下载PDF
Efficient Dump Design Saves Agnico Eagle $1.4 Million
技术
- 分析与建模 - 实时分析
适用行业
- 矿业
适用功能
- 离散制造
- 质量保证
用例
- 预测性维护
- 过程控制与优化
服务
- 培训
- 系统集成
挑战
Agnico Eagle’s Meadowbank gold mine in northern Canada was facing a challenge of integrating mine design and production schedules with geological modeling to increase in-house knowledge and ensure profitability. They were struggling with a competitive software solution for over a year and needed a more efficient and effective solution. The mine is Agnico eagle’s largest gold producer, with 1.8 million ounces of gold in proven and probable reserves since the open pit began in early 2010. The mine is one of the most complicated waste management sites in Canada with 14 dikes, 9 pits, multiple dumps and more than 100 haul routes. The mine was also looking to reduce production costs and needed to modify the long-range plans on-the-go ensuring they are up to date with current operations.
关于客户
Agnico Eagle is a gold mining company with mining operations in Canada, Mexico and Finland and exploration activities in Canada, Europe, Latin America and the United States. The company is headquartered in Toronto, Canada and has over 5,500 employees. The Meadowbank mine, located in the Kivalliq region of Nunavut, about 2,600 kilometers northwest of Toronto, is Agnico eagle’s largest gold producer, with 1.8 million ounces of gold in proven and probable reserves since the open pit began in early 2010. The mine is one of the most complicated waste management sites in Canada with 14 dikes, 9 pits, multiple dumps and more than 100 haul routes.
解决方案
Agnico Eagle implemented GEOVIA GEMS SQL, GEOVIA MineSched and GEOVIA Whittle with onsite GEOVIA Services training and assistance for life of mine estimation, life of mine production scenarios, pit optimization, pit designs and ore control. The implementation of these solutions was completed successfully with the help of a skilled GEMS power user onsite to train their staff. The staff uses GEMS SQL for pit design and road design infrastructure, and appreciates that it can handle the large amounts of data contained in their complex operation. The implementation of Whittle assisted with economic optimization of the pit design. The company also improved the layout and design of their in-pit dumps, which increased the capacity of the dump by 1.7 million tonnes, decreasing hauling and construction costs. The company also used MineSched for life of mine and medium-term planning.
运营影响
数量效益
相关案例.
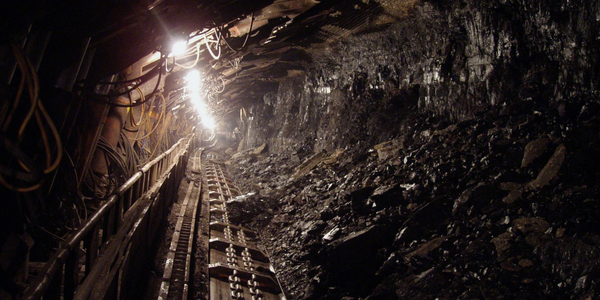
Case Study
Underground Mining Safety
The goal was to produce a safety system to monitor and support underground mining operations; existing systems were either too simple (i.e. phone line) or overly complex and expensive, inhibiting deployment, and providing little-to-no support in event of an accident. Given the dangerous nature of the mining work environment and the strict regulations placed on the industry, the solution would have to comply with Mine Safety and Health Administration (MSHA) regulations. Yet the product needed to allow for simple deployment to truly be a groundbreaking solution - increasing miner safety and changing daily operations for the better.
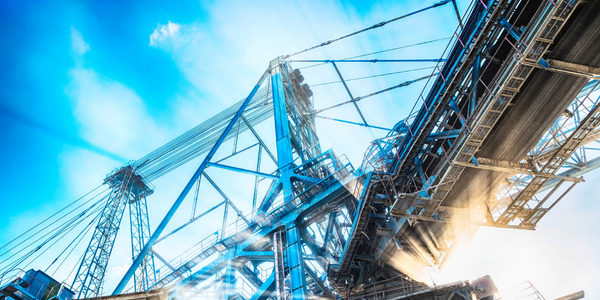
Case Study
Mining Firm Quadruples Production, with Internet of Everything
Dundee Precious Metal’s flagship mine, in Chelopech, Bulgaria, produces a gold, copper, and silver concentrate set a goal to increase production by 30%. Dundee wanted to increase production quality and output without increasing headcount and resources, improve miner safety, and minimize cost.
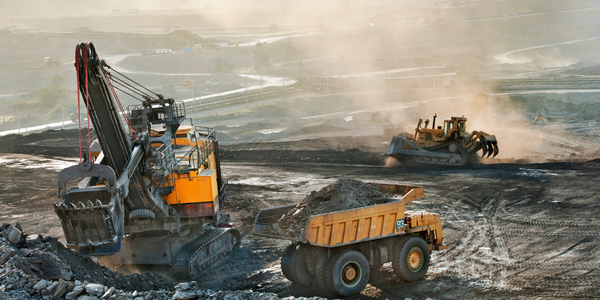
Case Study
Fastenal Builds the Future of Manufacturing with MachineMetrics
Fastenal's objective was to better understand their machine downtime, utilization, quality issues, and to embrace cutting-edge manufacturing technology/process improvement capabilities to bring their team to the next level. However, there was a lack of real-time data, visualization, and actionable insights made this transition impossible.
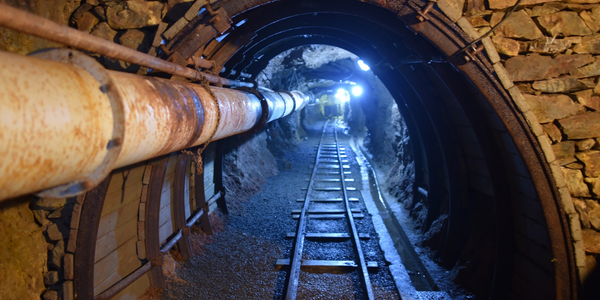
Case Study
Joy Mining Systems
Joy equipment faces many challenges. The first is machine integration and control. The business end of the machine has a rapidly-spinning cylinder with 6-inch diamond-studded cutting teeth. It chews through rock at rates measured in tens of tons per minute. The system grinds through the rock in front, creating a rectangular mine tunnel. Hydraulic lifters support the ceiling as the machine moves forward. Automated drills and screws drive 3-ft long screws into the ceiling to stabilize it. The rock and coal fall into a set of gathering "fingers" below the cutting cylinder. These fingers scoop up the rock and coal and deposit it onto a conveyor belt. The conveyor passes under the machine and out the back. A train of conveyor belt cars, up to a mile long, follows the cutter into the mine. The rock shoots along this train at over 400 feet per minute until it empties into rail cars at the end. Current systems place an operator cage next to the cutter. Choking dust (potentially explosive), the risk of collapse and the proximity of metal and rock mayhem make the operator cage a hazardous location.
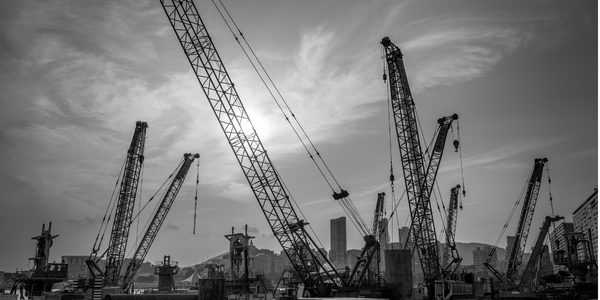
Case Study
Improved Monitoring in Industrial Manufacturing Facility
When your crane is moving tons of magma-hot iron, you can’t afford an unexpected failure. McWane Ductile knew monitoring the crane motor metrics within their facility could help prevent a mechanical failure that would strand an enormous bucket of molten metal overhead. Unfortunately, their legacy wired monitoring system couldn’t work with moving objects in this extreme environment. If they could integrate wireless capabilities into their existing equipment they could extend their monitoring capabilities without starting over from scratch.