下载PDF
Global Dairy Manufacturer improves Quality and Safety with insights from Parsable
技术
- 分析与建模 - 实时分析
- 应用基础设施与中间件 - 数据交换与集成
适用行业
- 食品与饮料
适用功能
- 离散制造
- 质量保证
用例
- 实时定位系统 (RTLS)
- 根因分析与诊断
服务
- 软件设计与工程服务
- 系统集成
挑战
The company, one of the largest dairy manufacturers in the world, was facing hurdles in scaling its operations to meet growing demand. Outdated procedures and processes led to inconsistent data capture, impacting operational productivity, quality, and employee safety. The company's largest site produces different types of drinkable yogurts. For every batch of finished product, samples are sent to the quality lab for microbiology and physico-chemical testing. All lab results were recorded on paper and created large binders of data, which were then manually entered into SAP every 24 hours, leaving room for human error. The data reporting process took anywhere from seven to 30 days to uncover trends or identify if the production line was complying with quality standards. Additionally, a single safety inspector would walk around a production facility to conduct safety rounds and create Safety Behavior Observations (SBOs). These reports were filled out inconsistently and would sometimes get lost, resulting in considerable safety insurance premium costs.
关于客户
The customer is one of the largest dairy manufacturers in the world, producing a variety of products including milk, juice, cream, cheese, yogurt, and butter. The company is a billion-dollar entity with close to 38,000 employees. It has plants and distribution centers throughout the U.S., Mexico, Brazil, and Central America. The company has been in production for over 65 years and produces over 600 different products. The company's largest site produces different types of drinkable yogurts. The company is on a mission to create the world's best dairy products and is a fast-growing CPG brand.
解决方案
The company implemented Parsable to digitize its quality analysis and safety checks. Workers are now able to open the application on a mobile device and begin capturing data in real-time. With Parsable, data went from being processed and put into dashboards in seven to 30 days, to synchronized data every 24 hours with no data recapture. Safety checks have been transformed from static paper-based procedures into digital, interactive processes. If a worker identifies an unsafe condition or bad safety practice, they can receive in-the-moment training within the app-based work instructions, and identify improvements to make the operation safer.
运营影响
数量效益
相关案例.
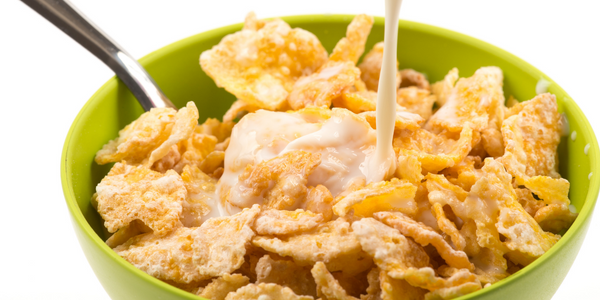
Case Study
The Kellogg Company
Kellogg keeps a close eye on its trade spend, analyzing large volumes of data and running complex simulations to predict which promotional activities will be the most effective. Kellogg needed to decrease the trade spend but its traditional relational database on premises could not keep up with the pace of demand.
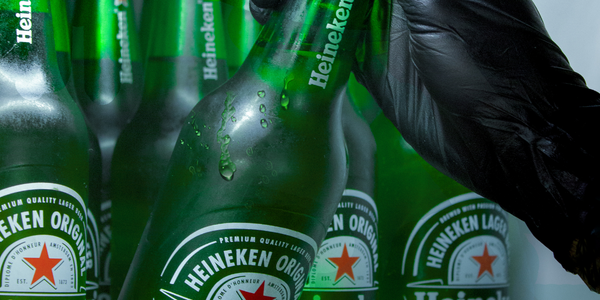
Case Study
HEINEKEN Uses the Cloud to Reach 10.5 Million Consumers
For 2012 campaign, the Bond promotion, it planned to launch the campaign at the same time everywhere on the planet. That created unprecedented challenges for HEINEKEN—nowhere more so than in its technology operation. The primary digital content for the campaign was a 100-megabyte movie that had to play flawlessly for millions of viewers worldwide. After all, Bond never fails. No one was going to tolerate a technology failure that might bruise his brand.Previously, HEINEKEN had supported digital media at its outsourced datacenter. But that datacenter lacked the computing resources HEINEKEN needed, and building them—especially to support peak traffic that would total millions of simultaneous hits—would have been both time-consuming and expensive. Nor would it have provided the geographic reach that HEINEKEN needed to minimize latency worldwide.
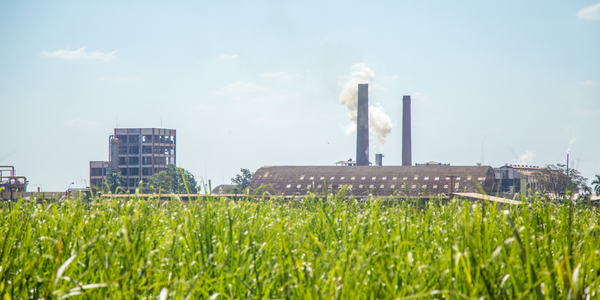
Case Study
Energy Management System at Sugar Industry
The company wanted to use the information from the system to claim under the renewable energy certificate scheme. The benefit to the company under the renewable energy certificates is Rs 75 million a year. To enable the above, an end-to-end solution for load monitoring, consumption monitoring, online data monitoring, automatic meter data acquisition which can be exported to SAP and other applications is required.
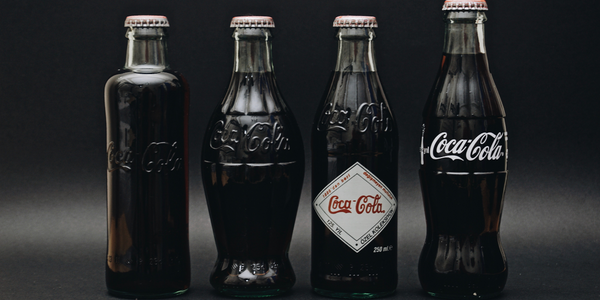
Case Study
Coca Cola Swaziland Conco Case Study
Coco Cola Swaziland, South Africa would like to find a solution that would enable the following results: - Reduce energy consumption by 20% in one year. - Formulate a series of strategic initiatives that would enlist the commitment of corporate management and create employee awareness while helping meet departmental targets and investing in tools that assist with energy management. - Formulate a series of tactical initiatives that would optimize energy usage on the shop floor. These would include charging forklifts and running cold rooms only during off-peak periods, running the dust extractors only during working hours and basing lights and air-conditioning on someone’s presence. - Increase visibility into the factory and other processes. - Enable limited, non-intrusive control functions for certain processes.
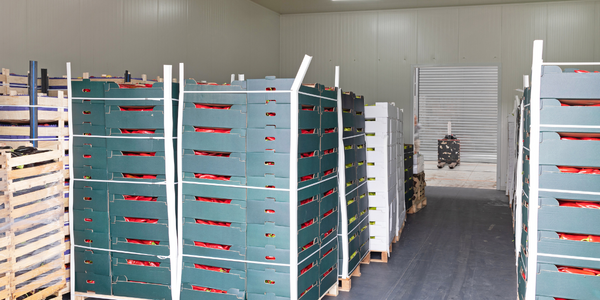
Case Study
Temperature Monitoring for Restaurant Food Storage
When it came to implementing a solution, Mr. Nesbitt had an idea of what functionality that he wanted. Although not mandated by Health Canada, Mr. Nesbitt wanted to ensure quality control issues met the highest possible standards as part of his commitment to top-of-class food services. This wish list included an easy-to use temperature-monitoring system that could provide a visible display of the temperatures of all of his refrigerators and freezers, including historical information so that he could review the performance of his equipment. It also had to provide alert notification (but email alerts and SMS text message alerts) to alert key staff in the event that a cooling system was exceeding pre-set warning limits.
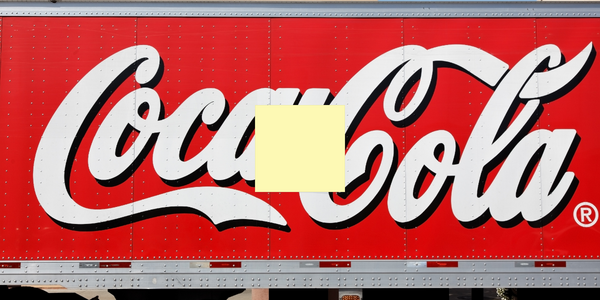
Case Study
Coca-Cola Refreshments, U.S.
Coca-Cola Refreshments owns and manages Coca-Cola branded refrigerators in retail establishments. Legacy systems were used to locate equipment information by logging onto multiple servers which took up to 8 hours to update information on 30-40 units. The company had no overall visibility into equipment status or maintenance history.