下载PDF
Auto Avaliar: Transforming Automotive eCommerce with Google Cloud
技术
- 分析与建模 - 机器学习
- 分析与建模 - 预测分析
适用行业
- 汽车
- 水泥
适用功能
- 产品研发
- 销售与市场营销
用例
- 篡改检测
- 车辆到基础设施 (V2I)
服务
- 云规划/设计/实施服务
- 数据科学服务
挑战
Auto Avaliar 是巴西的一个 B2B 汽车电子商务平台,需要扩展其基础设施以支持更多用户、新应用程序和不断变化的安全要求。传统数据中心基础设施的扩展不具有成本效益或效率。
关于客户
Auto Avaliar 是巴西流行的 B2B 汽车电子商务平台,被超过 30,000 家多品牌商店和 3,500 家经销商使用。他们每年评估超过 240 万辆汽车,产生 14 亿美元的销售额。
解决方案
Auto Avaliar 选择了 Google Cloud 并与 Google 云托管服务提供商 SantoDigital 合作,将其平台迁移到快速、安全且可靠的基于云的解决方案。他们添加了各种 Google Cloud 解决方案来优化性能和效率。
运营影响
数量效益
相关案例.
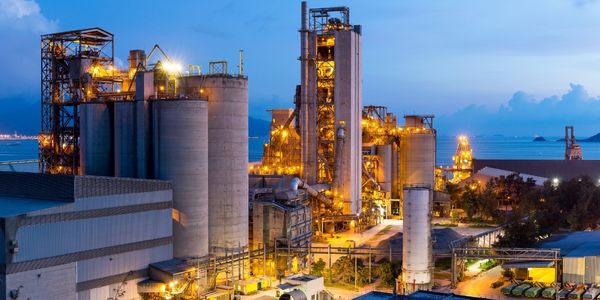
Case Study
System 800xA at Indian Cement Plants
Chettinad Cement recognized that further efficiencies could be achieved in its cement manufacturing process. It looked to investing in comprehensive operational and control technologies to manage and derive productivity and energy efficiency gains from the assets on Line 2, their second plant in India.
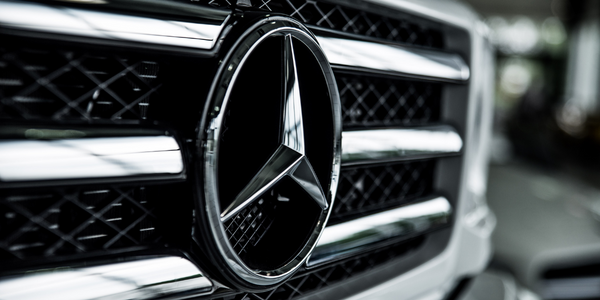
Case Study
Integral Plant Maintenance
Mercedes-Benz and his partner GAZ chose Siemens to be its maintenance partner at a new engine plant in Yaroslavl, Russia. The new plant offers a capacity to manufacture diesel engines for the Russian market, for locally produced Sprinter Classic. In addition to engines for the local market, the Yaroslavl plant will also produce spare parts. Mercedes-Benz Russia and his partner needed a service partner in order to ensure the operation of these lines in a maintenance partnership arrangement. The challenges included coordinating the entire maintenance management operation, in particular inspections, corrective and predictive maintenance activities, and the optimizing spare parts management. Siemens developed a customized maintenance solution that includes all electronic and mechanical maintenance activities (Integral Plant Maintenance).
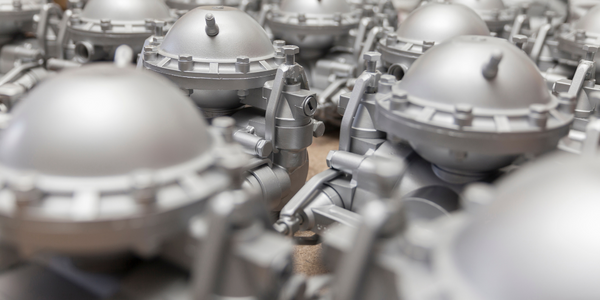
Case Study
Monitoring of Pressure Pumps in Automotive Industry
A large German/American producer of auto parts uses high-pressure pumps to deburr machined parts as a part of its production and quality check process. They decided to monitor these pumps to make sure they work properly and that they can see any indications leading to a potential failure before it affects their process.