下载PDF
CAE Simulation Driven Product Development for Expandable Liner Hanger
技术
- 分析与建模 - 数字孪生/模拟
- 传感器 - 触觉传感器
适用行业
- 水泥
- 石油和天然气
适用功能
- 产品研发
- 质量保证
用例
- 数字孪生
- 虚拟现实
服务
- 系统集成
- 测试与认证
挑战
贝克休斯是全球石油和天然气行业油田服务、产品、技术和系统的领先供应商,面临着多项环境和技术挑战。其中包括在近海深水和北极环境中作业、处理页岩和水力压裂,以及遵守更严格的环境和安全法规。技术挑战包括钻更深的井、应对极端压力和温度以及处理非常规地质变化。该公司还负责开发可扩展尾管悬挂系统,这是一种机械系统,用于在石油和天然气行业的井眼施工作业期间将尾管柱连接到先前运行的套管柱的底部。该系统用于在极端深水环境、盐下区域或斜井下悬挂较重的衬管。
关于客户
贝克休斯是为全球石油和天然气行业提供油田服务、产品、技术和系统的领先供应商。该公司在全球运营,拥有约 60,000 名员工,总部位于德克萨斯州休斯顿。 2013年,该公司报告收入为224亿美元。贝克休斯以其针对石油和天然气行业所面临挑战的创新解决方案而闻名,特别是在海上深水钻探、北极环境、页岩和水力压裂领域,以及遵守严格的环境和安全法规。
解决方案
为了克服这些挑战,贝克休斯将 CAE 仿真与产品开发相结合。这种方法最大限度地提高了产品成功的可能性、产品质量和可靠性、客户满意度和员工士气。它还通过消除浪费来最大限度地减少开发成本和时间。 CAE 仿真与 PDM 的集成有助于以“一次成功”策略开发产品,了解开发早期阶段的设计限制、约束、装配交互,并减少原型数量。该公司遵循七步 CAE 仿真方法,包括 FE 模型构建、验证、初始验证、细化或重建、优化、可靠性评估/改进和迭代。该方法用于加速可扩展衬管悬挂系统设计的开发,预测其悬挂能力和密封完整性,优化其性能并提高其可靠性。
运营影响
数量效益
相关案例.
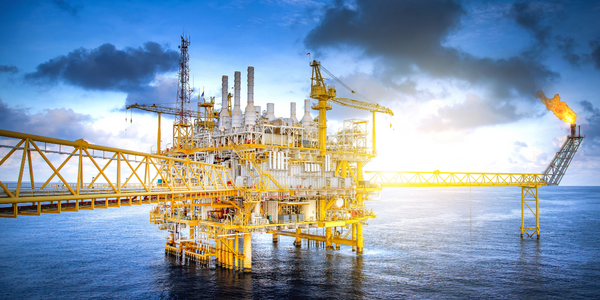
Case Study
Taking Oil and Gas Exploration to the Next Level
DownUnder GeoSolutions (DUG) wanted to increase computing performance by 5 to 10 times to improve seismic processing. The solution must build on current architecture software investments without sacrificing existing software and scale computing without scaling IT infrastructure costs.
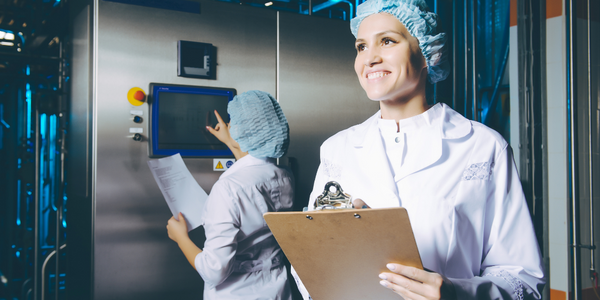
Case Study
Remote Wellhead Monitoring
Each wellhead was equipped with various sensors and meters that needed to be monitored and controlled from a central HMI, often miles away from the assets in the field. Redundant solar and wind generators were installed at each wellhead to support the electrical needs of the pumpstations, temperature meters, cameras, and cellular modules. In addition to asset management and remote control capabilities, data logging for remote surveillance and alarm notifications was a key demand from the customer. Terra Ferma’s solution needed to be power efficient, reliable, and capable of supporting high-bandwidth data-feeds. They needed a multi-link cellular connection to a central server that sustained reliable and redundant monitoring and control of flow meters, temperature sensors, power supply, and event-logging; including video and image files. This open-standard network needed to interface with the existing SCADA and proprietary network management software.
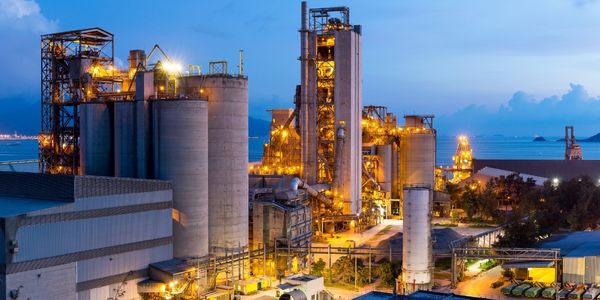
Case Study
System 800xA at Indian Cement Plants
Chettinad Cement recognized that further efficiencies could be achieved in its cement manufacturing process. It looked to investing in comprehensive operational and control technologies to manage and derive productivity and energy efficiency gains from the assets on Line 2, their second plant in India.
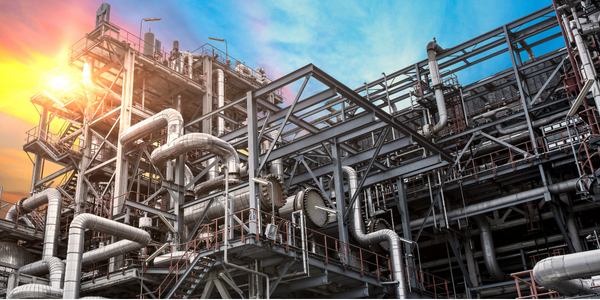
Case Study
Refinery Saves Over $700,000 with Smart Wireless
One of the largest petroleum refineries in the world is equipped to refine various types of crude oil and manufacture various grades of fuel from motor gasoline to Aviation Turbine Fuel. Due to wear and tear, eight hydrogen valves in each refinery were leaking, and each cost $1800 per ton of hydrogen vented. The plant also had leakage on nearly 30 flare control hydrocarbon valves. The refinery wanted a continuous, online monitoring system that could catch leaks early, minimize hydrogen and hydrocarbon production losses, and improve safety for maintenance.