Download PDF
Zscaler and SICK AG: A Visionary Cloud Implementation
Technology Category
- Infrastructure as a Service (IaaS) - Cloud Databases
- Networks & Connectivity - Gateways
Applicable Industries
- Automotive
- National Security & Defense
Applicable Functions
- Maintenance
Use Cases
- Manufacturing System Automation
- Tamper Detection
Services
- Cloud Planning, Design & Implementation Services
- Hardware Design & Engineering Services
The Challenge
SICK AG, a global leader in sensors, systems, and services for industrial automation technology, was facing a challenge in modernizing its IT security and driving digitization. The company, which has a significant international presence with over 50 subsidiaries and approximately 10,000 employees, was heavily reliant on sensor intelligence for Industry 4.0 processes. However, the existing four internet gateways in Europe, Asia, and North America were a limiting factor for a cloud-first infrastructure. The company needed a solution that would allow secure internet breakouts at each location and facilitate the exchange of data recorded by sensors via the cloud. In 2015, SICK decided to stop using its existing security hardware and sought a cloud-based solution to drive digitization and modernize its IT security.
About The Customer
SICK AG is a global leader in sensors, systems, and services for industrial automation technology. The company offers intelligent solutions for Industry 4.0 and uses the cloud for more than just its product range. Based in Waldkirch im Breisgau in Southwest Germany, SICK AG has an international presence with more than 50 subsidiaries and approximately 10,000 employees. The company's sensors are omnipresent in the automotive manufacturing, aviation, transport, food packaging, and recycling industries. With sensor intelligence, SICK enables Industry 4.0 processes and creates solutions for the safe and efficient control of operations, protecting people from accidents and avoiding environmental damage.
The Solution
SICK AG turned to Zscaler's cloud-based internet security to modernize its IT security and drive digitization. The Zscaler Zero Trust Exchange became foundational for SICK's successful digitization. The IT department took advantage of the Zscaler cloud proxy to pave the way for secure internet breakouts at each location. This allowed SICK to roll out new cloud applications securely. SICK also implemented Zscaler's SSL scanning to fully scan encrypted web traffic for malware, significantly increasing their security levels. The company also added more Zscaler functionalities to support its growing portfolio of cloud-based sensor solutions. The Cloud Firewall provided the option of applying very granular rules, adding extra security and enabling secure communication with sensors via protocols that have not been inspected by the web proxy.
Operational Impact
Quantitative Benefit
Related Case Studies.
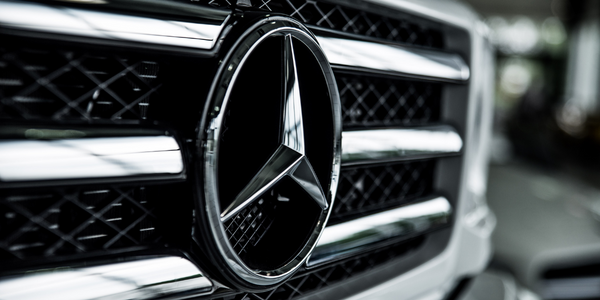
Case Study
Integral Plant Maintenance
Mercedes-Benz and his partner GAZ chose Siemens to be its maintenance partner at a new engine plant in Yaroslavl, Russia. The new plant offers a capacity to manufacture diesel engines for the Russian market, for locally produced Sprinter Classic. In addition to engines for the local market, the Yaroslavl plant will also produce spare parts. Mercedes-Benz Russia and his partner needed a service partner in order to ensure the operation of these lines in a maintenance partnership arrangement. The challenges included coordinating the entire maintenance management operation, in particular inspections, corrective and predictive maintenance activities, and the optimizing spare parts management. Siemens developed a customized maintenance solution that includes all electronic and mechanical maintenance activities (Integral Plant Maintenance).
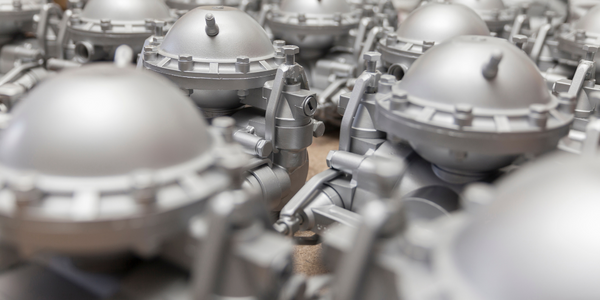
Case Study
Monitoring of Pressure Pumps in Automotive Industry
A large German/American producer of auto parts uses high-pressure pumps to deburr machined parts as a part of its production and quality check process. They decided to monitor these pumps to make sure they work properly and that they can see any indications leading to a potential failure before it affects their process.