下载PDF
DSV Gains Better Insight Into and Control Over Transport Thanks to MPO
技术
- 功能应用 - 运输管理系统 (TMS)
- 平台即服务 (PaaS) - 连接平台
适用功能
- 商业运营
- 物流运输
用例
- 车队管理
- 预测性维护
- 供应链可见性(SCV)
服务
- 软件设计与工程服务
- 系统集成
挑战
DSV Solutions faces the challenge of managing complex transport operations for a diverse range of clients across various sectors. The company needs to ensure cost savings, value addition, and optimal transparency for its customers. The logistics service provider handles high-value equipment in the hi-tech industry, hospital deliveries in the healthcare sector, and spare parts supply in the automotive sector, among other tasks. Managing these diverse requirements and ensuring accurate invoicing and performance tracking is a significant challenge.
关于客户
DSV Solutions is a logistics service provider that organizes transport for numerous customers across various sectors, including hi-tech, healthcare, automotive, industrial, and consumer products. The company goes beyond mere transportation by offering solutions that save costs and add value, such as consolidating orders and redesigning supply chains. DSV Solutions operates in a complex environment, handling high-value equipment, hospital deliveries, and spare parts supply, among other tasks. The company leverages a large network of transporters and partners to meet the diverse needs of its clients.
解决方案
DSV Solutions implemented the MPO Control Tower and Transportation Management System (TMS) to manage its transport activities. The MPO platform automates the freight settlement process by matching invoices against transport orders, ensuring that DSV never overpays. The platform also supports DSV's invoicing process, providing clear, consolidated invoices to customers based on their preferred billing metrics. Additionally, the MPO Control Tower allows DSV to compare carriers' performance against service level agreements, offering better insight into transport costs and profits. The software is also used for planning delivery routes, tracking consignments, and event management, enabling quick intervention when shipments do not progress as planned.
运营影响
数量效益
相关案例.
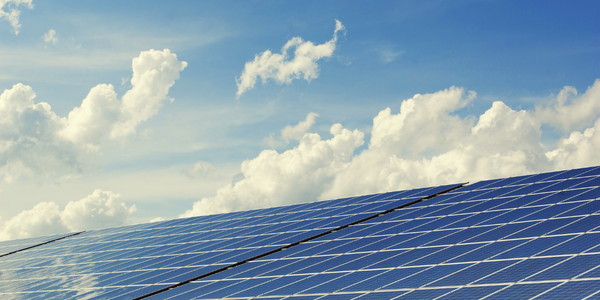
Case Study
Remote Monitoring & Predictive Maintenance App for a Solar Energy System
The maintenance & tracking of various modules was an overhead for the customer due to the huge labor costs involved. Being an advanced solar solutions provider, they wanted to ensure early detection of issues and provide the best-in-class customer experience. Hence they wanted to automate the whole process.
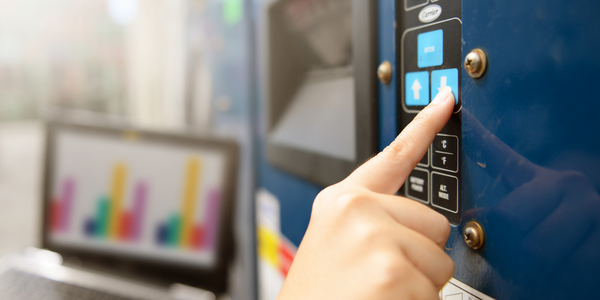
Case Study
Remote Temperature Monitoring of Perishable Goods Saves Money
RMONI was facing temperature monitoring challenges in a cold chain business. A cold chain must be established and maintained to ensure goods have been properly refrigerated during every step of the process, making temperature monitoring a critical business function. Manual registration practice can be very costly, labor intensive and prone to mistakes.
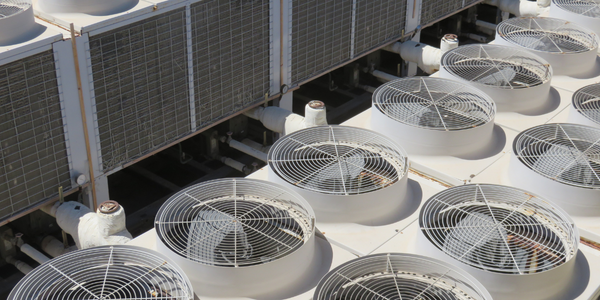
Case Study
Predictive Maintenance for Industrial Chillers
For global leaders in the industrial chiller manufacturing, reliability of the entire production process is of the utmost importance. Chillers are refrigeration systems that produce ice water to provide cooling for a process or industrial application. One of those leaders sought a way to respond to asset performance issues, even before they occur. The intelligence to guarantee maximum reliability of cooling devices is embedded (pre-alarming). A pre-alarming phase means that the cooling device still works, but symptoms may appear, telling manufacturers that a failure is likely to occur in the near future. Chillers who are not internet connected at that moment, provide little insight in this pre-alarming phase.
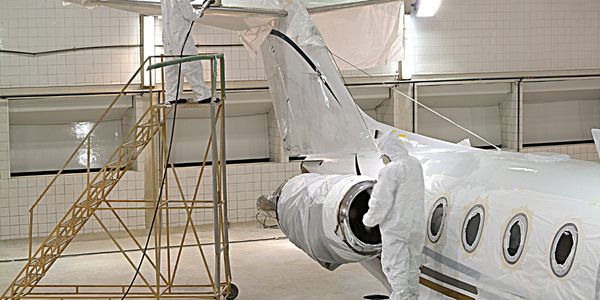
Case Study
Aircraft Predictive Maintenance and Workflow Optimization
First, aircraft manufacturer have trouble monitoring the health of aircraft systems with health prognostics and deliver predictive maintenance insights. Second, aircraft manufacturer wants a solution that can provide an in-context advisory and align job assignments to match technician experience and expertise.
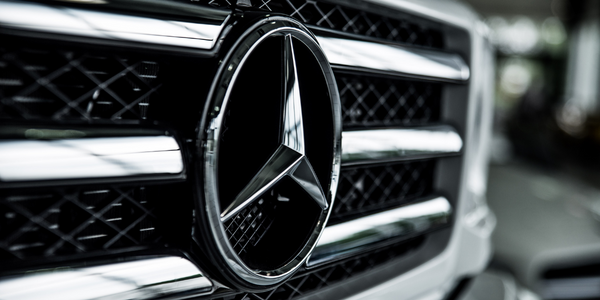
Case Study
Integral Plant Maintenance
Mercedes-Benz and his partner GAZ chose Siemens to be its maintenance partner at a new engine plant in Yaroslavl, Russia. The new plant offers a capacity to manufacture diesel engines for the Russian market, for locally produced Sprinter Classic. In addition to engines for the local market, the Yaroslavl plant will also produce spare parts. Mercedes-Benz Russia and his partner needed a service partner in order to ensure the operation of these lines in a maintenance partnership arrangement. The challenges included coordinating the entire maintenance management operation, in particular inspections, corrective and predictive maintenance activities, and the optimizing spare parts management. Siemens developed a customized maintenance solution that includes all electronic and mechanical maintenance activities (Integral Plant Maintenance).