下载PDF
Food Manufacturer Reduces Waste by Over 70% in Six Weeks
技术
- 分析与建模 - 实时分析
- 功能应用 - 制造执行系统 (MES)
- 功能应用 - 远程监控系统
适用行业
- 食品与饮料
适用功能
- 质量保证
- 流程制造
用例
- 机器状态监测
- 预测性维护
- 过程控制与优化
服务
- 软件设计与工程服务
- 系统集成
挑战
Dan Wadyka, Assistant Director of Quality Control at Giorgio Foods, faced a significant challenge. New company leadership was pushing for major growth and change, but some managers and supervisors felt that the current way of working was good enough. Production workers tracked product weights on the production line for frozen pizzas manually, recording data on paper. This manual process meant that line supervisors were only concerned with the current production run, and if problems arose, managers spent hours compiling hand-written data before they could make sense of what happened. The lack of timely information did not allow for impactful insights into production processes, leading to high costs from waste and overpack. Wadyka had an intuition that the impact was significant and inhibiting the growth of the business. He needed data to build momentum for change and appeal to his colleagues' heads and hearts.
关于客户
Giorgio Foods is a multi-plant manufacturer specializing in pizza and mushroom products. The company has a significant presence in the food manufacturing industry and is known for its high-quality products. Giorgio Foods employs over 1,000 people and operates multiple production lines to meet the demands of its customers. The company is committed to growth and innovation, driven by new leadership that aims to transform its operations. Giorgio Foods faced challenges in its production processes, particularly in managing waste and overfill, which were seen as normal and acceptable by some managers and supervisors. The company needed to adopt new technologies and processes to support its growth initiatives and improve operational efficiency.
解决方案
Wadyka partnered with Hertzler Systems to implement real-time weight control on the production line. The new system put tablets in operators' hands, guiding them to collect weight and compliance data at several points in the process. This real-time data collection allowed the team to monitor and control each ingredient and the final product weight. In just six weeks, Giorgio Foods saw a significant reduction in waste across the entire line. Low-cost items like pizza dough and tomato sauce saw a 70% reduction in waste and overfill, while high-cost items like meats and cheeses saw over an 80% reduction. The GainSeeker system provided the visibility needed to reduce waste and product giveaway. Employees could now interact with information instantly on a dashboard, giving them a complete view of the process and empowering them to act immediately to reduce overpack and waste.
运营影响
数量效益
相关案例.
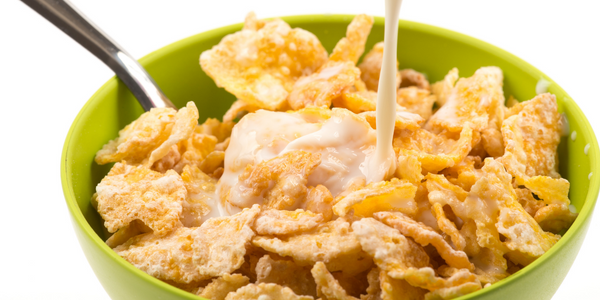
Case Study
The Kellogg Company
Kellogg keeps a close eye on its trade spend, analyzing large volumes of data and running complex simulations to predict which promotional activities will be the most effective. Kellogg needed to decrease the trade spend but its traditional relational database on premises could not keep up with the pace of demand.
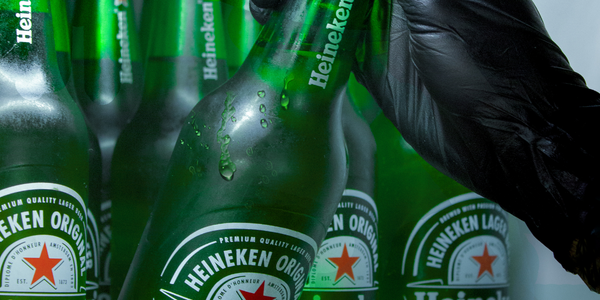
Case Study
HEINEKEN Uses the Cloud to Reach 10.5 Million Consumers
For 2012 campaign, the Bond promotion, it planned to launch the campaign at the same time everywhere on the planet. That created unprecedented challenges for HEINEKEN—nowhere more so than in its technology operation. The primary digital content for the campaign was a 100-megabyte movie that had to play flawlessly for millions of viewers worldwide. After all, Bond never fails. No one was going to tolerate a technology failure that might bruise his brand.Previously, HEINEKEN had supported digital media at its outsourced datacenter. But that datacenter lacked the computing resources HEINEKEN needed, and building them—especially to support peak traffic that would total millions of simultaneous hits—would have been both time-consuming and expensive. Nor would it have provided the geographic reach that HEINEKEN needed to minimize latency worldwide.
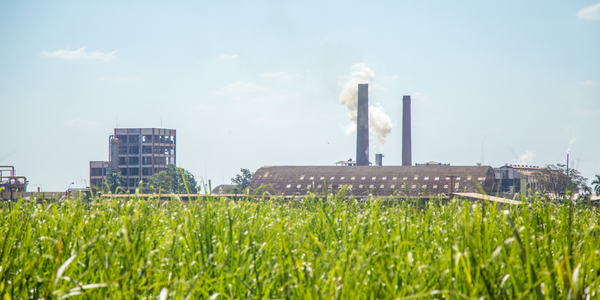
Case Study
Energy Management System at Sugar Industry
The company wanted to use the information from the system to claim under the renewable energy certificate scheme. The benefit to the company under the renewable energy certificates is Rs 75 million a year. To enable the above, an end-to-end solution for load monitoring, consumption monitoring, online data monitoring, automatic meter data acquisition which can be exported to SAP and other applications is required.
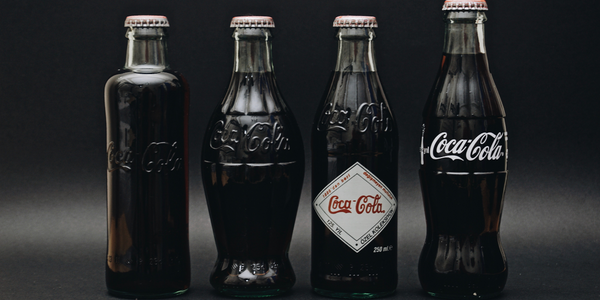
Case Study
Coca Cola Swaziland Conco Case Study
Coco Cola Swaziland, South Africa would like to find a solution that would enable the following results: - Reduce energy consumption by 20% in one year. - Formulate a series of strategic initiatives that would enlist the commitment of corporate management and create employee awareness while helping meet departmental targets and investing in tools that assist with energy management. - Formulate a series of tactical initiatives that would optimize energy usage on the shop floor. These would include charging forklifts and running cold rooms only during off-peak periods, running the dust extractors only during working hours and basing lights and air-conditioning on someone’s presence. - Increase visibility into the factory and other processes. - Enable limited, non-intrusive control functions for certain processes.
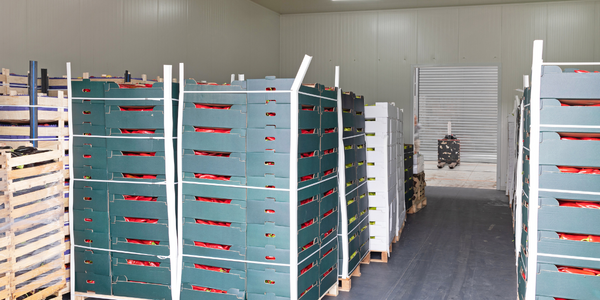
Case Study
Temperature Monitoring for Restaurant Food Storage
When it came to implementing a solution, Mr. Nesbitt had an idea of what functionality that he wanted. Although not mandated by Health Canada, Mr. Nesbitt wanted to ensure quality control issues met the highest possible standards as part of his commitment to top-of-class food services. This wish list included an easy-to use temperature-monitoring system that could provide a visible display of the temperatures of all of his refrigerators and freezers, including historical information so that he could review the performance of his equipment. It also had to provide alert notification (but email alerts and SMS text message alerts) to alert key staff in the event that a cooling system was exceeding pre-set warning limits.
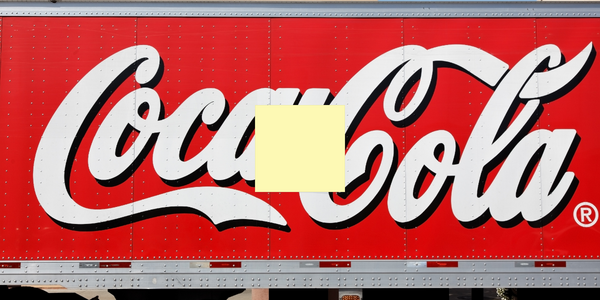
Case Study
Coca-Cola Refreshments, U.S.
Coca-Cola Refreshments owns and manages Coca-Cola branded refrigerators in retail establishments. Legacy systems were used to locate equipment information by logging onto multiple servers which took up to 8 hours to update information on 30-40 units. The company had no overall visibility into equipment status or maintenance history.