下载PDF
Optimizing Autonomous Driving with IoT: A Case Study of Woven Planet and Pachyderm
技术
- 分析与建模 - 机器学习
- 应用基础设施与中间件 - API 集成与管理
适用行业
- 汽车
- 石油和天然气
用例
- 自主运输系统
- 预测性维护
服务
- 数据科学服务
- 系统集成
挑战
Woven Planet 的自动测绘团队面临着开发汽车级地图的挑战,其详细程度、准确度和精确度远远超出消费级地图。他们需要处理大陆范围内的大量航空和卫星数据,以满足自动驾驶的要求。
关于客户
Woven Planet 是丰田的子公司,专注于为自动驾驶构建最安全的移动解决方案。他们投资新技术、软件和商业模式,为所有人提供安全、互联、可靠和可持续的移动解决方案。
解决方案
Woven Planet 选择 Pachyderm 作为他们的编排系统来支持他们的自动绘图团队。 Pachyderm 提供最大的灵活性,使团队能够扩展以满足弹性工作负载,并在结构化和非结构化数据集之间轻松切换。它还为基于区域的连续地图更新提供长期的管道稳定性。
运营影响
数量效益
相关案例.
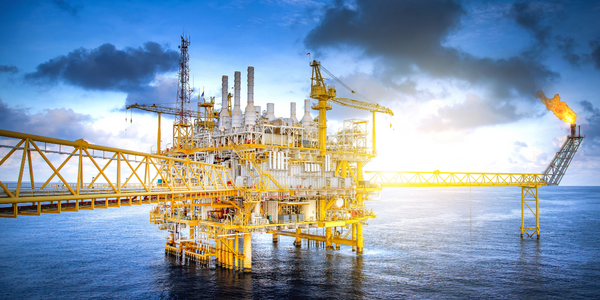
Case Study
Taking Oil and Gas Exploration to the Next Level
DownUnder GeoSolutions (DUG) wanted to increase computing performance by 5 to 10 times to improve seismic processing. The solution must build on current architecture software investments without sacrificing existing software and scale computing without scaling IT infrastructure costs.
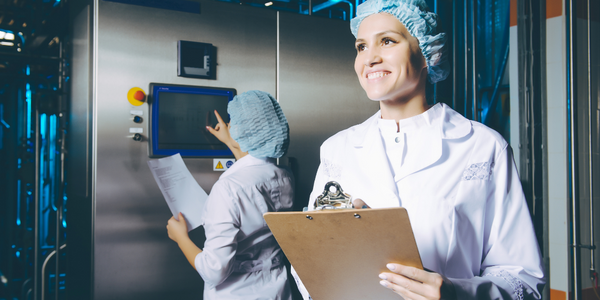
Case Study
Remote Wellhead Monitoring
Each wellhead was equipped with various sensors and meters that needed to be monitored and controlled from a central HMI, often miles away from the assets in the field. Redundant solar and wind generators were installed at each wellhead to support the electrical needs of the pumpstations, temperature meters, cameras, and cellular modules. In addition to asset management and remote control capabilities, data logging for remote surveillance and alarm notifications was a key demand from the customer. Terra Ferma’s solution needed to be power efficient, reliable, and capable of supporting high-bandwidth data-feeds. They needed a multi-link cellular connection to a central server that sustained reliable and redundant monitoring and control of flow meters, temperature sensors, power supply, and event-logging; including video and image files. This open-standard network needed to interface with the existing SCADA and proprietary network management software.
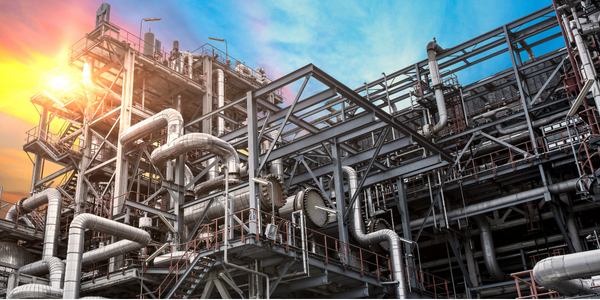
Case Study
Refinery Saves Over $700,000 with Smart Wireless
One of the largest petroleum refineries in the world is equipped to refine various types of crude oil and manufacture various grades of fuel from motor gasoline to Aviation Turbine Fuel. Due to wear and tear, eight hydrogen valves in each refinery were leaking, and each cost $1800 per ton of hydrogen vented. The plant also had leakage on nearly 30 flare control hydrocarbon valves. The refinery wanted a continuous, online monitoring system that could catch leaks early, minimize hydrogen and hydrocarbon production losses, and improve safety for maintenance.
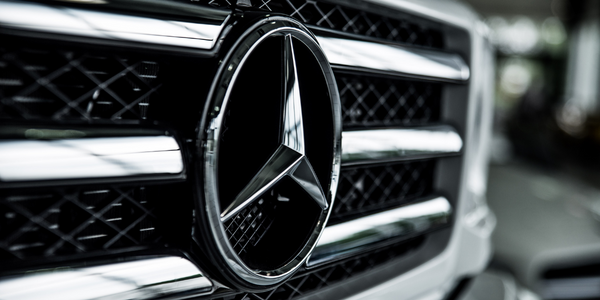
Case Study
Integral Plant Maintenance
Mercedes-Benz and his partner GAZ chose Siemens to be its maintenance partner at a new engine plant in Yaroslavl, Russia. The new plant offers a capacity to manufacture diesel engines for the Russian market, for locally produced Sprinter Classic. In addition to engines for the local market, the Yaroslavl plant will also produce spare parts. Mercedes-Benz Russia and his partner needed a service partner in order to ensure the operation of these lines in a maintenance partnership arrangement. The challenges included coordinating the entire maintenance management operation, in particular inspections, corrective and predictive maintenance activities, and the optimizing spare parts management. Siemens developed a customized maintenance solution that includes all electronic and mechanical maintenance activities (Integral Plant Maintenance).