下载PDF
Kalalou Case Study
技术
- 分析与建模 - 实时分析
- 平台即服务 (PaaS) - 数据管理平台
适用行业
- 零售
适用功能
- 物流运输
- 仓库和库存管理
用例
- 库存管理
- 仓库自动化
服务
- 系统集成
- 培训
挑战
In 2008, Kalalou, like many wholesale companies at the time, was manually receiving and processing inventory with paper-based systems. It needed a better way to allocate inventory and work with back orders and releases. In addition, the company was looking to improve how it dealt with containers with multiple purchase orders, receiving, and to better manage overall warehouse operations, including cube utilization, efficient rack positioning, stock rotation, and inventory placement. The company has four onsite warehouses and one offsite, and routinely maintains approximately 80 trailers of merchandise onsite. Because it has so many yard-based trailers in addition to its main warehouses, the company faced issues with replenishment to and from offsite facilities and yard-based trailers. Manual cycle counting also affected the accuracy of inventory quantities.
关于客户
Kalalou is a leading designer and supplier of home accents, garden decor, and gifts. For more than 30 years, the company has brought international products to the U.S. market. It is committed to working with recycled/sustainable materials and dedicated to improving the lives of those with whom it works through its Doug and Susan’s Kid Foundation. Kalalou delivers its products via three channels: Wholesale to big home décor companies and brick-and-mortar boutiques & gift shops, Direct-to-consumers via its eCommerce store, At West End, Drop-shipping for D2C customers.
解决方案
Since implementing ShipHawk WMS (formerly SuiteWM) in 2009, Kalalou has achieved a wide variety of efficiencies and improved productivity outcomes. As it replaced manual processes with automation, Kalalou now uses handheld wireless devices to effortlessly receive goods against multiple purchase order (PO) advanced shipping notices (ASNs). Using ShipHawk WMS, the company now has visibility into the entire process, meaning they can utilize the real-time data and make decisions throughout the day. Once their inventory is offloaded, the team uses handheld devices for efficient directed-put away to consolidate inventory in storage and maximize cube utilization and placement. Most of Kalalou’s POs aren’t single orders or for single suppliers, so the warehouse team often makes consolidations and being able to track them in the system is instrumental in staying on top of inventory.
运营影响
数量效益
相关案例.
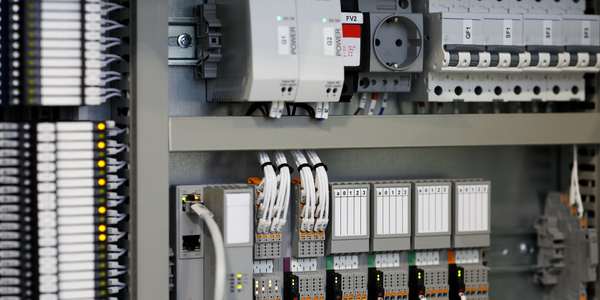
Case Study
Improving Production Line Efficiency with Ethernet Micro RTU Controller
Moxa was asked to provide a connectivity solution for one of the world's leading cosmetics companies. This multinational corporation, with retail presence in 130 countries, 23 global braches, and over 66,000 employees, sought to improve the efficiency of their production process by migrating from manual monitoring to an automatic productivity monitoring system. The production line was being monitored by ABB Real-TPI, a factory information system that offers data collection and analysis to improve plant efficiency. Due to software limitations, the customer needed an OPC server and a corresponding I/O solution to collect data from additional sensor devices for the Real-TPI system. The goal is to enable the factory information system to more thoroughly collect data from every corner of the production line. This will improve its ability to measure Overall Equipment Effectiveness (OEE) and translate into increased production efficiencies. System Requirements • Instant status updates while still consuming minimal bandwidth to relieve strain on limited factory networks • Interoperable with ABB Real-TPI • Small form factor appropriate for deployment where space is scarce • Remote software management and configuration to simplify operations
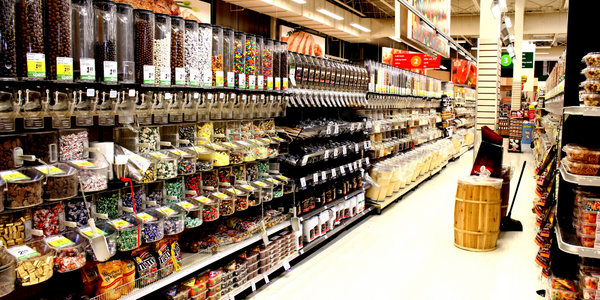
Case Study
How Sirqul’s IoT Platform is Crafting Carrefour’s New In-Store Experiences
Carrefour Taiwan’s goal is to be completely digital by end of 2018. Out-dated manual methods for analysis and assumptions limited Carrefour’s ability to change the customer experience and were void of real-time decision-making capabilities. Rather than relying solely on sales data, assumptions, and disparate systems, Carrefour Taiwan’s CEO led an initiative to find a connected IoT solution that could give the team the ability to make real-time changes and more informed decisions. Prior to implementing, Carrefour struggled to address their conversion rates and did not have the proper insights into the customer decision-making process nor how to make an immediate impact without losing customer confidence.
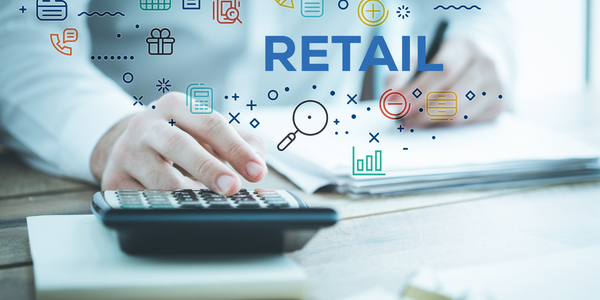
Case Study
Digital Retail Security Solutions
Sennco wanted to help its retail customers increase sales and profits by developing an innovative alarm system as opposed to conventional connected alarms that are permanently tethered to display products. These traditional security systems were cumbersome and intrusive to the customer shopping experience. Additionally, they provided no useful data or analytics.
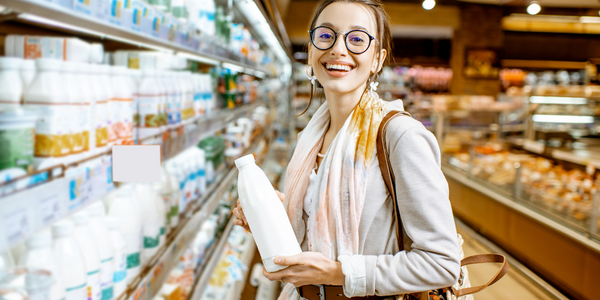
Case Study
Ensures Cold Milk in Your Supermarket
As of 2014, AK-Centralen has over 1,500 Danish supermarkets equipped, and utilizes 16 operators, and is open 24 hours a day, 365 days a year. AK-Centralen needed the ability to monitor the cooling alarms from around the country, 24 hours a day, 365 days a year. Each and every time the door to a milk cooler or a freezer does not close properly, an alarm goes off on a computer screen in a control building in southwestern Odense. This type of alarm will go off approximately 140,000 times per year, equating to roughly 400 alarms in a 24-hour period. Should an alarm go off, then there is only a limited amount of time to act before dairy products or frozen pizza must be disposed of, and this type of waste can quickly start to cost a supermarket a great deal of money.
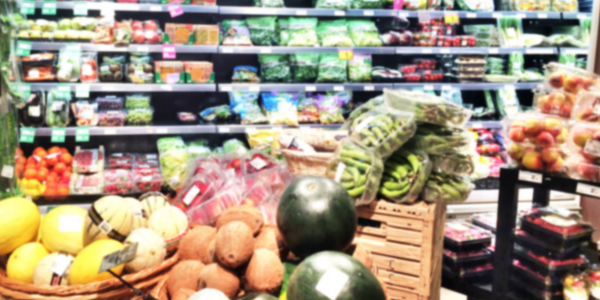
Case Study
Supermarket Energy Savings
The client had previously deployed a one-meter-per-store monitoring program. Given the manner in which energy consumption changes with external temperature, hour of the day, day of week and month of year, a single meter solution lacked the ability to detect the difference between a true problem and a changing store environment. Most importantly, a single meter solution could never identify root cause of energy consumption changes. This approach never reduced the number of truck-rolls or man-hours required to find and resolve issues.