下载PDF
IFS Enables Future Growth for Heerema Fabrication Group
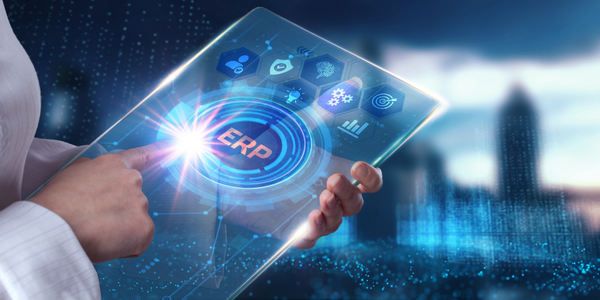
技术
- 分析与建模 - 过程分析
- 功能应用 - 企业资源规划系统 (ERP)
适用行业
- 水泥
- 石油和天然气
适用功能
- 设施管理
- 采购
用例
- 施工管理
- 快速原型制作
服务
- 系统集成
挑战
新的 ERP 软件是必要的,特别是为了支持 HFG 强调成为工程、采购、施工和安装 (EPC(I)) 和交钥匙合同的全球参与者的重点。
客户
Heerema 制造集团 (HFG)
关于客户
Heerema 制造集团 (HFG)是 Heerema 集团的一部分。 Heerema 集团为全球油气和能源行业设计、建造、运输、安装和拆除海上设施。在过去的几十年中,Heerema 已成为海上建筑行业的重要国际参与者。 HeeremaGroup 由两个部门组成:Heerema Fabrication Group (HFG) 和 Heerema Marine Contractors (HMC)。
解决方案
IFS 应用程序的使用使 HFG 能够制定未来计划并扩展其 EPC(I) 合同。
为 EPC(I) 项目的核心流程、与分包商的协作以及项目管理支持提供支持。
运营影响
数量效益
相关案例.
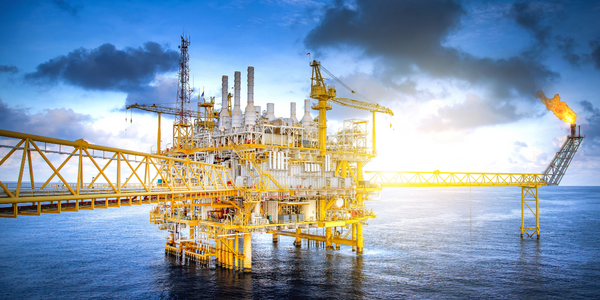
Case Study
Taking Oil and Gas Exploration to the Next Level
DownUnder GeoSolutions (DUG) wanted to increase computing performance by 5 to 10 times to improve seismic processing. The solution must build on current architecture software investments without sacrificing existing software and scale computing without scaling IT infrastructure costs.
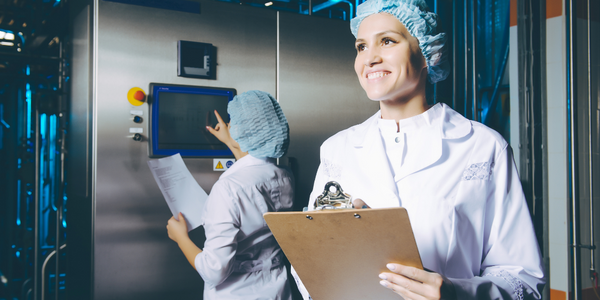
Case Study
Remote Wellhead Monitoring
Each wellhead was equipped with various sensors and meters that needed to be monitored and controlled from a central HMI, often miles away from the assets in the field. Redundant solar and wind generators were installed at each wellhead to support the electrical needs of the pumpstations, temperature meters, cameras, and cellular modules. In addition to asset management and remote control capabilities, data logging for remote surveillance and alarm notifications was a key demand from the customer. Terra Ferma’s solution needed to be power efficient, reliable, and capable of supporting high-bandwidth data-feeds. They needed a multi-link cellular connection to a central server that sustained reliable and redundant monitoring and control of flow meters, temperature sensors, power supply, and event-logging; including video and image files. This open-standard network needed to interface with the existing SCADA and proprietary network management software.
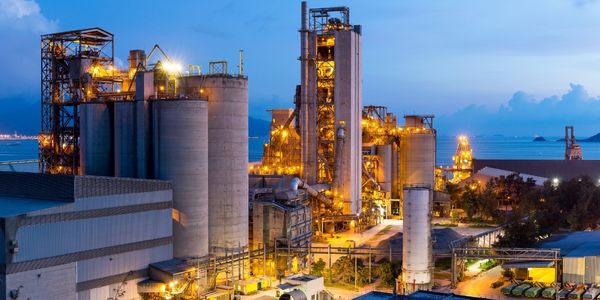
Case Study
System 800xA at Indian Cement Plants
Chettinad Cement recognized that further efficiencies could be achieved in its cement manufacturing process. It looked to investing in comprehensive operational and control technologies to manage and derive productivity and energy efficiency gains from the assets on Line 2, their second plant in India.
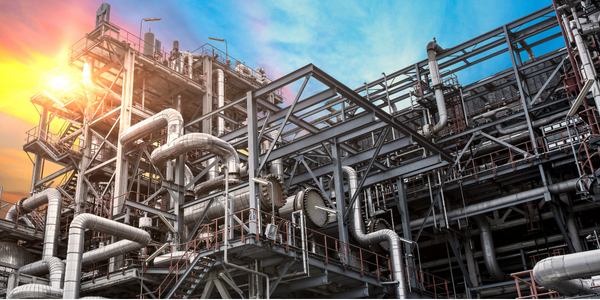
Case Study
Refinery Saves Over $700,000 with Smart Wireless
One of the largest petroleum refineries in the world is equipped to refine various types of crude oil and manufacture various grades of fuel from motor gasoline to Aviation Turbine Fuel. Due to wear and tear, eight hydrogen valves in each refinery were leaking, and each cost $1800 per ton of hydrogen vented. The plant also had leakage on nearly 30 flare control hydrocarbon valves. The refinery wanted a continuous, online monitoring system that could catch leaks early, minimize hydrogen and hydrocarbon production losses, and improve safety for maintenance.