下载PDF
Digital Transformation with Predictive Maintenance Drives Cost Savings
技术
- 分析与建模 - 机器学习
- 分析与建模 - 预测分析
适用行业
- 石油和天然气
适用功能
- 维护
用例
- 预测性维护
服务
- 数据科学服务
挑战
The customer, a diversified energy company with operations in refining, marketing, midstream, chemicals and specialties, had experienced three previous failures of a hydrogen compressor resulting in millions in production losses and additional maintenance costs. The company had begun its own digital transformation initiative that uses big data, machine learning and artificial intelligence (AI) to drive cultural change in the organization. As part of the initiative, they were investigating predictive maintenance. The customer decided to organize a competitive bakeoff, trimming an initial list of ten predictive analytics vendors to a handful of finalists. Ultimately, AspenTech was chosen as the sole vendor to execute an online pilot project.
关于客户
The customer is a diversified energy company with operations in refining, marketing, midstream, chemicals and specialties. They operate more than a dozen refineries in the U.S. and Europe with a total capacity of over 2 million barrels of crude oil per day. The company had begun its own digital transformation initiative that uses big data, machine learning and artificial intelligence (AI) to drive cultural change in the organization. As part of the initiative, they were investigating predictive maintenance.
解决方案
Aspen Mtell was implemented as the predictive maintenance solution. A hydrogen compressor in one of the refineries had multiple historical ring and piston failures costing over $250 million USD across just 3 events. Aspen Mtell was able to provide notification of pending failures over 35 days in advance. With that amount of warning, the plant could have scheduled the shutdown at a more opportune time within the 35-day window, reducing downtime by as much as 8 days. They would also have saved over 30 percent on the repair costs by planning work in advance. The combined production and maintenance savings from these three events alone would have been more than $75 million. Seven anomaly agents and four failure agents were created for the compressor. These agents watched for a range of failure types, including piston and piston ring failures (38 days lead time), valve failures (24 days lead time) and lubricator failures (32 days lead time).
运营影响
数量效益
相关案例.
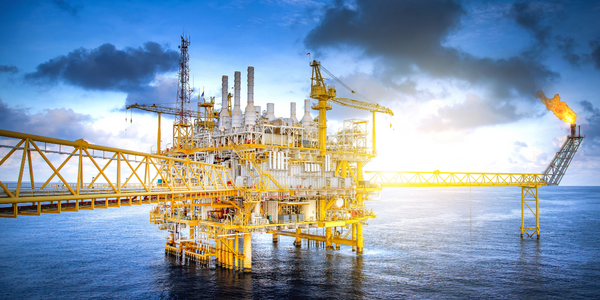
Case Study
Taking Oil and Gas Exploration to the Next Level
DownUnder GeoSolutions (DUG) wanted to increase computing performance by 5 to 10 times to improve seismic processing. The solution must build on current architecture software investments without sacrificing existing software and scale computing without scaling IT infrastructure costs.
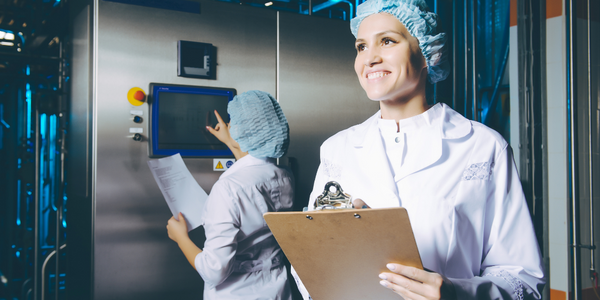
Case Study
Remote Wellhead Monitoring
Each wellhead was equipped with various sensors and meters that needed to be monitored and controlled from a central HMI, often miles away from the assets in the field. Redundant solar and wind generators were installed at each wellhead to support the electrical needs of the pumpstations, temperature meters, cameras, and cellular modules. In addition to asset management and remote control capabilities, data logging for remote surveillance and alarm notifications was a key demand from the customer. Terra Ferma’s solution needed to be power efficient, reliable, and capable of supporting high-bandwidth data-feeds. They needed a multi-link cellular connection to a central server that sustained reliable and redundant monitoring and control of flow meters, temperature sensors, power supply, and event-logging; including video and image files. This open-standard network needed to interface with the existing SCADA and proprietary network management software.
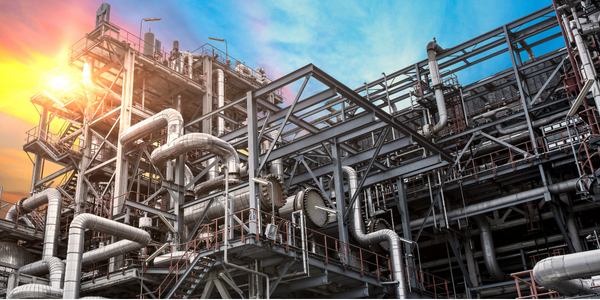
Case Study
Refinery Saves Over $700,000 with Smart Wireless
One of the largest petroleum refineries in the world is equipped to refine various types of crude oil and manufacture various grades of fuel from motor gasoline to Aviation Turbine Fuel. Due to wear and tear, eight hydrogen valves in each refinery were leaking, and each cost $1800 per ton of hydrogen vented. The plant also had leakage on nearly 30 flare control hydrocarbon valves. The refinery wanted a continuous, online monitoring system that could catch leaks early, minimize hydrogen and hydrocarbon production losses, and improve safety for maintenance.