下载PDF
Continuous Casting: Optimizing Both Machine and Process with Simulation
技术
- 分析与建模 - 数字孪生/模拟
- 分析与建模 - 预测分析
- 应用基础设施与中间件 - 数据可视化
适用行业
- 金属
适用功能
- 流程制造
- 质量保证
用例
- 预测性维护
- 过程控制与优化
- 数字孪生
服务
- 软件设计与工程服务
- 系统集成
挑战
Continuous casting presents numerous variables that need to be analyzed to improve technology and advance the boundaries of steelmaking. The process involves transforming a constant stream of liquid steel into endless strands of solid metal, which requires precise control to minimize waste and improve yield. The challenge is to understand and simulate the complex processes involved in continuous casting, including fluid flow, solidification, and mechanical deformation, to achieve superior quality and cost efficiency.
关于客户
SMS Concast is a leading company in the field of continuous casting, with over 60 years of experience in designing and building technical equipment for steel melting, refining, and continuous casting. The company holds a worldwide market share of over 40 percent and is known for pushing the limits of steelmaking technology. SMS Concast uses advanced simulation techniques to ensure their customers can produce high-quality steel products while reducing energy consumption and waste. The company has implemented innovative solutions in steel plants worldwide, including in Taiwan, Germany, and South Korea.
解决方案
SMS Concast uses simulation at every stage of the continuous casting process to analyze fluid flow, solidification, and mechanical deformation. They employ COMSOL Multiphysics to simulate the electromagnetic stirring of liquid steel, which is crucial for achieving high-quality steel with minimal non-metallic inclusions and even composition. The company also developed a new type of mold to cast billets with large rounded corners, allowing for hot charging directly to the rolling mill without reheating. This innovative mold design was successfully implemented at Tung Ho Steel in Taiwan, resulting in significant environmental and economic benefits.
运营影响
数量效益
相关案例.
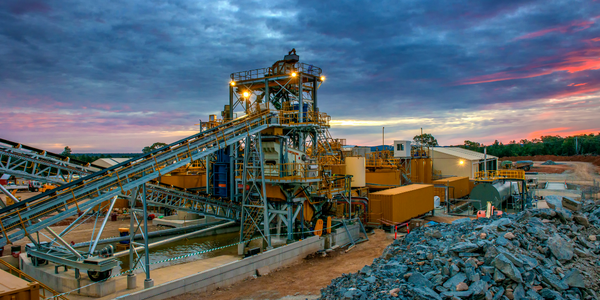
Case Study
Goldcorp: Internet of Things Enables the Mine of the Future
Goldcorp is committed to responsible mining practices and maintaining maximum safety for its workers. At the same time, the firm is constantly exploring ways to improve the efficiency of its operations, extend the life of its assets, and control costs. Goldcorp needed technology that can maximize production efficiency by tracking all mining operations, keep employees safe with remote operations and monitoring of hazardous work areas and control production costs through better asset and site management.
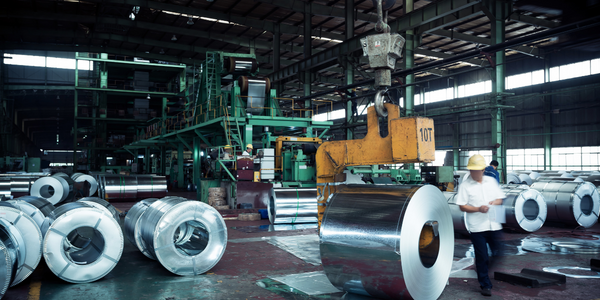
Case Study
KSP Steel Decentralized Control Room
While on-site in Pavlodar, Kazakhstan, the DAQRI team of Business Development and Solutions Architecture personnel worked closely with KSP Steel’s production leadership to understand the steel production process, operational challenges, and worker pain points.
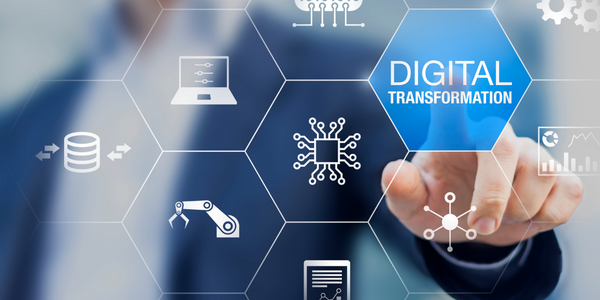
Case Study
Bluescope Steel on Path to Digitally Transform Operations and IT
Increasing competition and fluctuations in the construction market prompted BlueScope Steel to look toward digital transformation of its four businesses, including modern core applications and IT infrastructure. BlueScope needed to modernize its infrastructure and adopt new technologies to improve operations and supply chain efficiency while maintaining and updating an aging application portfolio.
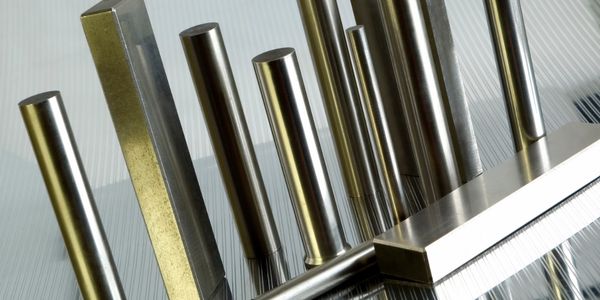
Case Study
RobotStudio Case Study: Benteler Automobiltechnik
Benteler has a small pipe business area for which they produce fuel lines and coolant lines made of aluminum for Porsche and other car manufacturers. One of the problems in production was that when Benteler added new products, production had too much downtime.
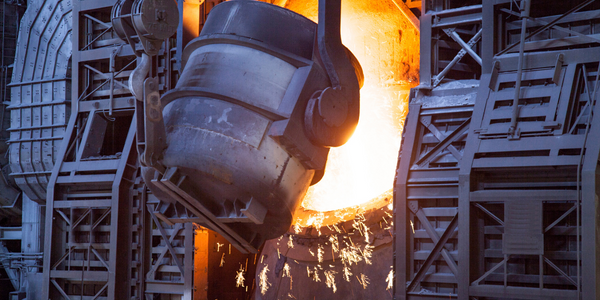
Case Study
Continuous Casting Machines in a Steel Factory
With a very broad range of applications, steel is an important material and has been developed into the most extensive alloy in the engineering world. Since delivering high quality is absolutely crucial for steel plants, ensuring maximum productivity and the best quality production are the keys to competitiveness in the steel industry. Additionally, working conditions in steel factories are not suitable for workers to stay in for long periods of time, so manufactures usually adopt various machines to complete the steel production processes. However, the precision of these machines is often overestimated and the lack of flexibility also makes supervisors unable to adjust operating procedures. A renowned steel factory in Asia planned to improve its Distributed Control System (DCS) of furnaces as well as addressing the problem of insufficient accuracy. However, most well-known international equipment suppliers can not provide a satisfactory solution and local maintenance because the project needed new technologies to more accurately control equipment operations. By implementing Advantech’s automated monitoring and control solution, steel factories can not only improve the manufacturing processes but can also allow users to add additional functions to the existing system so as to make sure the operation runs at high efficiency.
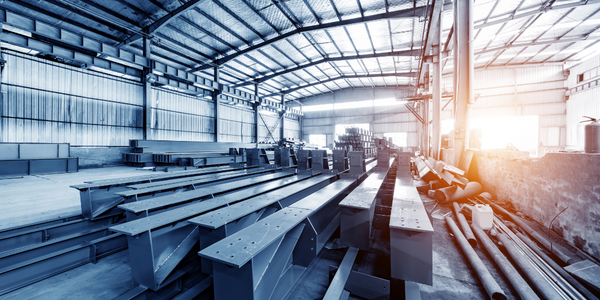
Case Study
Automated Predicitive Analytics For Steel/Metals Industry
Asset to be monitored: Wire Compactor that produces Steel RebarCustomer Faced The Following Challenges:Dependent upon machine uptime.Pressure cylinders within the compactor fail to control compression and speed causing problems in binding the coil.Equipment failure occurs in the final stage of production causing the entire line to stop, can you say bottleneck?Critical asset unequipped with sensors to produce data.