下载PDF
Compañía Española de Petróleos (CEPSA) Streamlines Scheduling Workflows With Integrated Refinery Scheduling and Blending
技术
- 功能应用 - 企业资源规划系统 (ERP)
适用行业
- 石油和天然气
适用功能
- 离散制造
- 物流运输
用例
- 预测性维护
- 车队管理
服务
- 系统集成
- 培训
挑战
CEPSA, an integrated energy company, was looking to create a solution that would involve various business units in a coordinated way to optimize the global margin by establishing an integrated management model. Prior to the corporate initiative to improve the business processes in CEPSA, schedulers had been using homemade tools based on Excel files that were managed and reported by each individual scheduling stakeholder in a refinery. Since this method of scheduling provided no collaboration, there was little to no interaction among schedulers, causing inefficiencies and lost opportunities within CEPSA’s refineries to execute on the optimal plan. Additionally, because the spreadsheets were standalone, they provided no integration with Aspen PIMS (CEPSA’s planning solution since 2014), creating siloed departments and a disconnect between planning and operations.
关于客户
Compañía Española de Petróleos, S.A.U. (CEPSA) is an integrated energy company operating at every stage in the oil and gas value chain. Headquartered in Madrid, Spain with more than 10,000 employees, CEPSA is the fourth-largest industrial group in Spain. The company has over 90 years of experience in the development of large-scale projects in different phases of the oil and gas value chain, both nationally and internationally. The company is engaged in petroleum and natural gas exploration and production activities, refining and the transport and sale of crude oil derivatives, petrochemicals, gas and electricity. Thanks to its flexibility and ability to adapt, CEPSA has become a benchmark company in its sector in Spain. The company operates on five continents through progressive internationalization of its activities, with business interests in several European countries as well as Algeria, Brazil, Canada, Colombia, Panama, Peru and Portugal.
解决方案
CEPSA decided to move forward with AspenTech as the vendor for their refinery scheduling and blending solution. AspenTech already had a long-standing strategic partnership with CEPSA, providing solutions in petroleum supply chain to their organization. The integration of Aspen PIMS with Aspen Petroleum Scheduler and Aspen Refinery Multi-Blend Optimizer would provide CEPSA with shared common assay data, unit sub-models, blending correlations and planning targets (key process indicators, or KPIs). Another driver was the integration between rigorous models with Aspen HYSYS®, planning models in Aspen PIMS and scheduling with Aspen Petroleum Scheduler and Aspen Refinery Multi-Blend Optimizer. These capabilities and features aligned with the corporate objectives to automate and integrate the different processes in the planning cycle. CEPSA implemented AspenTech refinery scheduling and blending solutions at both the La Rábida and GibraltarSan Roque refineries sequentially. A phased approach was taken in a four-step process that took approximately 12 months per site.
运营影响
数量效益
相关案例.
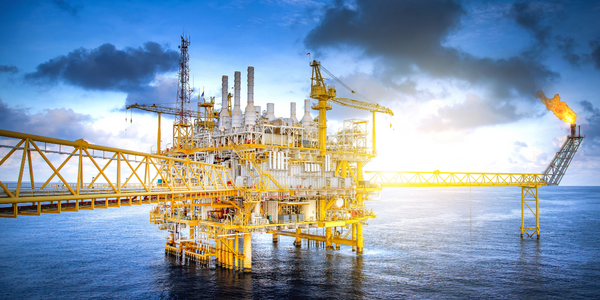
Case Study
Taking Oil and Gas Exploration to the Next Level
DownUnder GeoSolutions (DUG) wanted to increase computing performance by 5 to 10 times to improve seismic processing. The solution must build on current architecture software investments without sacrificing existing software and scale computing without scaling IT infrastructure costs.
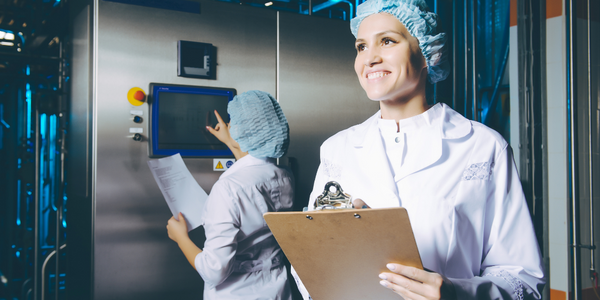
Case Study
Remote Wellhead Monitoring
Each wellhead was equipped with various sensors and meters that needed to be monitored and controlled from a central HMI, often miles away from the assets in the field. Redundant solar and wind generators were installed at each wellhead to support the electrical needs of the pumpstations, temperature meters, cameras, and cellular modules. In addition to asset management and remote control capabilities, data logging for remote surveillance and alarm notifications was a key demand from the customer. Terra Ferma’s solution needed to be power efficient, reliable, and capable of supporting high-bandwidth data-feeds. They needed a multi-link cellular connection to a central server that sustained reliable and redundant monitoring and control of flow meters, temperature sensors, power supply, and event-logging; including video and image files. This open-standard network needed to interface with the existing SCADA and proprietary network management software.
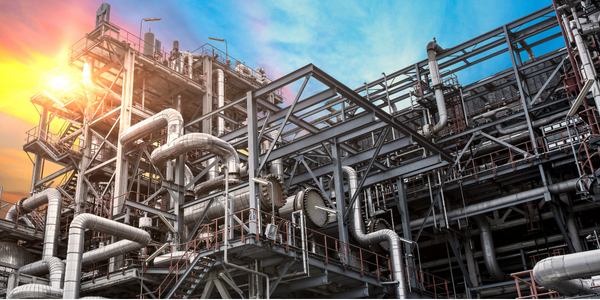
Case Study
Refinery Saves Over $700,000 with Smart Wireless
One of the largest petroleum refineries in the world is equipped to refine various types of crude oil and manufacture various grades of fuel from motor gasoline to Aviation Turbine Fuel. Due to wear and tear, eight hydrogen valves in each refinery were leaking, and each cost $1800 per ton of hydrogen vented. The plant also had leakage on nearly 30 flare control hydrocarbon valves. The refinery wanted a continuous, online monitoring system that could catch leaks early, minimize hydrogen and hydrocarbon production losses, and improve safety for maintenance.