下载PDF
Building a next-generation materials handler with additive manufacturing
技术
- 功能应用 - 远程监控系统
- 其他 - 添加剂制造
适用行业
- 零售
适用功能
- 物流运输
- 仓库和库存管理
用例
- 添加剂制造
- 库存管理
- 仓库自动化
服务
- 硬件设计与工程服务
- 软件设计与工程服务
挑战
Bastian Solutions, a leading materials handling company owned by Toyota Advanced Logistics, was faced with the challenge of meeting the high expectations of today's shoppers for on-demand fulfillment. Retailers require innovative materials handling systems that can navigate tight warehouse and shelving spaces to fill orders quickly. They also need picking technologies that can handle a wide variety of product shapes, sizes, and densities without having to invest additional capital in multiple custom grippers for the picking arms. To address these complex set of problems, Bastian Solutions set out to engineer an improved solution. This effort resulted in the Bastian Solutions Shuttle System, an advanced, customizable electrical robot arm-and-shuttle combo that autonomously picks and moves a range of differently sized and weighted products. However, creating a new disruptive materials handler like the Bastian Solutions Shuttle System required Bastian Solutions to use a disruptive method—additive manufacturing. But without on-site 3D printing capabilities, Bastian Solutions sought out a partner that could help make their vision a reality.
关于客户
Bastian Solutions is a leading materials handling company owned by Toyota Advanced Logistics. The company is dedicated to providing superior material handling and automation solutions to its clients. Bastian Solutions is committed to providing the best technology, quality, and service to their customers. They strive to innovate and create advanced solutions to complex problems. One of their latest projects is the Bastian Solutions Shuttle System, an advanced, customizable electrical robot arm-and-shuttle combo that autonomously picks and moves a range of differently sized and weighted products. This system is designed to meet the high expectations of today's shoppers for on-demand fulfillment.
解决方案
To create the Bastian Solutions Shuttle System, the company partnered with Fast Radius, a company with technology partners like HP 3D Printing and Carbon®. Fast Radius enabled Bastian to make a truly innovative advanced materials handling robot unlike any on the market. Nearly 50 percent of the bill-of-materials was made using additive manufacturing in Fast Radius’ Chicago factory. By using 3D printing for critical parts, Bastian Solutions can quickly scale the robot arm for its customers’ requirements. Once the adjusted design is submitted to Fast Radius’ Virtual Warehouse, the customer receives the additive parts in days instead of weeks or months. This helps customers get their new materials handling systems up and running with little interruption to their business. Additive manufacturing unlocked entirely new engineering opportunities as Bastian Solutions was designing the robot arm. It allowed for a more lightweight machine, increased energy efficiencies, a multi-faceted gripper, and enhanced protective parts.
运营影响
数量效益
相关案例.
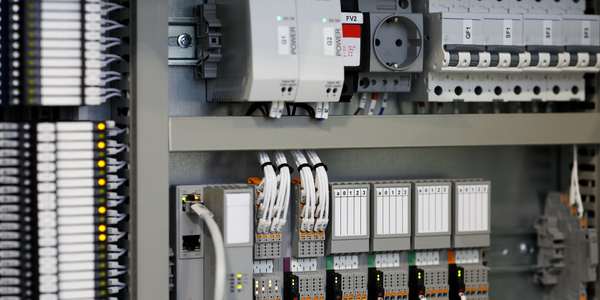
Case Study
Improving Production Line Efficiency with Ethernet Micro RTU Controller
Moxa was asked to provide a connectivity solution for one of the world's leading cosmetics companies. This multinational corporation, with retail presence in 130 countries, 23 global braches, and over 66,000 employees, sought to improve the efficiency of their production process by migrating from manual monitoring to an automatic productivity monitoring system. The production line was being monitored by ABB Real-TPI, a factory information system that offers data collection and analysis to improve plant efficiency. Due to software limitations, the customer needed an OPC server and a corresponding I/O solution to collect data from additional sensor devices for the Real-TPI system. The goal is to enable the factory information system to more thoroughly collect data from every corner of the production line. This will improve its ability to measure Overall Equipment Effectiveness (OEE) and translate into increased production efficiencies. System Requirements • Instant status updates while still consuming minimal bandwidth to relieve strain on limited factory networks • Interoperable with ABB Real-TPI • Small form factor appropriate for deployment where space is scarce • Remote software management and configuration to simplify operations
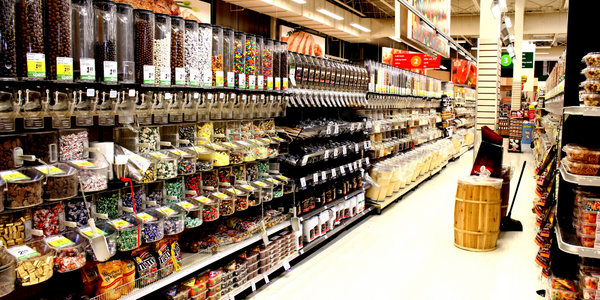
Case Study
How Sirqul’s IoT Platform is Crafting Carrefour’s New In-Store Experiences
Carrefour Taiwan’s goal is to be completely digital by end of 2018. Out-dated manual methods for analysis and assumptions limited Carrefour’s ability to change the customer experience and were void of real-time decision-making capabilities. Rather than relying solely on sales data, assumptions, and disparate systems, Carrefour Taiwan’s CEO led an initiative to find a connected IoT solution that could give the team the ability to make real-time changes and more informed decisions. Prior to implementing, Carrefour struggled to address their conversion rates and did not have the proper insights into the customer decision-making process nor how to make an immediate impact without losing customer confidence.
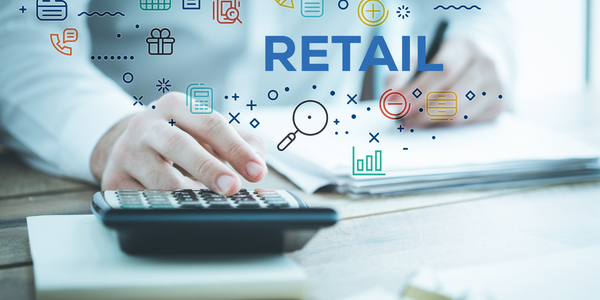
Case Study
Digital Retail Security Solutions
Sennco wanted to help its retail customers increase sales and profits by developing an innovative alarm system as opposed to conventional connected alarms that are permanently tethered to display products. These traditional security systems were cumbersome and intrusive to the customer shopping experience. Additionally, they provided no useful data or analytics.
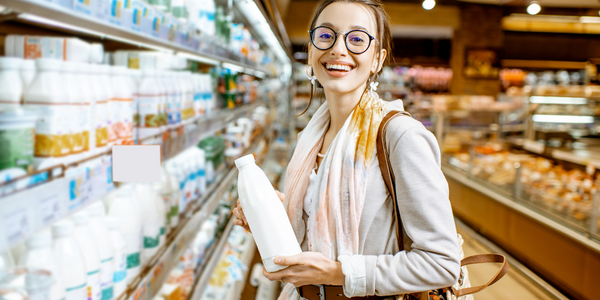
Case Study
Ensures Cold Milk in Your Supermarket
As of 2014, AK-Centralen has over 1,500 Danish supermarkets equipped, and utilizes 16 operators, and is open 24 hours a day, 365 days a year. AK-Centralen needed the ability to monitor the cooling alarms from around the country, 24 hours a day, 365 days a year. Each and every time the door to a milk cooler or a freezer does not close properly, an alarm goes off on a computer screen in a control building in southwestern Odense. This type of alarm will go off approximately 140,000 times per year, equating to roughly 400 alarms in a 24-hour period. Should an alarm go off, then there is only a limited amount of time to act before dairy products or frozen pizza must be disposed of, and this type of waste can quickly start to cost a supermarket a great deal of money.
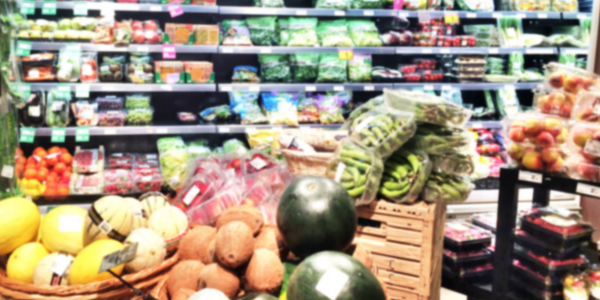
Case Study
Supermarket Energy Savings
The client had previously deployed a one-meter-per-store monitoring program. Given the manner in which energy consumption changes with external temperature, hour of the day, day of week and month of year, a single meter solution lacked the ability to detect the difference between a true problem and a changing store environment. Most importantly, a single meter solution could never identify root cause of energy consumption changes. This approach never reduced the number of truck-rolls or man-hours required to find and resolve issues.