下载PDF
National Oilwell Varco uses PTC University’s eLearning and assessment solutions to improve design and accountability
技术
- 功能应用 - 企业资源规划系统 (ERP)
适用行业
- 石油和天然气
适用功能
- 产品研发
- 质量保证
用例
- 预测性维护
- 自动化制造系统
服务
- 培训
- 软件设计与工程服务
挑战
National Oilwell Varco's Pressure Control Group (PCG) was facing challenges in training and assessing its engineers to ensure they design quality products, meet regulatory requirements, and follow strict internal guidelines. The traditional industry practice of pairing new hires with mentors was proving inadequate due to the mentors' own project commitments. The lack of formalized training and accountability led to significant rework, slowing the design process and potentially impacting product quality. The company needed a paradigm shift in its training approach to improve engineering quality and accountability. Additionally, the company was struggling to deliver on a tremendous backlog of business due to substantial business growth over the past several years.
关于客户
National Oilwell Varco (NOV) is a worldwide leader in oilfield products and services, based in Houston, Texas. Established in 1841, the company has a long history of providing innovative solutions to the oil and gas industry. NOV's Pressure Control Group (PCG) designs products that improve drilling safety by preventing oil well blowouts and controlling wells during drilling operations. The company has been using PTC's products for over 20 years, with PTC Creo being the primary design tool for the PCG for more than a decade. NOV aims to technically dominate its industry and produce robust and reliable products that are designed right the first time.
解决方案
NOV instituted a global initiative, the NOV Competency Management System (CMS), to train engineers in design best practices and demonstrate their competence. PTC University played an integral role in the PCG’s CMS, providing management and assessment tools to assist their efforts to train employees and evaluate their skills. The CMS used PTC’s eLearning courses to develop a series of learning paths tailored to the needs of different roles. The CMS also used ModelCHECK and PTC University’s Pro/FICIENCY and Expert Model Analysis (XMA) tools to evaluate the skills of new hires and current employees as well as assess their progress and design quality after completing training courses. The CMS tailors PTC training and assessments to three different types of individuals: new hires right out of college, experienced new hires, and existing staff.
运营影响
数量效益
相关案例.
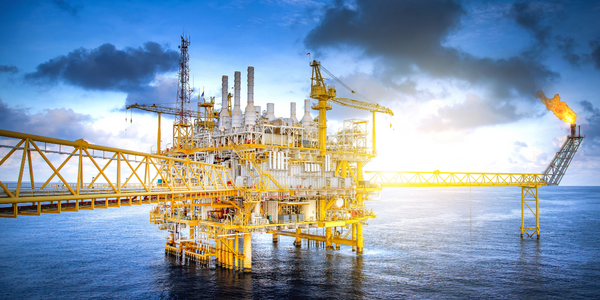
Case Study
Taking Oil and Gas Exploration to the Next Level
DownUnder GeoSolutions (DUG) wanted to increase computing performance by 5 to 10 times to improve seismic processing. The solution must build on current architecture software investments without sacrificing existing software and scale computing without scaling IT infrastructure costs.
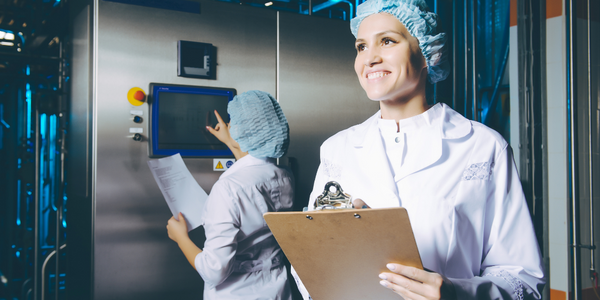
Case Study
Remote Wellhead Monitoring
Each wellhead was equipped with various sensors and meters that needed to be monitored and controlled from a central HMI, often miles away from the assets in the field. Redundant solar and wind generators were installed at each wellhead to support the electrical needs of the pumpstations, temperature meters, cameras, and cellular modules. In addition to asset management and remote control capabilities, data logging for remote surveillance and alarm notifications was a key demand from the customer. Terra Ferma’s solution needed to be power efficient, reliable, and capable of supporting high-bandwidth data-feeds. They needed a multi-link cellular connection to a central server that sustained reliable and redundant monitoring and control of flow meters, temperature sensors, power supply, and event-logging; including video and image files. This open-standard network needed to interface with the existing SCADA and proprietary network management software.
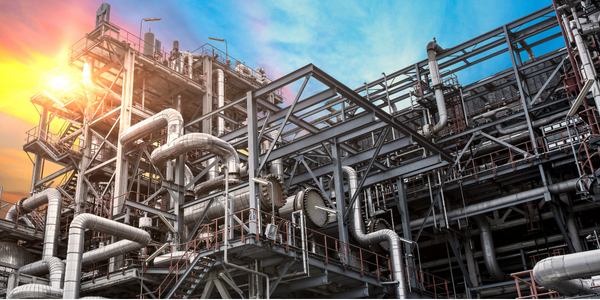
Case Study
Refinery Saves Over $700,000 with Smart Wireless
One of the largest petroleum refineries in the world is equipped to refine various types of crude oil and manufacture various grades of fuel from motor gasoline to Aviation Turbine Fuel. Due to wear and tear, eight hydrogen valves in each refinery were leaking, and each cost $1800 per ton of hydrogen vented. The plant also had leakage on nearly 30 flare control hydrocarbon valves. The refinery wanted a continuous, online monitoring system that could catch leaks early, minimize hydrogen and hydrocarbon production losses, and improve safety for maintenance.