The project team used AVEVA Engage to review the 3D model together, which made it possible to look at different parameters, such as tags, equipment supplies and pipeline objects.
Operational Impact
Quantitative Benefit
Related Case Studies.
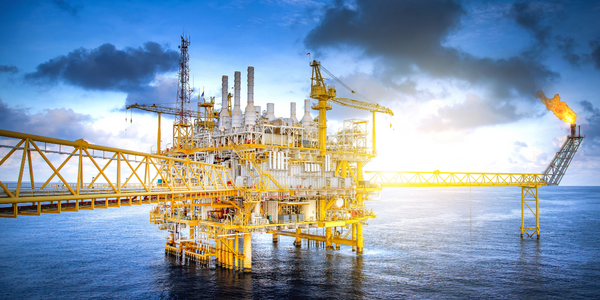
Case Study
Taking Oil and Gas Exploration to the Next Level
DownUnder GeoSolutions (DUG) wanted to increase computing performance by 5 to 10 times to improve seismic processing. The solution must build on current architecture software investments without sacrificing existing software and scale computing without scaling IT infrastructure costs.
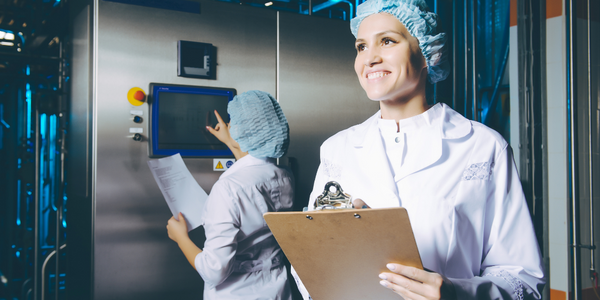
Case Study
Remote Wellhead Monitoring
Each wellhead was equipped with various sensors and meters that needed to be monitored and controlled from a central HMI, often miles away from the assets in the field. Redundant solar and wind generators were installed at each wellhead to support the electrical needs of the pumpstations, temperature meters, cameras, and cellular modules. In addition to asset management and remote control capabilities, data logging for remote surveillance and alarm notifications was a key demand from the customer. Terra Ferma’s solution needed to be power efficient, reliable, and capable of supporting high-bandwidth data-feeds. They needed a multi-link cellular connection to a central server that sustained reliable and redundant monitoring and control of flow meters, temperature sensors, power supply, and event-logging; including video and image files. This open-standard network needed to interface with the existing SCADA and proprietary network management software.
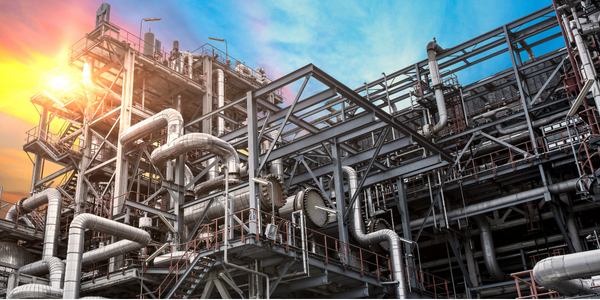
Case Study
Refinery Saves Over $700,000 with Smart Wireless
One of the largest petroleum refineries in the world is equipped to refine various types of crude oil and manufacture various grades of fuel from motor gasoline to Aviation Turbine Fuel. Due to wear and tear, eight hydrogen valves in each refinery were leaking, and each cost $1800 per ton of hydrogen vented. The plant also had leakage on nearly 30 flare control hydrocarbon valves. The refinery wanted a continuous, online monitoring system that could catch leaks early, minimize hydrogen and hydrocarbon production losses, and improve safety for maintenance.