下载PDF
Manage Analytics Challenges with Sisense for Custom Furnishings and E-commerce
技术
- 分析与建模 - 大数据分析
- 应用基础设施与中间件 - 数据可视化
- 应用基础设施与中间件 - 数据交换与集成
适用行业
- 电子商务
- 零售
适用功能
- 商业运营
- 销售与市场营销
服务
- 系统集成
- 软件设计与工程服务
挑战
As the company grew, Online Commerce Group’s data become so large that, without a new generation Big Data Analytics solution, management couldn’t receive quality reports. The fast growth of the company meant that Data Manager Paul Auen was unable to run reports with large enough data sets to provide any real value to the business end. “Originally, we could do reports manually, but as the data sets got larger, the reports took longer and impacted the transactional database,” Auen recalled. “We were constrained between keeping the servers running or making it available for reports.” Online Commerce Group chose a popular business analytics tool, but it was too complex; Auen’s group was unable to run reports at the speed and frequency needed for the business. Quickly, the team abandoned and turned to Sisense. The company needed a solution that could: 1. Quickly analyze large data sets coming from multiple sources. 2. Provide drag-and-drop modeling and dashboard creation for business users. 3. Automatically generate reports and publish them to the company intranet. 4. Require a minimal capital investment and learning curve for use.
关于客户
Since 2004, Montgomery, Alabama-based Online Commerce Group has specialized in upscale outdoor and indoor living space products for both residential and commercial markets. With a diversified portfolio of over 50 retail websites including CushionSource.com, Online Commerce Group sells custom-made furnishings and accents and has ranked for three years straight in Inc. magazine’s fastest-growing privately-held companies in the United States.
解决方案
Paul Auen’s team began evaluating traditional business intelligence platforms, but when he heard about Sisense as an up-and-comer in the Big Data Analytics space, he was intrigued and decided to test out the solution; he threw all his data at it, and soon was impressed. “We could easily import our data structure’s model without scripting, quickly build dashboards, and share analytics in minutes. We could do all that with the free trial before we had to put any money into it,” he said. “We could prove Sisense worked before we had to make an investment in it.” Auen appreciated the out-of-the box aspect of the Sisense solution – in one package, the solution provided a high-performance analytical database, along with reporting capabilities any business user could use to work with large data sets ad-hoc. Once he installed the software, he configured it to make sure it was connected to the many data sets Online Commerce Group uses. Deployment was so efficient that Auen was able to run reports on day 1, without training. This was far from the experience he had had with traditional vendors or even the more modern in-memory or visualization vendors. Auen can now accommodate his need to work with data in a constant state of change. No matter how data changes in structure, Auen can swap out dimensions and create reports by customer, website, or salesperson without having to completely rewrite the report. Data size is not an issue either – Auen can breeze through half-a-terabyte of data in minutes on standard hardware. This is important, as his need for real-time analytics has grown: reports to management and teams are automatically published to the company intranet – without bogging down the server.
运营影响
数量效益
相关案例.
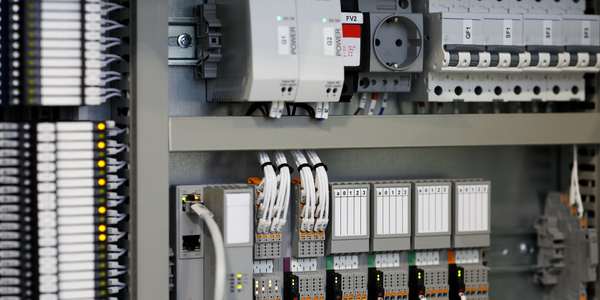
Case Study
Improving Production Line Efficiency with Ethernet Micro RTU Controller
Moxa was asked to provide a connectivity solution for one of the world's leading cosmetics companies. This multinational corporation, with retail presence in 130 countries, 23 global braches, and over 66,000 employees, sought to improve the efficiency of their production process by migrating from manual monitoring to an automatic productivity monitoring system. The production line was being monitored by ABB Real-TPI, a factory information system that offers data collection and analysis to improve plant efficiency. Due to software limitations, the customer needed an OPC server and a corresponding I/O solution to collect data from additional sensor devices for the Real-TPI system. The goal is to enable the factory information system to more thoroughly collect data from every corner of the production line. This will improve its ability to measure Overall Equipment Effectiveness (OEE) and translate into increased production efficiencies. System Requirements • Instant status updates while still consuming minimal bandwidth to relieve strain on limited factory networks • Interoperable with ABB Real-TPI • Small form factor appropriate for deployment where space is scarce • Remote software management and configuration to simplify operations
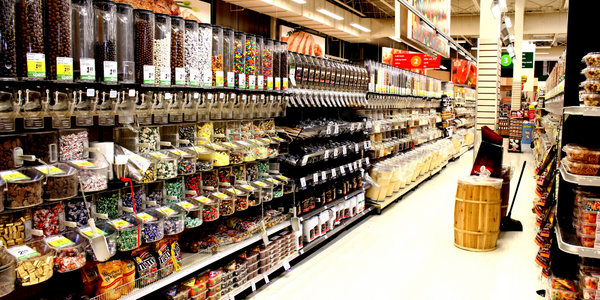
Case Study
How Sirqul’s IoT Platform is Crafting Carrefour’s New In-Store Experiences
Carrefour Taiwan’s goal is to be completely digital by end of 2018. Out-dated manual methods for analysis and assumptions limited Carrefour’s ability to change the customer experience and were void of real-time decision-making capabilities. Rather than relying solely on sales data, assumptions, and disparate systems, Carrefour Taiwan’s CEO led an initiative to find a connected IoT solution that could give the team the ability to make real-time changes and more informed decisions. Prior to implementing, Carrefour struggled to address their conversion rates and did not have the proper insights into the customer decision-making process nor how to make an immediate impact without losing customer confidence.
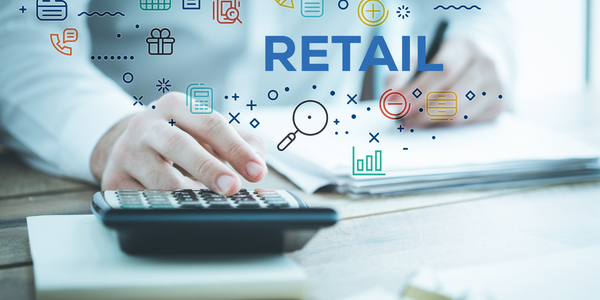
Case Study
Digital Retail Security Solutions
Sennco wanted to help its retail customers increase sales and profits by developing an innovative alarm system as opposed to conventional connected alarms that are permanently tethered to display products. These traditional security systems were cumbersome and intrusive to the customer shopping experience. Additionally, they provided no useful data or analytics.
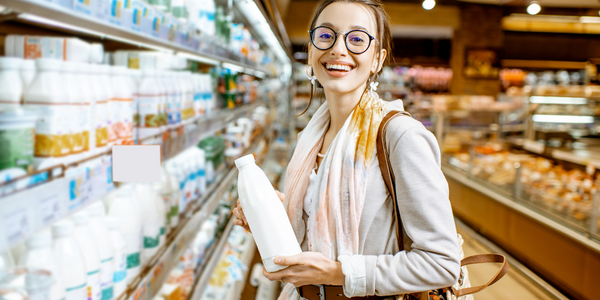
Case Study
Ensures Cold Milk in Your Supermarket
As of 2014, AK-Centralen has over 1,500 Danish supermarkets equipped, and utilizes 16 operators, and is open 24 hours a day, 365 days a year. AK-Centralen needed the ability to monitor the cooling alarms from around the country, 24 hours a day, 365 days a year. Each and every time the door to a milk cooler or a freezer does not close properly, an alarm goes off on a computer screen in a control building in southwestern Odense. This type of alarm will go off approximately 140,000 times per year, equating to roughly 400 alarms in a 24-hour period. Should an alarm go off, then there is only a limited amount of time to act before dairy products or frozen pizza must be disposed of, and this type of waste can quickly start to cost a supermarket a great deal of money.
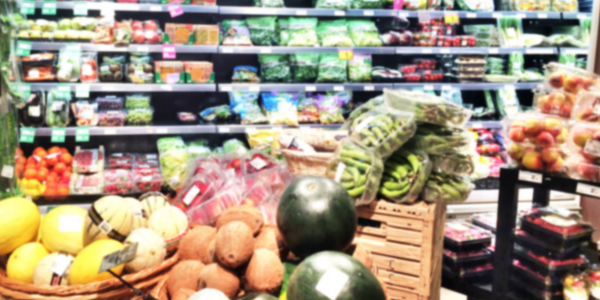
Case Study
Supermarket Energy Savings
The client had previously deployed a one-meter-per-store monitoring program. Given the manner in which energy consumption changes with external temperature, hour of the day, day of week and month of year, a single meter solution lacked the ability to detect the difference between a true problem and a changing store environment. Most importantly, a single meter solution could never identify root cause of energy consumption changes. This approach never reduced the number of truck-rolls or man-hours required to find and resolve issues.