下载PDF
Global Brewery increases OEE by 5% with actionable insights from Parsable
技术
- 功能应用 - 远程监控系统
适用行业
- 食品与饮料
适用功能
- 维护
用例
- 远程资产管理
服务
- 系统集成
挑战
The global brewery was focused on product development, which resulted in the adoption of digital transformation processes taking a back seat. One of the major challenges was enabling operators on the floor to complete autonomous maintenance tasks, like clean/inspect/lubricate (CIL). The brewery had industry-standard CIL steps documented on laminated sheets of paper. However, these were rarely used and contained outdated images and information. There was no way to track if operators were completing the process or not – the data on CIL completion rates across teams and machines was inadequate. This resulted in a lack of confidence that the machines were being maintained at an optimal level and the inability to accurately track the completion of this critical procedure.
关于客户
The customer is a leading global brewery with a large portfolio of beer and other beverage brands, including soft drinks, water, and wine. The company has more than 40,000 employees and its products are sold in more than 150 markets around the world. The company has over 500 brands in its portfolio. The company is focused on product development and has been slow to adopt digital transformation processes.
解决方案
The Parsable Connected Worker Platform was implemented to fully digitize the brewery’s clean/inspect/lubricate procedures, resulting in increased adherence and visibility into the work performed. With Parsable’s Platform, a line worker can open a CIL job in the mobile app and follow clear instructions that contain interactive rich-media – inline videos, photos, GIFs and PDFs – on how to complete the task correctly. For operators performing a routine CIL inspection, they can log details of an equipment issue into Parsable’s mobile app and immediately share the information with a line leader or maintenance personnel. Supervisors have a real-time view into what is happening, and are able to provide a response to triage the issue. Management is able to see a summary of all CIL jobs in easy-to-understand dashboards. They can even hover over a specific station to see the status of a CIL, the time it was completed, how long it took and whether there were any issues raised. These insights can be viewed across machines and locations.
运营影响
数量效益
相关案例.
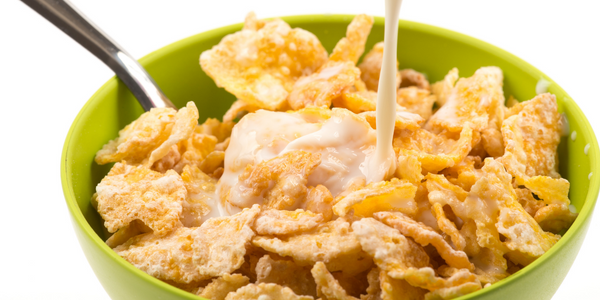
Case Study
The Kellogg Company
Kellogg keeps a close eye on its trade spend, analyzing large volumes of data and running complex simulations to predict which promotional activities will be the most effective. Kellogg needed to decrease the trade spend but its traditional relational database on premises could not keep up with the pace of demand.
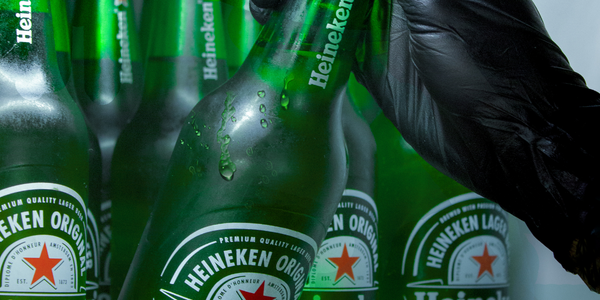
Case Study
HEINEKEN Uses the Cloud to Reach 10.5 Million Consumers
For 2012 campaign, the Bond promotion, it planned to launch the campaign at the same time everywhere on the planet. That created unprecedented challenges for HEINEKEN—nowhere more so than in its technology operation. The primary digital content for the campaign was a 100-megabyte movie that had to play flawlessly for millions of viewers worldwide. After all, Bond never fails. No one was going to tolerate a technology failure that might bruise his brand.Previously, HEINEKEN had supported digital media at its outsourced datacenter. But that datacenter lacked the computing resources HEINEKEN needed, and building them—especially to support peak traffic that would total millions of simultaneous hits—would have been both time-consuming and expensive. Nor would it have provided the geographic reach that HEINEKEN needed to minimize latency worldwide.
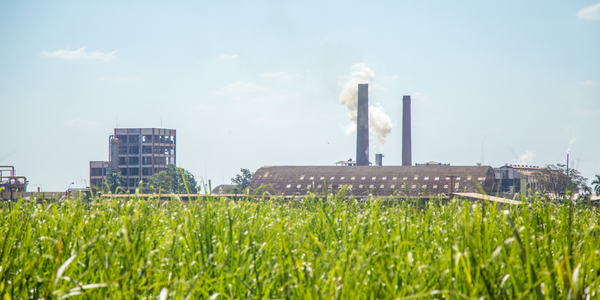
Case Study
Energy Management System at Sugar Industry
The company wanted to use the information from the system to claim under the renewable energy certificate scheme. The benefit to the company under the renewable energy certificates is Rs 75 million a year. To enable the above, an end-to-end solution for load monitoring, consumption monitoring, online data monitoring, automatic meter data acquisition which can be exported to SAP and other applications is required.
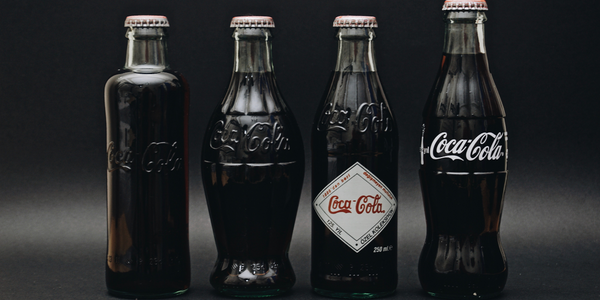
Case Study
Coca Cola Swaziland Conco Case Study
Coco Cola Swaziland, South Africa would like to find a solution that would enable the following results: - Reduce energy consumption by 20% in one year. - Formulate a series of strategic initiatives that would enlist the commitment of corporate management and create employee awareness while helping meet departmental targets and investing in tools that assist with energy management. - Formulate a series of tactical initiatives that would optimize energy usage on the shop floor. These would include charging forklifts and running cold rooms only during off-peak periods, running the dust extractors only during working hours and basing lights and air-conditioning on someone’s presence. - Increase visibility into the factory and other processes. - Enable limited, non-intrusive control functions for certain processes.
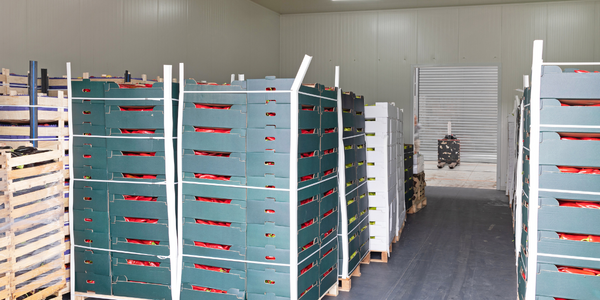
Case Study
Temperature Monitoring for Restaurant Food Storage
When it came to implementing a solution, Mr. Nesbitt had an idea of what functionality that he wanted. Although not mandated by Health Canada, Mr. Nesbitt wanted to ensure quality control issues met the highest possible standards as part of his commitment to top-of-class food services. This wish list included an easy-to use temperature-monitoring system that could provide a visible display of the temperatures of all of his refrigerators and freezers, including historical information so that he could review the performance of his equipment. It also had to provide alert notification (but email alerts and SMS text message alerts) to alert key staff in the event that a cooling system was exceeding pre-set warning limits.
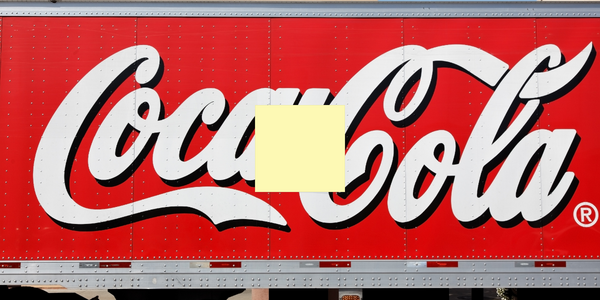
Case Study
Coca-Cola Refreshments, U.S.
Coca-Cola Refreshments owns and manages Coca-Cola branded refrigerators in retail establishments. Legacy systems were used to locate equipment information by logging onto multiple servers which took up to 8 hours to update information on 30-40 units. The company had no overall visibility into equipment status or maintenance history.